Zarządzanie ryzykiem w branży budowlanej
Cz. 2. Wymogi i skala projektów renowacji zbiorników betonowych na przykładzie infrastruktury wodno-ściekowej
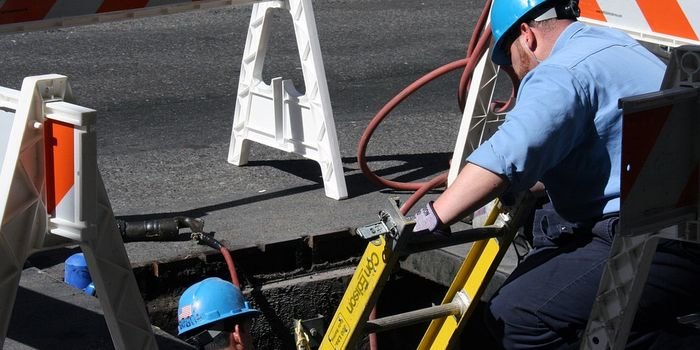
Jak zarządzać ryzykiem w branży budowlanej? fot. www.pixabay.com
Podczas realizacji projektów renowacji zbiorników w oczyszczalniach ścieków występuje bardzo dużo różnych czynników, których wpływ wywołuje określone skutki dla trzech kolejnych parametrów efektywności inwestycji. Tymi parametrami są koszty projektu, czas realizacji inwestycji i jakość wykonanych prac, która determinuje trwałość przeprowadzonej renowacji.
Zobacz także
Messe Monachium GmbH Światowe Targi Architektury, Materiałów i Systemów Budowlanych BAU zapraszają do Monachium
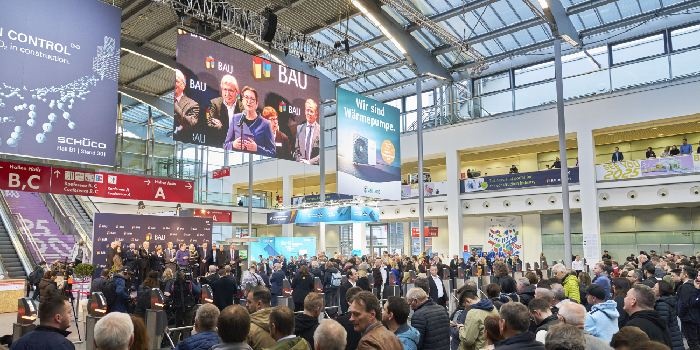
W styczniu 2025 r. czeka nas kolejna odsłona targów BAU, czyli Światowych Targów Architektury, Materiałów i Systemów Budowlanych. Największa światowa wystawa budownictwa odbędzie się w dniach 13–17 stycznia...
W styczniu 2025 r. czeka nas kolejna odsłona targów BAU, czyli Światowych Targów Architektury, Materiałów i Systemów Budowlanych. Największa światowa wystawa budownictwa odbędzie się w dniach 13–17 stycznia 2025 w Monachium. Ponad 2000 wystawców w 18 halach czeka na Państwa.
Rockwool Polska Profesjonalne elementy konstrukcyjne BIM dla budownictwa
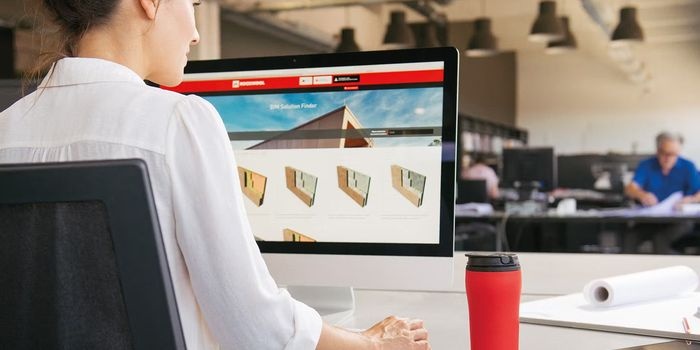
W nowoczesnym projektowaniu budynków standardem staje się technologia BIM (Building Information Modeling). Jest to złożony system informacji technicznej, który na podstawie trójwymiarowego modelu obiektu...
W nowoczesnym projektowaniu budynków standardem staje się technologia BIM (Building Information Modeling). Jest to złożony system informacji technicznej, który na podstawie trójwymiarowego modelu obiektu opisuje cechy zastosowanych rozwiązań.
dr inż. Krzysztof Pawłowski prof. PBŚ Charakterystyka energetyczna budynku i jego części – analiza planowanych zmian w przepisach prawnych od 1 stycznia 2026 r.

Charakterystyka energetyczna budynku i części budynku (Świadectwo charakterystyki energetycznej) to dokument, który określa wielkość zapotrzebowania na energię niezbędną do zaspokojenia potrzeb energetycznych...
Charakterystyka energetyczna budynku i części budynku (Świadectwo charakterystyki energetycznej) to dokument, który określa wielkość zapotrzebowania na energię niezbędną do zaspokojenia potrzeb energetycznych związanych z użytkowaniem budynku lub części budynku. W pierwszych dniach lipca 2024 r. na stronie internetowej Ministerstwa Rozwoju i Technologii [1] zaprezentowano projekt zmian w rozporządzeniu.
Jeżeli założymy, że każdego roku jest remontowanych kilka tysięcy zbiorników i że średniej wielkości zbiornik w oczyszczalni ścieków komunalnych ma 1000 m2 powierzchni do zabezpieczenia powłoką ochronną, a koszt wykonania renowacji takiej powłoki wraz z usunięciem starej, oczyszczeniem i osuszeniem podłoża, rusztowaniami itd. wynosi od 200 do nawet 500 zł/1 m2, to widzimy, że zagadnienie dotyczy olbrzymich nakładów finansowych.
