Wzrost efektywności energetycznej instalacji przemysłowych dzięki poprawie izolacyjności
Cz. 1. Wymagania prawne i metody oceny skuteczności

Wzrost efektywności energetycznej instalacji przemysłowych
Wszelkie działania inwestycyjne w zakresie termomodernizacji wymagają od osób podejmujących takie decyzje uzasadnienia ekonomicznego.
W drugim rzędzie istotne jest wykazanie innych efektów towarzyszących, takich jak zmniejszenie negatywnego oddziaływania na środowisko, zwiększenie sprawności technicznej pracujących maszyn i urządzeń, zwiększenie produktywności czy wydajności.
Zobacz także
Saint-Gobain Construction Products Polska/ Isover U Protect – innowacyjny system ognioodpornej izolacji kanałów
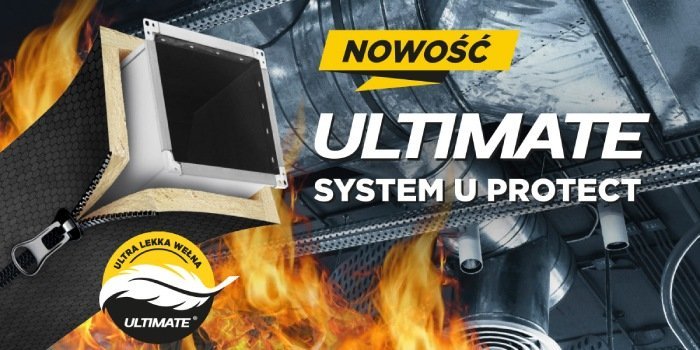
System ochrony przeciwpożarowej kanałów wentylacyjnych i przewodów oddymiających, stosowany od 10 lat przez wykonawców w ponad 20 krajach europejskich, jest już dostępny również na polskim rynku. Zalety...
System ochrony przeciwpożarowej kanałów wentylacyjnych i przewodów oddymiających, stosowany od 10 lat przez wykonawców w ponad 20 krajach europejskich, jest już dostępny również na polskim rynku. Zalety U Protect to niewielki ciężar oraz łatwość montażu. Rozwiązanie firmy Isover wyróżnia ochrona przeciwpożarowa nawet do 2 godzin.
PETRALANA Zastosowanie przeciwogniowe, termiczne, akustyczne – płyty PETRATOP i PETRALAMELA-FG
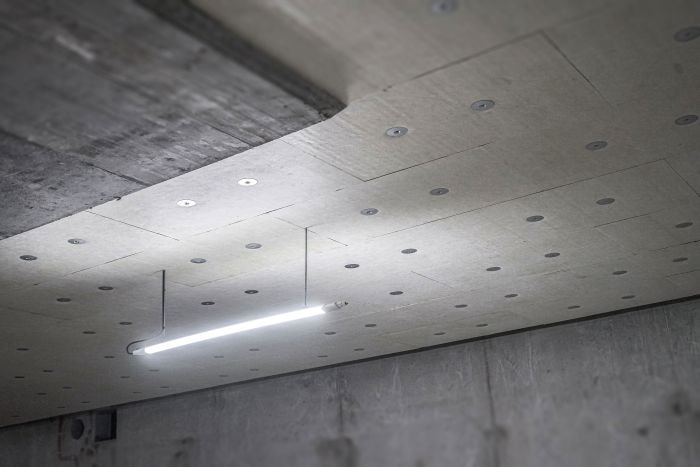
PETRATOP i PETRALAMELA-FG to produkty stworzone z myślą o efektywnej izolacji termicznej oraz akustycznej oraz bezpieczeństwie pożarowym garaży i piwnic. Rozwiązanie to zapobiega wymianie wysokiej temperatury...
PETRATOP i PETRALAMELA-FG to produkty stworzone z myślą o efektywnej izolacji termicznej oraz akustycznej oraz bezpieczeństwie pożarowym garaży i piwnic. Rozwiązanie to zapobiega wymianie wysokiej temperatury z górnych kondygnacji budynków z niską temperaturą, która panuje bliżej gruntu.
