Izolacje we współczesnej prefabrykacji betonowej
Insulation in modern concrete prefabrication elements
![FOT. 1. Ułożenie folii tłoczonej na ścianach piwnic; fot.: [5]](https://www.izolacje.com.pl/media/cache/typical_view/data/202106/prefabrykacja-betonowa.jpg)
FOT. 1. Ułożenie folii tłoczonej na ścianach piwnic; fot.: [5]
Idea prefabrykacji w budownictwie sięga czasów rzymskich, kiedy to przy wykorzystaniu wapna, gipsu, wody, kamiennego kruszywa oraz popiołu wulkanicznego produkowano kompozyt przypominający dzisiejszy beton. Kolejnym krokiem w historii nawiązującym do prefabrykacji było wynalezienie współczesnego betonu z cementu portlandzkiego w 1824 r. i początki stosowania żelbetu do produkcji siatkobetonowych donic [1].
Zobacz także
Bostik Bostik AQUASTOPP – szybkie i efektywne rozwiązanie problemu wilgoci napierającej
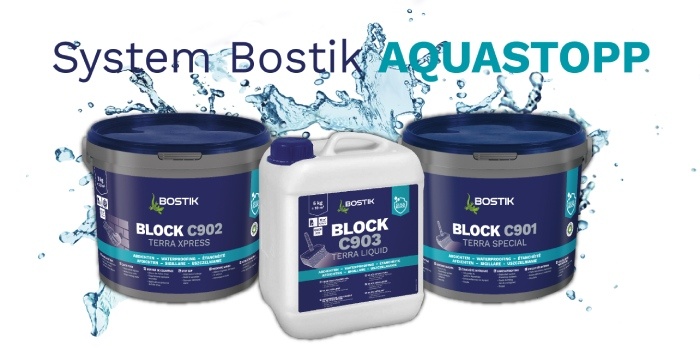
Bostik to firma z wieloletnią tradycją, sięgającą 1889 roku, oferująca szeroką gamę produktów chemii budowlanej dla profesjonalistów i majsterkowiczów. Producent słynie z innowacyjnych rozwiązań i wysokiej...
Bostik to firma z wieloletnią tradycją, sięgającą 1889 roku, oferująca szeroką gamę produktów chemii budowlanej dla profesjonalistów i majsterkowiczów. Producent słynie z innowacyjnych rozwiązań i wysokiej jakości preparatów, które znajdują zastosowanie w budownictwie, przemyśle i renowacji.
Fiberglass Fabrics s.c. Wiele zastosowań siatki z włókna szklanego

Siatka z włókna szklanego jest wykorzystywana w systemach ociepleniowych jako warstwa zbrojąca tynków zewnętrznych. Ma za zadanie zapobiec ich pękaniu oraz powstawaniu rys podczas użytkowania. Siatka z...
Siatka z włókna szklanego jest wykorzystywana w systemach ociepleniowych jako warstwa zbrojąca tynków zewnętrznych. Ma za zadanie zapobiec ich pękaniu oraz powstawaniu rys podczas użytkowania. Siatka z włókna szklanego pozwala na przedłużenie żywotności całego systemu ociepleniowego w danym budynku. W sklepie internetowym FFBudowlany.pl oferujemy szeroki wybór różnych gramatur oraz sposobów aplikacji tego produktu.
Parati Płyta fundamentowa i jej zalety – wszystko, co trzeba wiedzieć

Budowa domu jest zadaniem niezwykle trudnym, wymagającym od inwestora podjęcia wielu decyzji, bezpośrednio przekładających się na efekt. Dokłada on wszelkich starań, żeby budynek był w pełni funkcjonalny,...
Budowa domu jest zadaniem niezwykle trudnym, wymagającym od inwestora podjęcia wielu decyzji, bezpośrednio przekładających się na efekt. Dokłada on wszelkich starań, żeby budynek był w pełni funkcjonalny, wygodny oraz wytrzymały. A jak pokazuje praktyka, aby osiągnąć ten cel, należy rozpocząć od podstaw. Właśnie to zagwarantuje nam solidna płyta fundamentowa.