Jeżeli więc stosowanie zasad zarządzania ryzykiem przy realizacji tych projektów może wygenerować kilkanaście lub nawet kilkadziesiąt procent oszczędności, to bez wątpienia warto je stosować.
Pod względem czasu trwania prac renowacyjnych zbiorników betonowych jako elementów infrastruktury gospodarki wodno-ściekowej należy wyróżnić różne przypadki.
Dla zakładów wodociągowych, które w swoich zasobach mają większą liczbę określonego rodzaju zbiorników w ramach jednej instalacji, łatwiej jest zaplanować funkcjonowanie zakładu podczas wyłączenia z użytkowania jednego z tych zbiorników na czas jego renowacji, z zachowaniem ciągłości odbioru i oczyszczania ścieków lub dostarczania wody pitnej do gospodarstw domowych w obrębie rejonu danej gminy czy powiatu.
W takich przypadkach czas trwania remontu nie jest tak bardzo istotny jak w gminach, gdzie instalacja składa się z pojedynczych zbiorników i wyłączenie jednego rodzaju zbiornika ze schematu oczyszczania ścieków lub produkcji wody pitnej uniemożliwia realizację działań statutowych.
W takich sytuacjach wydłużenie czasu trwania prac renowacyjnych jest zagadnieniem krytycznym i jeżeli można określić metody zarządzania ryzykiem minimalizujące prawdopodobieństwo opóźnienia przywrócenia remontowanego zbiornika do użytkowania, to bezwzględnie należy traktować te budowle jako strategiczne z punktu widzenia bezpieczeństwa publicznego i wprowadzić takie metody do praktyk powszechnie stosowanych.
Jakość realizacji projektu renowacji powłok ochronnych w zbiornikach będących częścią infrastruktury gospodarki wodno-ściekowej bezpośrednio wpływa na jej trwałość, a więc długość czasu prawidłowego i bezpiecznego użytkowania bez zakłóceń do czasu, gdy konieczne stanie się przeprowadzenie kolejnej renowacji. Oczekuje się, że okres ten wyniesie od 5 do 10 lat. Jednak gdy uzyskana jakość nowo wykonanej powłoki ochronnej jest niższa od zakładanej, interwał czasu pomiędzy kolejnymi renowacjami drastycznie się skraca. W długoterminowej perspektywie, np. w okresie 30 lat, oznacza to zwiększenie ilości przeprowadzania renowacji nawet dwukrotnie.
Takie sytuacje nie tylko nadmiernie obciążają budżet gminy czy powiatu, implikując nadmierne koszty utrzymania, ale dodatkowo istotnie zwiększają ryzyko utraty zachowania ciągłości realizowania zadań statutowych, narażając okoliczną ludność na przerwy w dostawie wody pitnej czy odbioru ścieków. Wobec tego należy zrobić wszystko, co tylko możliwe, aby ograniczyć ryzyko związane z zaistnieniem takiej sytuacji.
Wykonywanie i renowacja powłok ochronnych na wewnętrznych powierzchniach zbiorników betonowych
Zastosowanie powłok ochronnych na powierzchniach betonowych zbiorników na ciecze dzieli się na dwa rodzaje:
- Pierwszym jest zastosowanie ich w zbiornikach wody czystej (pitnej), gdzie zadaniem powłoki jest ochrona jakości wody przed wypłukiwaniem i migracją do niej zanieczyszczeń z betonu. Zwłaszcza w przypadkach miękkiej wody o niskim pH, która rozpuszcza i wypłukuje wapno z betonu.
- Drugim natomiast jest zastosowanie powłok w zbiornikach wody zanieczyszczonej lub przemysłowej i w tym przypadku zadaniem powłoki jest ochrona konstrukcji betonowej przed jej destrukcją w wyniku agresywnego odziaływania samej wody i substancji chemicznych rozcieńczonych w wodzie. Zbiorniki oczyszczalni ścieków to zdecydowanie ten drugi przypadek.
Beton jest sztucznym kamieniem i jak każdy wytworzony przez człowieka materiał podlega degradacji związanej z oddziaływaniem niekorzystnych czynników środowiska oraz z czynnikami reologicznymi powiązanymi ze zmianami cech fizycznych betonu wraz z upływem czasu.
Czynnikami oddziałującymi niekorzystnie na beton są m.in. absorbowana i wydalana woda oraz gazy, oleje i tłuszcze roślinne oraz zwierzęce, związki chemiczne itp.
Występuje wiele mechanizmów destrukcji betonu, w których bezpośrednim czynnikiem są dodatkowe okoliczności, jednak bez udziału wody mechanizmy te są uśpione, więc udział wody w tych reakcjach jest katalityczny i niejako decydujący w wielu procesach rozpadu betonu.
Do typowych procesów degradujących beton zaliczamy m.in. [1]:
- karbonatyzację
- korozję alkaliczną,
- korozję siarczanową,
- korozję mikrobiologiczną,
- korozję mrozową,
- korozję chlorkową,
- oddziaływanie chemikaliami.
W zasadzie woda w kontakcie z betonem katalizuje niezależnie trzy różne rodzaje mechanizmów niszczących jego strukturę:
- reakcje chemiczne wody z substancjami zawartymi w betonie,
- mechanizmy uszkodzeń fizycznych.
- funkcję rozpuszczalnika i medium do migracji agresywnych związków chemicznych ze środowiska w głąb struktury betonu.