Przemysław Gogojewicz Kanały technologiczne i ich usytuowanie
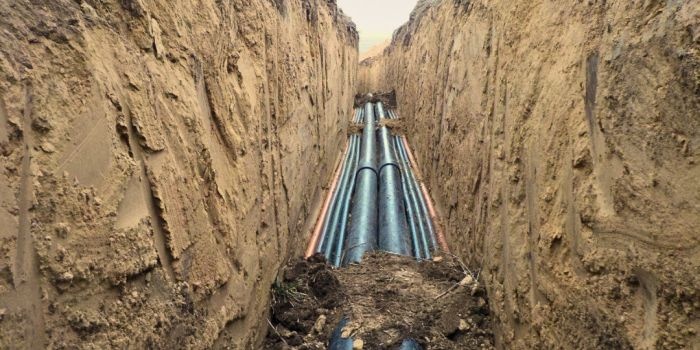
Zgodnie z Rozporządzeniem Ministra Cyfryzacji w sprawie warunków technicznych, jakim powinny odpowiadać kanały technologiczne i ich usytuowanie, które powstały na podstawie art. 7 ust. 2 pkt 2 ustawy Prawo...
Zgodnie z Rozporządzeniem Ministra Cyfryzacji w sprawie warunków technicznych, jakim powinny odpowiadać kanały technologiczne i ich usytuowanie, które powstały na podstawie art. 7 ust. 2 pkt 2 ustawy Prawo budowlane, kanały technologiczne stanowią ciąg osłonowych elementów obudowy, studni kablowych oraz innych obiektów lub urządzeń służących umieszczeniu lub eksploatacji.
Oprócz podejścia typowo ekonomicznego działania są często kreowane również przez odpowiednie uwarunkowania formalno-prawne.
Duża część nowych przepisów krajowych związanych z poprawą efektywności energetycznej wynika z zapisów dyrektyw europejskich.
Zachętą do podejmowania działań związanych z ograniczaniem strat ciepła przez stosowanie skuteczniejszych izolacji są również programy współfinansowania lub refinansowania części ponoszonych nakładów, np. programy NFOŚiGW, WFOŚiGW, fundusze termomodernizacyjne czy białe certyfikaty.
Głównymi beneficjentami mechanizmów pomocowych był i jest sektor budownictwa mieszkaniowego i użyteczności publicznej oraz wybrane grupy przedsiębiorstw [1, 2].
Wymagania w zakresie efektywności energetycznej
Do najważniejszych przepisów europejskich w zakresie efektywności energetycznej należą dyrektywy 2006/32/UE [3] i 2012/27/UE [4] [1].
Pierwsza z nich odnosiła się do celów strategicznych opłacalnej ekonomicznie poprawy efektywności końcowego wykorzystania energii przez określenie celów orientacyjnych oraz stworzenie mechanizmów, zachęt i ram instytucjonalnych, finansowych i prawnych, niezbędnych do usunięcia barier rynkowych i niedoskonałości rynku utrudniających efektywne końcowe wykorzystanie energii, a także stworzenie warunków do rozwoju i promowania rynku usług energetycznych.
Druga ustanawia wspólne ramy działań na rzecz promowania efektywności energetycznej w Unii Europejskiej dla osiągnięcia wzrostu efektywności energetycznej o 20% (zmniejszenia zużycia energii pierwotnej o 20%) do 2020 r. oraz utorowania drogi do dalszej poprawy efektywności energetycznej po tym terminie, a ponadto określa zasady opracowane w celu usunięcia barier na rynku energii oraz przezwyciężenia nieprawidłowości w funkcjonowaniu rynku. Przewiduje również ustanowienie krajowych celów w zakresie efektywności energetycznej na 2020 r.