Kształtowanie sektora budowlanego wraz z rozwijającym i zmieniającym się przemysłem wraz z technologią zaczęło rozszerzać produkcję masową poprzez opracowywanie nowych materiałów i technologii budowlanych, zwłaszcza po okresie rewolucji przemysłowej. Pierwszym najważniejszym przykładem standaryzacji i masowej produkcji jest budynek Crystal Palace z 1850 r. w Londynie. W 1891 r. w budynku w Biarritz we Francji zastosowano prefabrykowane belki żelbetowe, a w 1900 r. w Ameryce po raz pierwszy użyto prefabrykowanych żelbetowych płyt dachowych.
Kolejne próby prefabrykacji zostały podjęte chociażby przez takiego architekta jak Le Corbusier, którego koncepcja budynku z prefabrykatów Domino z 1914 r. stanowiła przez lata inspirację dla przyszłych pokoleń projektantów. Pomimo dużego zainteresowania system ten został rozpowszechniony dopiero po drugiej wojnie światowej. Pierwsze oficjalne konstrukcje wykorzystujące technologię prefabrykacji powstały na początku lat 60. XX wieku.
W Polsce po okresie tzw. wielkiej płyty prefabrykacja betonowa zaczęła powracać do łask dopiero w latach 90. ubiegłego wieku, kiedy to dostrzeżono korzyści płynące z badanego systemu nie tylko w sektorze mieszkaniowym, ale także przemysłowym. Elementy i przegrody wykonane w prefabrykacji betonowej coraz częściej są także rozpatrywane w kontekście budownictwa pasywnego, a na rynku pojawiają się certyfikowane materiały stanowiące komponent domu pasywnego [1, 2].
O czym przeczytasz w artykule:
|
Wykorzystanie elementów prefabrykowanych betonowych jest praktyką stosunkowo młodą, ale powszechnie stosowaną w budownictwie mieszkaniowym. W wyniku prowadzonych badań i wzrastającego popytu inwestorów na tego typu rozwiązania, obecnie produkowane materiały zostały przystosowane przez producentów do najnowszych wymagań i stanowią realną alternatywę dla konstrukcji monolitycznych. W artykule przeanalizowano zastosowanie współczesnych izolacji przeciwwodnych i przeciwwilgociowych w ścianach piwnic z prefabrykatów betonowych, a następnie szczegółowo opisano izolowanie termiczne z płyt PIR ścian zespolonych wraz z przedstawieniem otrzymanych wyników w zakresie parametrów cieplnych przegrody.
Insulation in modern concrete prefabrication elementsThe use of precast concrete elements is a relatively recent practice, but it is commonly used in housing construction. As a result of the conducted research and the growing demand for this type of solutions among the investors, the materials currently produced have been adapted by the manufacturers to the latest requirements and may be a real alternative to monolithic structures. The article analyses the use of modern waterproofing and anti-damp insulation in cellar walls made of precast concrete elements. Then the author described in detail the thermal insulation of composite walls made of PIR panels, along with the presentation of the obtained results in the field of thermal parameters of the partition. |
Produkcja prefabrykatów betonowych
Beton prefabrykowany to beton, który jest produkowany w jednym miejscu, do wykorzystania w innym miejscu jako materiał mobilny. Największa część światowej produkcji prefabrykatów prowadzona jest w wyspecjalizowanych zakładach dostawców, jednak w niektórych przypadkach z przyczyn m.in. ekonomicznych, geograficznych, skali produktu lub z powodu utrudnionego dostępu, część elementów jest przygotowywana przy samym placu budowy.
Fabryka dostawcy komercyjnego zazwyczaj obejmuje obiekty do produkcji asortymentów o podobnym charakterze w zależności od specjalizacji firmy, elementów ramowych, okładziny, belek mostowych itp. W związku z tym sprzęt jest często wysoce zmechanizowany, uwzględniający szybkie dozowanie i dystrybucję betonu, a także posiadający instalację do przyspieszonego utwardzania produktu [1, 2].
Ściany typu filigran – produkcja i montaż
Jednym z coraz bardziej popularnych rozwiązań konstrukcyjnych są ściany zespolone składające się z dwóch płyt typu filigran, połączonych ze sobą kratownicami, które zapewniają stabilność układu w czasie transportu, montażu oraz układania betonu. Dzięki swojej budowie gwarantują odpowiednie powiązanie i współpracę w fazie budowy oraz eksploatacji pomiędzy elementami [3].