Woda jako katalizator reakcji chemicznych
Woda inicjuje pewnego rodzaju procesy korozyjne, w których biorą czynny udział substancje zawarte w samym betonie, ale bez wody są nieszkodliwe, i dopiero pod wpływem jej udziału dochodzi do tych reakcji. Do tego typu procesów korozyjnych możemy zaliczyć karbonatyzację, podczas której (w wielkim skrócie) dochodzi do powstawania nierozpuszczalnych kryształów węglanu wapnia w procesie wiązania wodorotlenku wapnia przez dwutlenek węgla, co wpływa na znaczne obniżenie się pH betonu w strefie otuliny prętów zbrojeniowych, umożliwiając zablokowany wcześniej proces utleniania się stali zbrojeniowej. W efekcie tego procesu najpierw tworzą się drobne pęknięcia, a następnie otulina zbrojenia zaczyna odpadać, odsłaniając pręty (FOT. 1).
Karbonatyzacja jest wysoce zależna od wilgotności względnej betonu, a w szczególności jej proces przebiega szybko, gdy wilgotność względna utrzymuje się na poziomie między 50 a 75%. Przy wilgotności betonu poniżej 25% karbonatyzacja przebiega w sposób bardzo powolny.
Korozja wywołana karbonatyzacją występuje często na powierzchniach narażonych na stały dostęp wilgoci, jak oddziaływanie opadów deszczu, przepływ wody itp.
Drugim typem korozji betonu przy udziale wody jest korozja alkaliczna. Reakcja alkaliczno-krzemionkowa może powodować ekspansję i pękanie betonu, co prowadzi do poważnych uszkodzeń konstrukcji. Reakcja alkaliczno-krzemionkowa zachodzi między alkaliami z cementu a reaktywnym kruszywem w warunkach odpowiedniej wilgotności. Produktem reakcji alkaliczno-krzemionkowej jest pęczniejący żel, który zwiększając swoją objętość na skutek „dobrej współpracy” z wodą, implikuje naprężenia w stwardniałym betonie. Pęcznienie żelu na powierzchni kruszywa powoduje powstanie naprężeń rozciągających i ściskających w otulinie betonowej. Wynikiem tych oddziaływań jest siatka spękań konstrukcji, wzmożona penetracja wilgoci i odpadanie otuliny (FOT. 2). Zapobieganie zawilgoceniom, co ma miejsce w przypadku stosowania powłok ochronnych, zahamowuje zjawisko korozji alkalicznej.
Kolejnym mechanizmem niszczącym strukturę konstrukcji betonowych pod wpływem zawilgocenia bądź też wnikania w jego strukturę czystej wody, jest korozja mrozowa, czyli rozsadzania struktury betonu w wyniku rozszerzania się gromadzącej się w porach wody w procesie zamarzania.
W zimnych klimatach zniszczenia chodników, ścian oporowych, pomostów, tarasów związane są z cyklami zamarzania i odmarzania i są jedną z głównych przyczyn prac konserwacyjnych i naprawczych. Cząsteczki wody są bardzo małe, dlatego są zdolne do penetracji porów i kapilar betonu nawet najlepszej jakości.
Jeżeli woda dostanie się w strukturę betonu, do jego systemu kapilarnego i zamarznie, zwiększy swoją objętość (o ok. 9%), wywierając ogromne ciśnienie. Proces ten będzie się powtarzał, ponieważ zamarzanie i rozmarzanie pojawiające się cyklicznie prowadzi do rozszerzenia kapilar w strukturze. W betonie pojawia się coraz więcej wody i w konsekwencji więcej uszkodzeń. Zniszczenia powodowane zamarzaniem i odmarzaniem to najczęściej pękanie, czyli wykruszanie się betonu.
Woda jako medium migracji agresywnych substancji
Kolejnym mechanizmem działania wody w procesach korozyjnych betonu jest jej funkcja jako rozpuszczalnika umożliwiającego transport i wnikanie agresywnych substancji, jak kwasy, chlorki i siarczany w głąb struktury betonu.
Pierwszym przykładem takiego rodzaju mechanizmu jest korozja siarczanowa. Jest to najgroźniejsza w skutkach korozja, ponieważ w tym przypadku niszczenie betonu jest gwałtowne. Korozję tę wywołują roztwory wodne zawierające siarczany. W wyniku reakcji jonów siarczanowych ze składnikami betonu powstają trudno rozpuszczalne związki chemiczne, krystalizujące po przyłączeniu wody, zwiększając swoją objętość, często wielokrotnie.
Korozja siarczanowa powoduje ekspansję, spękania, łuszczenia, przez co prowadzi do obniżenia wytrzymałości na ściskanie.
Spośród wszystkich jonów jony chlorkowe najszybciej wnikają w głąb matrycy cementowej, z tego względu tzw. korozja chlorkowa betonu poddanego działaniu roztworu wody i chlorków postępuje z dużą szybkością. W wyniku reakcji jonów chlorkowych i wodorotlenku wapnia powstaje zasadowy i zwiększający swoją objętość podczas krystalizacji chlorek wapnia, który powoduje rozsadzanie struktury betonu.
Agresja chlorkowa prowadzi do obniżenia pH betonu oraz powstawania ekspansywnych związków, które mogą powodować spękanie i rozsadzanie struktury betonu.
Korozja kwasowa wywołana kwasami rozpuszczonymi w wodzie polega na rozpuszczaniu się wodorotlenku wapnia w stwardniałym zaczynie cementowym w betonie i w dalszej kolejności rozkładzie uwodnionych krzemianów i glinianów, w rezultacie czego dochodzi do rozpadu mikrostruktury betonu.
Aktualny stan wiedzy na temat wymogów i skuteczności dostępnych technologii ochrony powłokowej betonu zbiorników
W zakresie wymogów do projektowania i praktycznej skuteczności rozwiązań zgodnych z tymi wytycznymi obserwujemy niestety duże rozbieżności, które wynikają z błędnych założeń i braku aktualizacji danych o zmieniających się w czasie warunkach ekspozycji środowiskowej w tym sektorze budownictwa (TABELA 1).