Skutkiem wdrożenia dyrektywy powinien być 17% wzrost efektywności energetycznej do 2020 r., co stanowi wartość niższą niż 20% przewidziane w pakiecie klimatyczno-energetycznym 20/20/20. W zakresie nowych obiektów, na których budowę należy uzyskać decyzję pozwolenia na budowę, wymagania w zakresie efektywności energetycznej szczegółowo opisano w Rozporządzeniu Ministra Infrastruktury z dnia 12 kwietnia 2002 r. w sprawie warunków technicznych, jakim powinny odpowiadać budynki i usytuowanie [5]. Inne ważniejsze przepisy krajowe, które miały i mają wpływ na kształtowanie świadomości inwestorów w temacie efektywności, to Ustawa o wspieraniu przedsięwzięć termomodernizacyjnych[6] oraz Ustawa o efektywności energetycznej [7] z późniejszymi zmianami i nowelizacjami, a także wiele rozporządzeń szczegółowych stanowiących m.in. o zakresie i formie audytu energetycznego, metodologii wykonywania obliczeń, podstaw wykonywania weryfikacji obliczeń itp. Warto przywołać również Krajowy Plan Działań dotyczący efektywności energetycznej dla Polski z 2014 r., Obwieszczenie Ministra Gospodarki z dnia 21 grudnia 2012 r. w sprawie szczegółowego wykazu przedsięwzięć służących poprawie efektywności energetycznej [8] oraz Rozporządzenie Ministra Gospodarki z dnia 23 października 2012 r. w sprawie przetargu na wybór przedsięwzięć służących poprawie efektywności energetycznej [9]. Większość przywołanych aktów prawnych poświęcona jest zmniejszeniu zużycia energii dostarczanej do budynków mieszkalnych, budynków zbiorowego zamieszkania i budynków użyteczności publicznej na potrzeby ogrzewania, wentylacji, klimatyzacji oraz podgrzewania wody użytkowej, zmniejszeniu strat energii w lokalnych sieciach ciepłowniczych oraz zasilających je lokalnych źródłach ciepła, a także całkowitej lub częściowej zamianie konwencjonalnych źródeł energii na źródła niekonwencjonalne, w tym źródła odnawialne. |
ABSTRAKT |
W pierwszej części artykułu dotyczącego efektywności energetycznej instalacji przemysłowych przytoczono i omówiono akty prawne i inne dokumenty odniesienia dotyczące efektywności energetycznej. Wymieniono czynniki wpływające na skuteczność energetyczną instalacji termoizolacyjnych oraz sposoby określania tej skuteczności. Pokazano przykładowe wyniki i metody obliczeń strat ciepła układów przemysłowych.Increase of energy efficiency of industrial installations with improvement of insulation quality. Part 1 Legal requirements and performance evaluation methodsThe first part of the article concerning energy efficiency of industrial installations gives reference and discus-sion of legislation and other reference documents on energy efficiency. Factors affecting energy efficiency of thermal insulation installations are enumerated, together with methods of determining such efficiency. Example results and calculation methods of heat losses in industrial systems are presented as well. |
Zagadnienia efektywności energetycznej dokładniej opisano w Ustawie o efektywności energetycznej [7]. Omówiono w niej krajowy cel dotyczący oszczędnego gospodarowania energią, zadania jednostek sektora publicznego odnośnie efektywności energetycznej, zasady uzyskania i umorzenia świadectwa efektywności energetycznej, zasady sporządzania audytu efektywności energetycznej oraz uzyskania uprawnień audytora efektywności energetycznej.
Niestety, z zakresu obowiązywania ustawy wyłączono wiele przedsiębiorstw posiadających instalacje, które są objęte systemem handlu uprawnieniami do emisji w rozumieniu Ustawy z dnia 22 grudnia 2004 r. o handlu uprawnieniami do emisji do powietrza gazów cieplarnianych i innych substancji [10], z wyjątkiem urządzeń potrzeb własnych.
Ograniczenia wynikające z obecnej ustawy mają zostać zniesione w opracowywanej nowelizacji ustawy o efektywności energetycznej, która zakłada wydłużenie okresu jej obowiązywania do 2020 r. oraz zniesienie wyłączenia przedsiębiorstw objętych obowiązkiem handlu uprawnieniami do emisji gazów cieplarnianych oraz znaczne usprawnienie mechanizmu przyznawania białych certyfikatów.