Płyty ścian montuje się na równym i oczyszczonym podłożu. Aby połączyć ścianę z płytą fundamentową, z podłoża betonowego powinny wystawać pręty zbrojenia startowego, tzw. wytyki. Żeby zniwelować poziom podłoża betonowego, stosuje się podkładki niwelacyjne wysokości 2–3 cm i w ten sposób uzyskuje się liniowość poziomą ściany.
Na jeden element prefabrykowanej ściany należy zastosować minimum 4 punkty podporowe i dopiero na tak przygotowanym podłożu można zacząć układanie ścian prefabrykowanych. Sam montaż wykonuje się za pomocą żurawia lub dźwigu samojezdnego, wyposażonego w trawersy.
Należy zwrócić uwagę, by ściany ułożyć na punktach podporowych w linii szkicu lub prowadnic. Po ustawieniu elementu prefabrykowanego w odpowiednim miejscu należy go zabezpieczyć podporami ukośnymi i skontrować jego ułożenie w pionie. Podpory należy umocować do tulei montażowych, mieszczących się w prefabrykacie, oraz do podłoża betonowego.
Uzyskany kąt pomiędzy podporą a ścianą powinien wynosić ok. 40–50°. Dopiero po zamocowaniu wszystkich podpór można odpiąć haki dźwigu i przystąpić do układania kolejnego elementu ściany. W kolejnych krokach, po ułożeniu ściany zespolonej, można przystąpić do układania zbrojenia styków ścian żelbetowych, a także zbrojenia dodatkowego [3].
Betonowanie przestrzeni pomiędzy płytami odbywa się po oczyszczeniu i zwilżeniu wewnętrznych powierzchni płyt. Mieszanka betonowa powinna mieć konsystencję dopasowaną do grubości rdzenia ściany i układu kratownic. Beton należy układać równomiernie, poziomymi warstwami.
Do wypełnienia prefabrykatu warto zastosować mieszankę betonową samozagęszczalną. Ważne jest, by w przypadku zastosowania prefabrykowanych ścian zespolonych w kondygnacjach podziemnych, piwnicznych, garażowych oraz tam, gdzie wymagana jest szczelność przeciwwilgociowa/przeciwwodna lub istnieje zjawisko wystąpienia wilgoci, penetracji wody, użyć materiałów hydroizolacyjnych.
Izolacja przeciwwodna i przeciwwilgociowa ścian piwnic z prefabrykatów
W zakresie izolacji przeciwwodnej zaniechało się już praktycznie stosowania pap smołowych, które przez swoją nietrwałość z biegiem czasu nie chroniły skutecznie przegrody przed wodą znajdującą się w gruncie. W konsekwencji dokonano udoskonalenia w postaci bitumu modyfikowanego (uszlachetnionego) plastomerem APP. Dzięki tym zabiegom polepszono odporność pap na starzenie się oraz obniżono temperaturę łamliwości papy.
Papy modyfikowane należy układać w temperaturze dodatniej, ponieważ łatwiej wtedy dochować poprawności wykonania, zapewniając jednocześnie suchą powierzchnię ściany. Niektórzy producenci oferują papy w postaci pasów samoprzylepnych, dzięki czemu unikamy konieczności użycia do montażu palnika.
Kolejną możliwością izolacji ścian piwnic jest zastosowanie folii tłoczonych wykonanych z polietylenu. Są one dosyć charakterystyczne ze względu na wytłoczenia wysokości sześciu lub ośmiu milimetrów, które tworzą powietrzną szczelinę wentylacyjną umożliwiającą osuszanie ścian. Co ważne, także pod względem parametrów termicznych przegrody w budynkach energooszczędnych, folia tłoczona poprawia jej właściwości termiczne [3, 4]. Folię tłoczoną, zwaną potocznie także kubełkową, układa się w poziomie, ponieważ szerokość folii jest dostosowana do wysokości ściany.
Kolejną opcją izolacji ścian piwnic są materiały bentonitowe, które dopiero w chwili kontaktu z wodą stają się materiałem izolacyjnym. Pod wpływem wody swobodnie pozostawiony bentonit może zwiększyć swoją objętość kilkunastokrotnie, tworząc żel, który nie dopuszcza do przenikania zarówno pary wodnej, jak i wody.