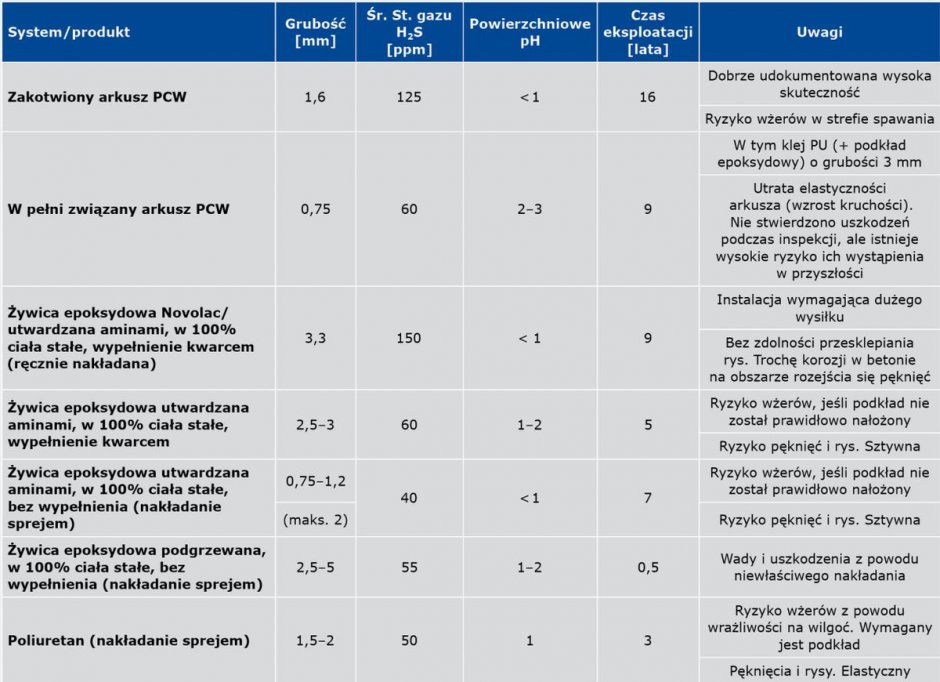
TABELA 1. Ocena skuteczności znanych technologii ochrony powłokowej; oprac. J. Banera na podstawie [5]
W zakresie wytycznych do projektowania zbiorników dla oczyszczalni ścieków, ogólnie przyjmuje się, że ścieki bytowo-gospodarcze nie wykazują wysokiej agresywności w stosunku do betonu.
Zgodnie z normą PN EN 206-1 środowisko panujące w kanalizacji ściekowej powinno być klasyfikowane jako XA1. Zarówno wskaźniki pH, które w ściekach bytowo-gospodarczych wahają się w przedziale od 5,5 do 6,5, jak i zawartość szkodliwych soli (siarczanów, chlorków i azotanów) nie przekracza zwykle 0,05%, co uznaje się za poziom poniżej wartości, które mogą być agresywne w stosunku do betonu. Jednocześnie literatura dotycząca tego zagadnienia podaje, że neutralnym odczynem pH betonu jest 12, a procesy korozyjne rozpoczynają się w środowisku poniżej 9,5 pH. Inne dane z lat 90. ubiegłego wieku wykazały, że podczas przebiegu procesu oczyszczania ścieków powstaje bardzo kwaśne środowisko już na poziomie pH 3, a nawet 2.
Dodatkowo ustalono, że średni poziom stężenia siarkowodoru w środowisku ściekowym w skali Europy wynosi 10 ppm. Ogólnie mówiąc, dane w tym zakresie są niespójne.
Opisany powyżej stan faktyczny odpowiadający stanowi wiedzy w tym zakresie w latach 90. ubiegłego stulecia odzwierciedlał wytyczne w zakresie wymagań stosowania odpowiednich w tamtych czasach normowych zabezpieczeń powłokowych konstrukcji betonowych [2] w obrębie infrastruktury gospodarki wodno-ściekowej w Europie celem przedłużenia ich trwałości i bezpiecznego okresu użytkowania. Jednak ze względu na znaczne rozbieżności w publikowanych materiałach na temat wytycznych projektowych dla gospodarki ściekowej i realnych wymagań, jeszcze w latach 90. zostały przeprowadzone szeroko zakrojone badania odporności różnych typów technologii zabezpieczeń powierzchniowych betonu w sektorze gospodarki wodno-ściekowej, gdzie dla celów wstępnej oceny przydatności tych materiałów wykorzystano badania laboratoryjne z zasymulowaniem środowiska podobnego pod względem agresji chemicznej do środowiska ścieków, a wnioski z przeprowadzonych badań zostały przedstawione w ciekawej publikacji z 1994 r. [3].
Analiza badań laboratoryjnych przedstawiona w tej publikacji wykazała, że na badanych 71 różnych materiałów, test ten przeszło pomyślnie tylko 21. Choć wszystkie ujęte w badaniu materiały w opisie zakresu zastosowania były przeznaczone właśnie do oczyszczalni ścieków. Co ciekawe, powłoki polimocznikowe [4] zaliczyły ten trudny test. A takie materiały jak winyloester, którego odporność chemiczna zdaje się przewyższać odporność polimoczników, nie zdały egzaminu w tych warunkach.
Skuteczność dostępnych na rynku technologii ochrony powłokowej badał również Robert Nixon [5], przeprowadzając serię testów powszechnie stosowanych powłok ochronnych.
Podczas tych testów nie była jednak badana bezkrytycznie tylko odporność chemiczna materiałów, ale również wpływ oddziaływania agresji chemicznej na inne parametry techniczne poddawanych działaniu obciążenia chemicznego jak sprężystość1) i zdolność przesklepiania rys czy siła przyczepności do podłoża betonowego.