Często zdarzało się bowiem, że przedsiębiorcy wypełniający wymagania ustawy mieli trudności w uzyskaniu potwierdzenia celowości (uzyskania białych certyfikatów), ponieważ mechanizm uzyskiwania tych certyfikatów nie zadziałał w pełni.
Wymagania wobec układów termoizolacyjnych
Skuteczność energetyczna instalacji termoizolacyjnych zależy od bardzo wielu czynników [11, 12]. Można je podzielić na dwie grupy:
- pierwsza - to czynniki, które brano pod uwagę podczas projektowania i wykonania izolacji,
- druga - to czynniki wynikające z warunków, w jakich izolacja jest użytkowana w obiekcie.
Najważniejszą grupę czynników stanowi grupa pierwsza. Należy w niej wymienić m.in.:
- prawidłowy dobór materiału izolacyjnego, uwzględniający temperaturę czynnika roboczego instalacji w różnych warunkach pracy oraz odporność na przyszłe narażenia mechaniczne, termochemiczne, klimatyczne, chemiczne lub wywołane promieniowaniem,
- optymalny dobór grubości izolacji, uwzględniający koszt wykonania izolacji i przyszły koszt zaoszczędzonej energii,
- dobór rodzaju i sposób wykonania podkonstrukcji,
- dobór rodzaju i sposób wykonania płaszcza ochronnego,
- sposób minimalizowania liniowych i punktowych mostków cieplnych.
W drugiej grupie można wymienić czynniki wynikające w dużej mierze z kultury technicznej służb odpowiedzialnych za eksploatację instalacji, w ramach której można wymienić m.in.:
- okresową kontrolę skuteczności izolacji,
- demontaż i ponowny montaż fragmentów izolacji z zachowaniem wymagań jak dla wykonywania nowej izolacji,
- okresową konserwację płaszcza ochronnego oraz niedopuszczanie do mechanicznego przerwania ciągłości powłok ochronnych.
Ważne jest również, aby nie dopuszczać do zmiany warunków pracy izolacji w stosunku do warunków przyjmowanych na etapie tworzenia założeń projektowych.
W zakresie wymagań formalnych, jakie muszą spełniać termoizolacje przemysłowe, można wymienić jedynie kilka przepisów.
Obowiązujący zapis dla projektowania izolacji termicznej instalacji przemysłowych zawarto w Rozporządzeniu Ministra Gospodarki z dnia 17 września 1999 r. w sprawie bezpieczeństwa i higieny pracy przy urządzeniach i instalacjach energetycznych [13]. Zgodnie z jego § 33:
"Urządzenia i instalacje pracujące z czynnikiem o temperaturze wyższej niż 60°C powinny być wyposażone w izolację termiczną tak zaprojekto-waną i utrzymaną, aby temperatura zewnętrzna na jej powierzchni w miejscach dostępnych nie przekraczała 60°C" [13].
W zakresie obowiązywania Ustawy prawo budowlane [14] oraz warunków technicznych, jakim powinny odpowiadać budynki i ich usytuowanie [5], należy projektować izolacje zgodnie normą PN-B-02421:2000 [15].
Zakres stosowania normy to izolacje cieplne w instalacjach centralnego ogrzewania, ciepłej wody użytkowej i technologicznej, sieciach ciepłowniczych prowadzonych w kanałach, tunelach i budynkach oraz sieciach napowietrznych o temp. czynnika nie większej niż 200°C.
Środowisko zrzeszone w Polskim Stowarzyszeniu Wykonawców Izolacji Przemysłowych przyczyniło się do opublikowania normy branżowej PN-B-20105:2014-09 [16], w której zawarto wiele cennych informacji dotyczących wymagań jakościowych i sposobu odbierania prac izolacyjnych oraz wprowadzono wymóg zachowania temperatury na zewnętrznym płaszczu izolacji nie więcej niż 50°C.
W normie można również znaleźć zalecenie, aby wyznaczać grubość izolacji na podstawie kryterium ekonomicznego.