Kluczowe w tym zagadnieniu jest ograniczenie możliwości pęcznienia. Dzięki swoim właściwościom, w zastosowanej izolacji występuje możliwość samonaprawy uszkodzeń spowodowanych osiadaniem budowli lub skurczem betonu.
Przykładem gotowego produktu są membrany, które składają się z trzech warstw: folii polimerowej, z warstwy bentonitowej oraz z cienkiej błony osłonowej rozpuszczającej się pod wpływem wody. Folia polimerowa jest pierwszą warstwą ochronną i ogranicza pęcznienie bentonitu, który natomiast zapobiega przedostaniu się wody do warstwy izolowanej przegrody. Błona osłonowa chroni warstwę konstrukcyjną ściany przed bezpośrednim kontaktem z pęczniejącym bentonitem [6, 7].
Izolacja termiczna ścian zespolonych
Ściany zespolone typu filigran są także izolowane termicznie. Wykorzystywane są do tego płyty PIR montowane pomiędzy żelbetowymi płytami. Wybór ten nie jest przypadkowy, ponieważ płyty poliizocyjanuratowe PIR wyróżniają się bardzo korzystnymi cechami mechanicznymi i niskim współczynnikiem przewodzenia ciepła. Do ich produkcji używa się izocujanianu, poliolu oraz specjalnych aktywatorów i stabilizatorów. Charakteryzuje je wysoka ognioodporność, odporność na wilgoć, pleśń i bakterie, a także niewielki ciężar. Jest to bardzo korzystne rozwiązanie zastępujące styropian i wełnę, w momencie gdy jest ograniczona przestrzeń na izolację, a wymagane są wysokie parametry cieplne przegrody, ponieważ już dzisiaj współczynnik przewodzenia ciepła λ tego materiału wynosi 0,020–0,022 W/(m·K) [8, 9].
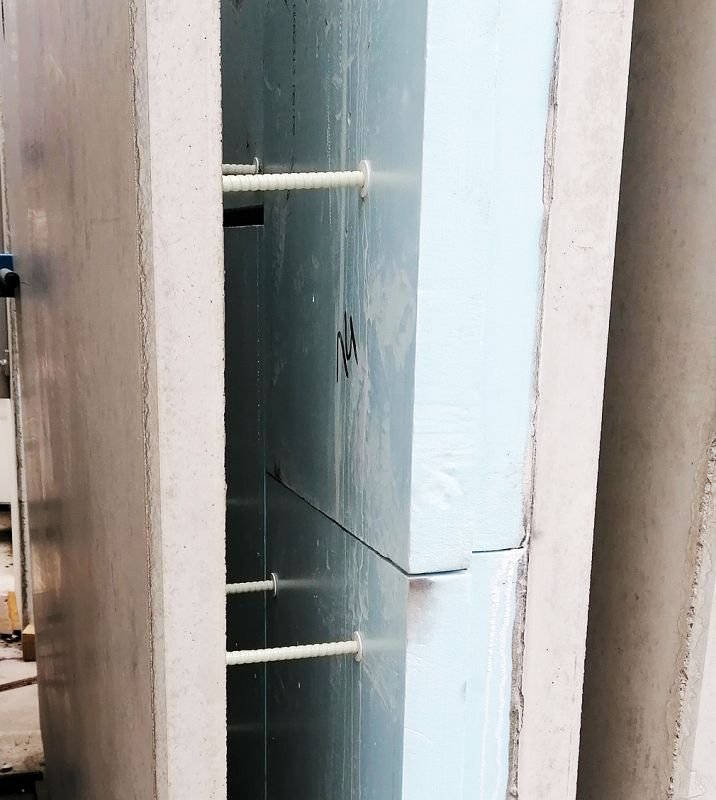
FOT. 3. Ściana filigran z widoczną izolacją z płyt PIR; fot.: B. Witkowski, K. Schabowicz, M. Moczko
Płyty izolacji termicznej są montowane za pomocą kotew wykonanych z tworzywa kompozytowego wzmacnianego włóknami. Cechą charakterystyczną tego materiału jest wysoka wytrzymałość na działanie substancji chemicznych i odporność na korozję. Przewagą kotew z włókna szklanego nad łącznikami ze stali nierdzewnej czy aluminium jest niewielka przewodność ciepła, a co za tym idzie – dzięki ich zastosowaniu unikamy powstaniu mostków cieplnych przy punktowych połączeniach.