Badanie odporności chemicznej podczas tej analizy uwzględniało oprócz kwasu siarkowego różne kwasy organiczne, w tym także kwasy tłuszczowe, jakie również występują w ściekach. Konkluzje analizy wyników tych badań mówią, że warunki środowiskowe w ściekach powodują utratę elastyczności różnych materiałów, co podobnie jak zastosowanie sztywnych materiałów powoduje powstawanie w powłoce rys i pęknięć umożliwiających przenikanie substancjom korozyjnym pod powłokę i degradację konstrukcji betonowej w tych miejscach.
W środowisku ściekowym oprócz odporności chemicznej na standardowe kwasy organiczne należy brać pod uwagę dodatkowe biogenne reakcje chemiczne, które są trudne do zasymulowania w warunkach laboratoryjnych.
Optymalną metodologię badań laboratoryjnych z uwzględnieniem tego czynnika stosowano podczas testów przeprowadzanych na Uniwersytecie w Duisburgu w Instytucie Fraunhofer do badania korozji biogennej. Metoda badania opracowana przez ten instytut pozwala zasymulować warunki przyśpieszonej korozji przy udziale biogennego kwasu siarkowego. Na bazie doświadczeń Instytutu Fraunhofer w zakresie tego testu wiemy, że przyspiesza on tempo korozji o 8 do 10 razy w porównaniu z realnymi warunkami, jakie panują w środowisku ściekowym, co oznacza, że 6 miesięcy trwania testu odpowiada okresowi 5–6 lat w naturalnym środowisku ściekowym.
Główne wnioski z powyższych analiz są następujące:
- Beton nie jest odporny na istniejące warunki środowiskowe w gospodarce wodno-ściekowej.
- Cementowo-polimerowe zaprawy naprawcze (nawet te siarczano odporne) w długim okresie czasu również nie są wystarczająco odporne.
- Nawet wysoka odporność chemiczna materiału powłokowego nie oznacza automatycznie wystarczającej odporności na biogenne reakcje chemiczne, które charakteryzują się wysoką agresywnością i działaniem żrącym.
- Odporność różnych materiałów na kwasy organiczne jest zwykle bardzo ograniczona w czasie trwania obciążenia.
- Nawet dobra lub bardzo dobra odporność chemiczna bez elastyczności i zdolności przesklepiania rys powłoki ochronnej to za mało. Materiał nawet najbardziej odporny chemicznie, lecz zbyt twardy, stanowi sztywną powłokę, która pękając [6] pod wpływem skurczu, prowadzi do korozji betonu, który miała chronić.
- Wszystkie błędy w aplikacji skutkujące nałożeniem niewystarczająco grubej warstwy powłoki nie zabezpieczą betonu przed korozją.
Cechy materiałów nowej generacji
Oprócz właściwości użytkowych materiałów już po ich związaniu bardzo ważne są również ich właściwości dotyczące wymaganych warunków otoczenia podczas aplikacji. Musimy pamiętać, że prace związane z wykonywaniem powłok ochronnych w obiektach sektora gospodarki wodno-ściekowej są z reguły prowadzone w bardzo trudnych warunkach. W zamkniętych pomieszczeniach, które do czasu rozpoczęcia remontu były zanurzone w wodzie (wypełnione ściekami), a więc konstrukcje te są zazwyczaj mokre, a w powietrzu panuje wysoka wilgotność, zazwyczaj przekraczająca maksymalną dopuszczalną dla prawidłowego wiązania materiałów standardowych z żywic reaktywnych2).
Czas na wykonanie prac jest ograniczony, a używane materiały wymagają dobrej przyczepności do podłoża, które jest mokre i zanieczyszczone. To są bardzo ważne zagadnienia, ponieważ przy zastosowaniu tradycyjnych materiałów wymagane jest zapewnienie suchego i czystego podłoża, a uzyskanie takich warunków w tak trudnym środowisku jest czasochłonne i kosztowne.
Przy rozpatrywaniu zalecanych kryteriów przy wyborze odpowiedniej technologii powłok ochronnych należy zwracać uwagę zarówno na właściwości użytkowe materiałów, jak i właściwości robocze podczas aplikacji.
Robert Nixon na podstawie analizy wyników przeprowadzonych badań [5] określił zestaw istotnych właściwości materiałów, jakie muszą posiadać materiały powłokowe, aby całościowo sprostać tym złożonym i trudnym warunkom. Podzielił te właściwości na dwie grupy. Pierwsza dotyczy właściwości użytkowych materiałów, czyli parametrów technicznych gotowej powłoki wykonanej z danego materiału:
- podwyższona długoterminowa (Klasa III) odporność na kwas H2SO4,
- długotrwała odporność na kwasy organiczne,
- niska nasiąkliwość (kapilarna absorbcja wody),
- odporność na biogenne reakcje chemiczne,
- optymalna przyczepność do podłoża betonowego,
- przyczepność do podłoża metalowego, ponieważ w niemal każdym zbiorniku betonowym w oczyszczalniach ścieków występują elementy stalowe jako wsporniki lub mocowania do montażu urządzeń technologicznych, które również wymagają zabezpieczenia,
- zdolność mostkowania rys (zarówno statycznych, jak i dynamicznych),
- wysoka odporność mechaniczna (ścieranie i uderzenia).
Natomiast do drugiej grupy przypisał właściwości materiałów jeszcze w postaci ciekłej jako cechy robocze podczas aplikacji przed ich stwardnieniem:
- tolerancja na wilgoć podłoża przy nakładaniu i utwardzaniu,
- łatwość uzyskania ciągłej warstwy powłoki pozbawionej porów i perforacji,
- krótki czas utwardzania, czas do nakładania kolejnej warstwy i czas do uzyskania odporności na obciążenia użytkowe,
- możliwość nakładania produktu na powierzchniach pionowych i poziomych ponad głową bez zacieków.