Biorąc pod uwagę przytoczone informacje oraz fakt, że stosowanie w naszym kraju norm nie jest obowiązkowe, można sformułować wniosek o braku jednoznacznych zasad i wytycznych do projektowania izolacji termicznych na instalacjach przemysłowych. W praktyce przemysłowej skutkuje to tym, że inwestorzy, projektanci i wykonawcy wciąż określają wymagania w zakresie skuteczności izolacji termicznych przez wypełnienie jedynie obowiązku zapewnienia bezpiecznej temperatury na płaszczu ochronnym izolacji.
Ocena skuteczności układów termoizolacyjnych
Większość instalacji przemysłowych o temperaturze czynnika grzewczego powyżej 60°C jest wyposażona w układ termoizolacyjny. Skuteczność tych układów można określać obliczeniowo lub przez pomiar. Rzeczywista wartość strat ciepła zależy od bardzo wielu czynników [11, 12, 17].
W metodzie obliczeniowej przyjmuje się w uproszczeniu, że straty zależą od temperatury czynnika grzewczego i otoczenia, współczynników przejmowania ciepła po stronie czynnika grzewczego i środowiska zewnętrznego, uwzględniających charakter konwekcji, a także współczynników przewodzenia ciepła zastosowanych materiałów z uwzględnieniem niejednorodności warstw wywołanych konstrukcją wsporczą i sposobem montażu poszczególnych elementów układu.
Na wyznaczoną wartość strat ciepła ma wpływ również przyjęta metoda obliczeń, która może w różny sposób uwzględniać zjawisko przewodzenia, konwekcji i promieniowania ciepła, co w konsekwencji może prowadzić do pewnych różnic w szacowaniu strat.
Różnice te będą jeszcze większe, jeżeli przyjmie się do obliczeń niewłaściwe wartości parametrów opisujących zjawiska cieplno-przepływowe w badanym układzie lub właściwości fizyczne zastosowanych materiałów izolacyjnych.
Na RYS. 1 i RYS. 2 przedstawiono wyniki obliczeń strat ciepła rurociągu o średnicy nominalnej 200 mm, temp. czynnika 540°C w odniesieniu do trzech różnych temperatur powierzchni płaszcza ochronnego: 80°C, 60°C i 40°C.
Obliczenia wykonano przy założeniu izolacji z wełny szklanej i mineralnej. Założono także, że rurociąg ułożono w pozycji poziomej w pomieszczeniu hali przemysłowej. W hali panuje temp. 25°C, prędkość ruchu powietrza w strefie izolacji nie przekracza 0,5 m/s, a wilgotność względna powietrza wynosi 55%.
Straty podano w przeliczeniu na 1 m długości rurociągu (RYS. 1) oraz na 1 m2 powierzchni zewnętrznej izolacji (RYS. 2). Opis zastosowanej metodologii obliczeń przy podanych założeniach można znaleźć w normie niemieckiej VDI 4610 [18].

RYS. 1. Straty ciepła izolowanego rurociągu technologicznego o średnicy DN 200 i temp. czynnika roboczego 540°C przypadające na 1 m długości rurociągu (1)

RYS. 2. Straty ciepła izolowanego rurociągu technologicznego o średnicy DN 200 i temp. czynnika roboczego 540°C przypadające na 1 m² powierzchni zewnętrznej płaszcza izolacji (2)
Straty ciepła wyznaczone przy temp. płaszcza 60°C (czyli takiej, jaką przyjmuje się najczęściej przy doborze grubości izolacji termicznej w projektach technicznych) wynoszą prawie 590 W na metr długości rurociągu, a w przeliczeniu na m² powierzchni izolacji to ponad 300 W. Wartości te są znacznie większe niż te, które określa się dla grubości wyznaczonych według normy PN-B-02421:2000 [15].
Nierzadko w rzeczywistych układach przemysłowych wskutek procesu starzenia się izolacji zmierzona temperatura płaszcza sięga 80-100°C. Wówczas straty ciepła osiągają poziom 1 kW na długości 1 m rurociągu (FOT. 1 i FOT. 2).