Na RYS. 1–3 przedstawiono rozkład izoterm dla łączników z:
- włókna szklanego,
- stali nierdzewnej,
- aluminium.
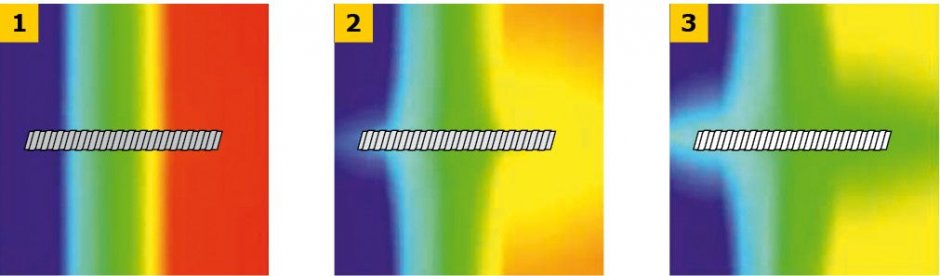
RYS. 1–3. Rozkład izoterm dla łączników z włókna szklanego (1), stali nierdzewnej (2) i aluminium (3); rys.: [10]
Wartość współczynnika przenikania ciepła UC ściany zespolonej typu filigran obliczona w kalkulatorze ABC wynosi 0,172 W/(m2·K) i przegroda ta spełnia najnowsze wymogi Warunków Technicznych obowiązujących od 2021 r. [0,20 W/(m2·K)]. Jednakże chcąc poprawić powyższe właściwości do standardu budynku pasywnego, dla którego współczynnik przenikania ciepła UC dla ściany zewnętrznej jest nie większy niż 0,15 W/(m2·K), należałoby zwiększyć grubość płyty PIR do min. 14 cm.
Podsumowanie
Prefabrykacja betonowa jest stosunkowo nowym i intensywnie badanym rozwiązaniem konstrukcyjnym, którego powszechne stosowanie w budownictwie mieszkaniowym zostało zapoczątkowane dopiero w latach 60. ubiegłego wieku.
Dzisiejsza produkcja elementów ma nie tylko zapewnić odpowiednio szybki czas dostawy i montażu, ale także zagwarantować najwyższą jakość w zakresie izolacji termicznej i przeciwwodnej. Przykład ścian zespolonych typu filigran spełnia wszystkie powyższe kryteria m.in. dzięki zastosowaniu najwyższej klasy izolacji w formie płyt PIR oraz kotew z włókna szklanego, które ograniczają powstanie mostków termicznych w miejscach łączeń z izolacją.
Powyższe rozwiązanie z powodzeniem może zostać wykorzystane w budynkach o najwyższej klasie energooszczędności, jednocześnie skracając czas budowy w porównaniu z konstrukcjami monolitycznymi oraz umożliwiając zmniejszenie grubości przegród poprzez zastosowanie izolacji termicznej o jednym z najniższych współczynników przewodzenia ciepła dla materiałów dostępnych na rynku.
Literatura
1. Strona internetowa www.inzynierbudownictwa.pl.
2. O.Y. Bayraktar, „Prefabricated Concrete and Waste Managment”, International Journal of Engineering Research & Technology, 2020.
3. Katalog Betard.
4. P. Sekki, T. Karvinen, J. Vinha, „Moisture behaviour of external insulated precast concreto wall panels”, Journal of Building Physics, 2020.
5. Strona internetowa www.kb.pl
6. Strona internetowa www.geotest.pl
7. Strona internetowa www.intako.pl
8. T. Makaveckas, R. Bliudzius, „The influence of polyisocyanurate (PIR) facing on the heat transfer through the corners of insulated building partitions”. E3S Web of Conferences 172, NSB 2020.
9. Strona internetowa www.e-izolacje.pl
10. Katalog Schöck Isolink.