Odporność chemiczna
Pod względem chemicznym stosunkowo łatwo jest wytworzyć materiał o wysokiej odporności chemicznej, ponieważ za odporność chemiczną materiału odpowiada bezpośrednio gęstość sieciowania struktury molekularnej materiału, co można dość łatwo regulować, a im większa jest ta gęstość, tym wyższa jest odporność chemiczna [4]. Jednak gęstość sieciowania wiązań chemicznych reguluje również elastyczność materiału i im większa jest ta gęstość, tym materiał staje się sztywniejszy, a jak wspomniano już wcześniej, materiał do skutecznych zabezpieczeń powłokowych obok wysokiej odporności chemicznej musi być jednocześnie elastyczny i zdolny do przesklepiania. Niestety stworzenie materiału, który łączyłby te dwie cechy, jest nie lada wyzwaniem (RYS 1 i RYS. 2).
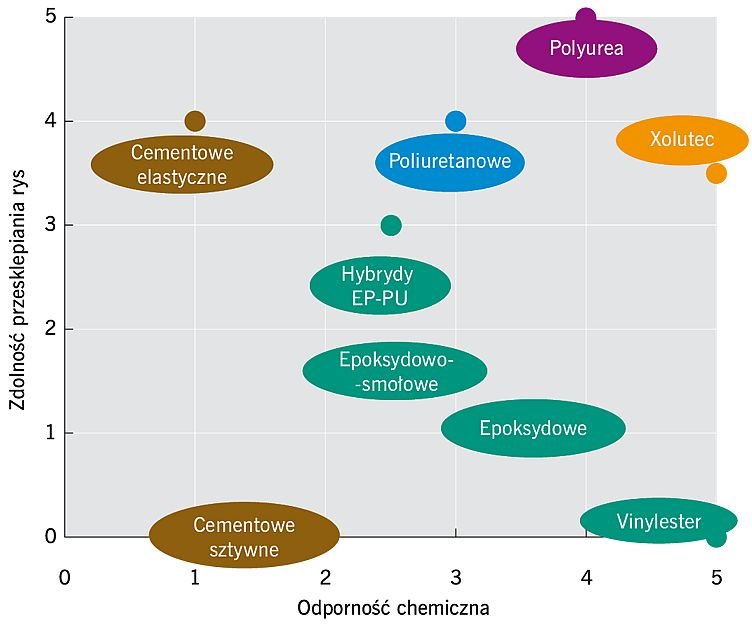
RYS. 1. Wykres parametrów odporności chemicznej i sprężystości różnych technologii powłok ochronnych; rys.: oprac. J. Banera na podstawie [9]
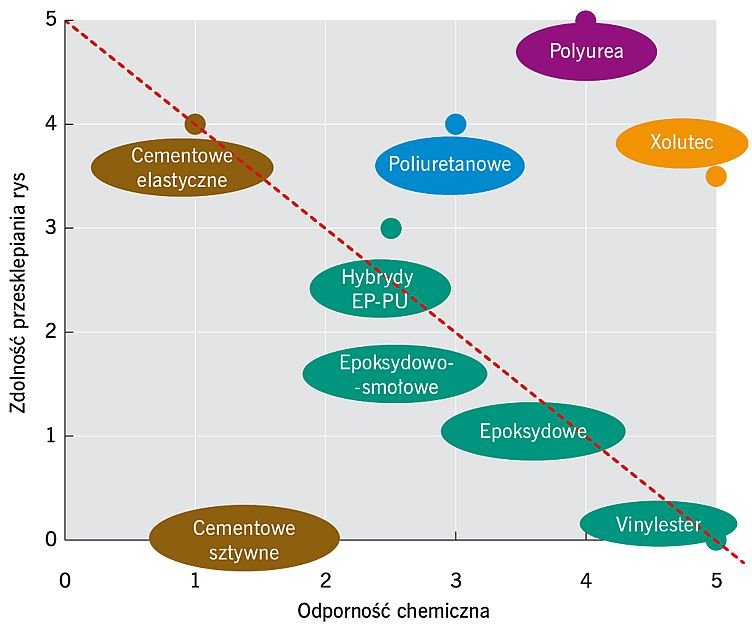
RYS. 2. Wykres pokazujący korelację odporności chemicznej i sprężystości/elastyczności różnych technologii do ochrony powłokowej; rys.: oprac. J. Banera na podstawie [9]
Metodologia badania odporności chemicznej nie jest skomplikowana. Jest ona ściśle określona przez normę [7] opisującą trzy standardy oznaczone klasami od I do III:
- klasa I to odporność na działanie substancji chemicznej na powierzchnię materiału bez dodatkowego ciśnienia przez okres 3 dni,
- klasa II to odporność na działanie substancji chemicznej na powierzchnię materiału również bez dodatkowego ciśnienia przez okres 28 dni,
- klasa III to odporność na działanie substancji chemicznej na powierzchnię materiału z dodatkowym ciśnieniem przez okres 28 dni.
Następnie jest badana utrata twardości Bucholza lub Shore’a badanego materiału i jeżeli nie zmniejsza się ona więcej niż o 50%, materiał ten jest uznawany za odporny na daną substancję.