FOT. 1. Wynik pomiaru termowizyjnego rurociągu poziomego o temperaturze czynnika technologicznego ok. 540°C wykonany w obiekcie przemysłowym (3)

FOT. 2. Wynik pomiaru termowizyjnego rurociągu pionowego o temperaturze czynnika technologicznego ok. 540°C wykonany w obiekcie przemysłowym (4)
W metodach pomiarowych bazuje się najczęściej na pomiarze temperatury ekwiwalentnej, która uwzględnia rozkład temperatury na płaszczu ochronnym izolacji oraz temperatury, prędkości i wilgotności powietrza otaczającego instalację. Następnie wyznacza się obliczeniowo strumień strat z uwzględnieniem matematycznego opisu zjawisk konwekcji i promieniowania.
W przypadku instalacji liniowych (rurociągi, kanały itp.) straty można szacować również przez pomiar spadku temperatury czynnika na badanym odcinku oraz strumienia masowego czynnika płynącego w instalacji. Ta ostatnia metoda może być najskuteczniejsza - pod warunkiem, że mierzony spadek temperatur będzie na tyle duży, aby zminimalizować błędy urządzeń pomiarowych.
Do najczęściej wykorzystywanych metod wyznaczania temperatury ekwiwalentnej na powierzchni ciał stosuje się metody oparte na obserwacji i zapisie rozkładu promieniowania podczerwonego wysyłanego przez badane ciało, którego temperatura jest wyższa od zera absolutnego, i przekształceniu tego promieniowania na światło widzialne: punktowe (pirometry) lub powierzchniowe (kamery termowizyjne).
Stosowanie w praktyce metod termowizyjnych wymaga odpowiedniej wiedzy i przygotowania, ponieważ tylko prawidłowo wykonany pomiar pozwala osiągnąć dokładność do ± 2% odczytu lub ± 2°C. W innym przypadku ocena zdjęć termowizyjnych może znacznie odbiegać od wartości rzeczywistych.
Poprawny pomiar temperatury wymaga uwzględnienia wielu parametrów [19]. Najważniejsze z nich to:
- korekcja transmisji atmosferycznej na podstawie wprowadzonej odległości, temperatury atmosfery i wilgotności względnej,
- korekcja transmisji optycznej na podstawie sygnałów z czujników pomiarowych,
- korekcja emisyjności przez poprawne wpisanie wartości współczynników emisyjności badanych powierzchni,
- korekcja odbić temperatury tła na podstawie wprowadzonej temperatury tła czy korekcja optyki na podstawie wprowadzonej transmisji optyki [19].

RYS. 4. Wizualizacja wpływu zjawisk mikroklimatycznych na rozkład temperatury na powierzchni zewnętrznej izolacji rurociągów technologicznych (6)
Poprawna ocena skuteczności izolacji termicznej instalacji przemysłowych wymaga uwzględnienia warunków środowiskowych panujących w obrębie badanych obiektów.
Obiekty przemysłowe to najczęściej przestrzenie wielkokubaturowe, w których panują w różnych okresach oraz różnych miejscach bardzo zróżnicowane warunki mikroklimatyczne.
Na RYS. 3. i RYS. 4. przedstawiono wyniki badań symulacyjnych obrazujących wpływ różnych warunków środowiskowych (jak prędkość i temperatura powietrza oraz charakter zjawiska konwekcji) na miejscowe rozkłady temperatury powierzchni płaszcza izolacji termicznej.
Wynika z nich m.in. iż ocena izolacji powinna być prowadzona odcinkami, a podział powinien przebiegać na granicy stref o podobnych warunkach mikroklimatycznych. Wyznaczenie takich stref wymaga jednak przeprowadzenia pomiarów i analizy zjawisk cieplno-przepływowych w badanym pomieszczeniu.
Podczas oceny skuteczności izolacji termicznych należy również zadbać, by wyraźnie określić granice bilansowe badanego obszaru. W globalnym bilansie strat ciepła należy bowiem uwzględnić bilanse miejscowe, których charakter może nie zawsze być negatywny.
Przykładem takim może być analiza strat ciepła w hali kotłów. Oprócz wyznaczenia strat ciepła od wszystkich obiektów energetycznych znajdujących się w pomieszczeniu należy również określić i uwzględnić bilans zysków ciepła wynikający z czerpania powietrza do procesu spalania spod sufitu hali.