Metodologia badania zdolności przesklepiania rys jest również określona przez normy, tym razem przez normę PN-EN 1062-7 [8], która rozgranicza dwa typy zdolności przesklepiania rys:
- statycznej, inaczej mówiąc zdolność przesklepiania rys z obciążeń statycznych, która jest określana klasami Aχ, gdzie χ określa zakres szerokości rozwarcia rysy w podłożu, którą badana powłoka jest w stanie przesklepić bez pęknięcia (TABELA 2),
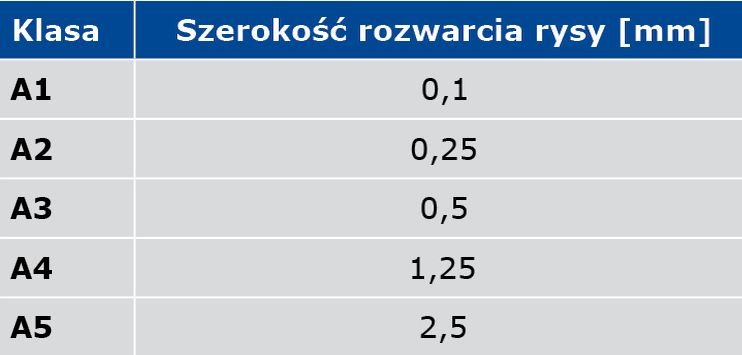
TABELA 2. Klasy zdolności przesklepiania rys z obciążeń statycznych; oprac. J. Banera na podstawie normy [8]
- dynamicznej (przy cyklicznym rozszerzaniu się rys i ich ponownym zwężaniu z wielokrotnym powtarzaniem się tego zjawiska). W tym przypadku jest ona określana klasami Bχ, gdzie prócz szerokości rozwarcia rysy w podłożu jest uwzględniana ilość cykli naprzemiennego rozszerzania i zwężania rysy oraz częstotliwość powtarzania tych cykli (TABELA 3).
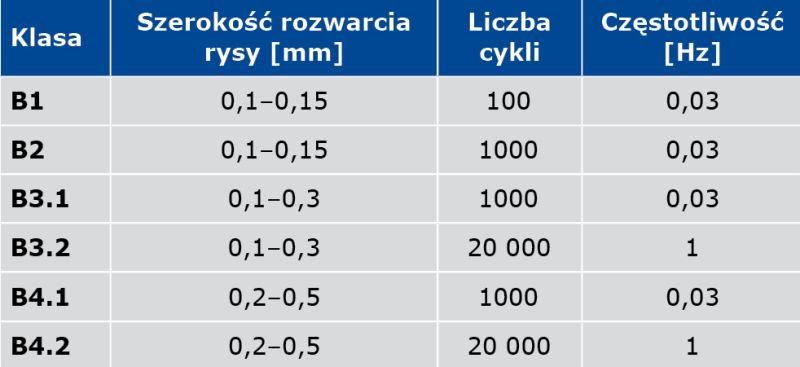
TABELA 3. Klasy zdolności przesklepiania rys z obciążeń dynamicznych; oprac. J. Banera na podstawie normy [8]
Wielokryterialna ocena dostępnych technologii
Jak wykazano powyżej, nie powinno się oceniać jakości materiałów do ochrony powłokowej przez pryzmat jednej jego cechy. Pomimo że wytyczne do projektowania ograniczają się do odporności chemicznej materiałów, to podczas oceny ich przydatności powinno się uwzględniać dodatkowo takie cechy, jak elastyczność i tolerancję dla wilgoci w podłożu podczas nakładania.
Jeżeli zbierzemy wszystkie dostępne typy (bazy chemiczne) technologii ochrony powłokowej na jednym wykresie, w którym uwzględnimy zarówno odporność chemiczną, jak i zdolność przesklepiania rys, zauważymy, że wzrost elastyczności (zdolności z przesklepiania rys) na ogół zmniejsza odporność chemiczną tych materiałów i zależność ta przebiega przez wykres niemalże (poza kilkoma wyjątkami) po linii prostej.
Jeżeli podzielimy te materiały na elastyczne i sztywne, jak również na bardziej i mniej odporne chemicznie, to tych jednocześnie elastycznych i odpornych chemicznie zostanie nam zaledwie kilka. Jeżeli jednak dołożymy kolejne kryterium w postaci normowej [10] tolerancji na wilgotne podłoże podczas aplikacji do wykresu korelacji odporności chemicznej i zdolności przesklepiania rys w podłożu, to zostanie nam tylko jedna technologia spełniająca te wszystkie wymagania jednocześnie.
Wysoka tolerancja na wilgoć podłoża podczas aplikacji nie tylko skraca czas potrzebny na przeprowadzenie prac, skracając czas suszenia zbiornika, ale również zmniejsza ryzyko delaminacji3), pęcherzenia [11] i pękania powłoki w okresie późniejszego użytkowania, które jest bardzo wysokie przy stosowaniu w skrajnych warunkach wilgotnościowych standardowych materiałów, które takiej cechy nie posiadają.
Wnioski
W świetle przedstawionych informacji nasuwa się wniosek, iż w celu zapewnienia realnej trwałości [12] planowanych prac renowacyjnych obiektów infrastruktury w zakresie gospodarki wodno-ściekowej należy w procesie doboru stosowanej technologii, oprócz podstawowych wytycznych do projektowania, uwzględniać wielokryterialny system wyboru materiałów, dobierając technologie nowej generacji, których receptury na etapie formulacji uwzględniały podwyższone wymagania ich odporności zgodnie z aktualnym stanem wiedzy na temat ekspozycji środowiskowej w tym sektorze budownictwa.
Ryzyko związane z wyborem materiałów niespełniających proponowanych przez Roberta Nixona [5] właściwości zagraża między innymi wydłużeniem czasu realizacji prac i wzrostu kosztów, gdy ze względu na wrażliwość materiału na wilgoć w podłożu konieczne staje się długie suszenie zawilgoconej konstrukcji betonowego zbiornika przed nakładaniem powłok. Ta właściwość wiąże się jednocześnie z ryzykiem opóźnienia terminu zakończenia prac renowacyjnych otwartego zbiornika w sytuacji wystąpienia niekorzystnych warunków atmosferycznych, ponieważ na ten czas należy wstrzymać prace lub zabezpieczyć miejsce prowadzenia prac przed wpływem tych warunków atmosferycznych. Zlekceważenie tego zagadnienia grozi delaminacją nowych powłok i koniecznością ponownej renowacji.