Z przedstawionych przykładów wynika, że określanie skuteczności izolacji termicznej w warunkach przemysłowych wymaga od osób wykonujących takie analizy dużej wiedzy i przygotowania zawodowego.
Brak odpowiednich przepisów i norm jeszcze bardziej komplikuje proces analityczny, gdyż weryfikacja wyników może w dużej mierze wynikać z subiektywnej oceny osoby dokonującej weryfikacji.
Literatura
1. Z. Parczewski, "Efektywność energetyczna w wybranych krajach UE, USA oraz w Polsce (trendy zmian, mechanizmy i instrumenty polityki)", monografia Instytutu Energetyki - Instytut Badawczy, Warszawa 2014.
2. "Planowanie i zarządzanie w energetyce", pod red. P. Borowski, M. Powałka, Wydawnictwo SGGW, Warszawa 2009.
3. Dyrektywa 2006/32/UE Parlamentu Europejskiego i Rady z dnia 5 kwietnia 2006 r. w sprawie efektywności końcowego wykorzystania energii i usług energetycznych oraz uchylająca dyrektywę Rady 93/76/EWG (DzUrz L 114 z 27.4.2006, s. 64).
4. Dyrektywa 2012/27/UE Parlamentu Europejskiego i Rady z dnia 25 października 2012 r. w sprawie efektywności energetycznej, zmiany dyrektyw 2009/125/WE i 2010/30/UE oraz uchylenia dyrektyw 2004/8/WE i 2006/32/WE (DzUrz L 315 z 14.11.2012).
5. Rozporządzenie Ministra Infrastruktury z dnia 12 kwietnia 2002 r. w sprawie warunków technicznych, jakim powinny odpowiadać budynki i usytuowanie (DzU 2002r. nr 75, poz. 690 ze zm).
6. Ustawa z dnia 18 grudnia 1998 r. o wspieraniu przedsięwzięć termomodernizacyjnych (DzU 1998 nr 162 poz. 1121).
7. Ustawa z dnia 15 kwietnia 2011 r. o efektywności energetycznej (DzU 2011 nr 94 poz. 551).
8. Obwieszczenie Ministra Gospodarki z dnia 21 grudnia 2012 r. w sprawie szczegółowego wykazu przedsięwzięć służących poprawie efektywności energetycznej (M.P. 2013, poz. 15).
9. Rozporządzenie Ministra Gospodarki z dnia 23 października 2012 r. w sprawie przetargu na wybór przedsięwzięć służących poprawie efektywności energetycznej (DzU 2012 poz. 1227).
10. Ustawa z dnia 22 grudnia 2004 r. o handlu uprawnieniami do emisji do powietrza gazów cieplarnianych i innych substancji (DzU 2004 nr 281 poz. 2784).
11. J. Górzyński, "Przemysłowe izolacje cieplne", Sorus 1996.
12. A. Skorek, A. Szlęk, "Wpływ technologii izolacji rurociągu na koszt transportu ciepła", "Energetyka", nr 6/7/2007.
13. Rozporządzenie Ministra Gospodarki z dnia 17 września 1999 r. w sprawie bezpieczeństwa i higieny pracy przy urządzeniach i instalacjach energetycznych (DzU 1999 nr 80 poz. 912).
14. Ustawa z dnia 7 lipca 1994 - Prawo budowlane (DzU z 1994 r. nr 89, poz. 414 ze zm).
15. PN-B-02421:2000, "Izolacja cieplna przewodów, armatury i urządzeń. Wymagania i badania odbiorcze".
16. PN-B-20105:2014-09, "Izolacja cieplna wyposażenia budynków i instalacji przemysłowych. Wymagania dotyczące projektowania, wykonania i odbioru robót".
17. E. Kostowski, "Przepływ ciepła", Wydawnictwo Politechniki Śląskiej, Gliwice 2006.
18. VDI 4610 Blatt 1:2012-12, "Energieeffizienz betriebstechnischer Anlagen. Wärme- und Kälteschutz".
19. D. Auer, "Kieszonkowy przewodnik. Termografia", Testo Sp. z o.o., Warszawa 2009.