Gdy stosowane materiały nie mają odpowiednio wysokiej odporności chemicznej lub/i elastyczności, grozi to obniżeniem jakości i właściwości użytkowych (trwałości), co również wiąże się z ryzykiem kosztowym, gdyż może się okazać konieczne powtórzenie renowacji w bardzo krótkim czasie po zakończeniu bieżących prac i oddaniu zbiornika do użytkowania.
Zastosowanie materiałów wymagających długiego czasu na pełne związanie i uzyskanie końcowej wytrzymałości stanowi ryzyko opóźnienia przekazania zbiornika do użytkowania, a niedopełnienie tego warunku i napełnienie ściekami zbiornika zbyt szybko zagraża uszkodzeniu nowo wykonanych i nie w pełni utwardzonych/wytrzymałych powłok.
Wobec powyższego, wyszukiwanie w internecie nazw technologii/produktów przeznaczonych do ochrony powłokowej w oczyszczalniach ścieków przez projektantów, celem wpisania ich w specyfikacji technicznej konkretnego projektu (choć w zdecydowanej większości przypadków ten proces projektowania tak właśnie wygląda) może okazać się błędem, pomimo użycia produktu zgodnie z jego przeznaczeniem. Niestety w tym przypadku nie można zakładać, że skoro dany produkt jest przeznaczony do stosowania w oczyszczalniach ścieków, to spełnia on niezbędne dla tego środowiska wymagania, bez sprawdzenia jego właściwości zgodnie z listą kontrolną.
Artykuł powstał z potrzeby skonstruowania modelu programu zarządzania ryzykiem podczas renowacji zbiorników będących częścią instalacji gospodarki wodno-ściekowej zgodnie ze znanymi zasadami zarządzania ryzykiem stosowanymi w branży budowlanej.
Podczas pisania niniejszej pracy wykorzystano informacje z literatury fachowej w zakresie zarządzania ryzykiem oraz wiele analiz instytutów badawczych, norm i literatury dotyczącej naprawy i ochrony betonu. Wykorzystane zostały również materiały empiryczne pozyskane z zasobów wewnętrznych firm BASF i Master Builders Solutions, wnioski z przeprowadzonych wywiadów i materiały wewnętrzne firm specjalizujących się w opisywanych zagadnieniach w ramach szkoleń i warsztatów praktycznych, informacje pozyskiwane z materiałów prezentowanych w ramach konferencji branżowych, literaturze branżowej i z własnego doświadczenia praktycznego.
Literatura
1. J. Banera, „Ochrona konstrukcji betonowych narażonych na oddziaływanie czynników chemicznych”, WPPK 2018 „Innowacyjne i współczesne rozwiązania w budownictwie – konstrukcje żelbetowe”, t. IV.
2. PN-EN 1504‑2:2006, „Wyroby i systemy do ochrony i napraw konstrukcji betonowych. Definicje, wymagania, sterowanie jakością i ocena zgodności. Część 2: Systemy ochrony powierzchniowej betonu”.
3. J.A. Redner, R.P. His, E.J. Esfandi, „Evaluating coatings for concrete in wastewater facilities: An update”, JPCL, grudzień 1994.
4. J. Banera, M. Maj, A. Ubysz, „Powłoki polimocznikowe w budownictwie”, DTP:D-CONCEPT, Grupa MD, Poznań 2017.
5. R. Nixon, „Linings in wastewater plants: Real world performance evaluation”, JPCL, październik 2008.
6. PN-EN ISO 4628-4:2005, „Farby i lakiery. Ocena zniszczenia powłok. Określanie ilości i rozmiaru uszkodzeń oraz intensywności jednolitych zmian w wyglądzie. Część 4: Ocena stopnia spękania”.
7. PN-EN 13529:2005, „Wyroby i systemy do ochrony i napraw konstrukcji betonowych. Metody badań. Odporność na silną agresję chemiczną”.
8. PN-EN 1062-7:2005, „Farby i lakiery. Wyroby lakierowe i systemy powłokowe stosowane na zewnątrz na mury i beton. Część 7: Oznaczanie właściwości pokrywania rys”.
9. A. Berenguel, E. Casas Bolivar, „360° concrete protection for extreme conditions in waste water and chemical industry”, Webinar European Waterproofing Community 2018.
10. PN-EN 13578:2008, „Wyroby i systemy do ochrony i napraw konstrukcji. Metody badań. Kompatybilność z betonem wilgotnym”.
11. PN-EN ISO 4628-2:2005, „Farby i lakiery. Ocena zniszczenia powłok. Określanie ilości i rozmiaru uszkodzeń oraz intensywności jednolitych zmian w wyglądzie. Część 2: Ocena stopnia spęcherzenia”.
12. „Trwałość materiałów stosowanych do napraw i ochrony betonu”, redakcja zbiorowa: M. Kamiński, J. Jasiczak, W. Buczkowski, T. Błaszczyński, Dolnośląskie Wydawnictwo Edukacyjne, Wrocław 2009.
1) Pojęcie sprężystości jest ścisłe w stosunku do materiałów konstrukcyjnych i jest najczęściej rozumiane jako odkształcenie wiązań międzyatomowych. Siła oddziałuje na wiązania elektrostatyczne między atomami, powodując wzrost energii potencjalnej, a po odjęciu siły atomy te wracają do pierwotnego stanu równowagi. W przypadku materiałów uznawanych jako tzw. sprężyste, jak na przykład stal, odkształcenia te wynoszą do kilku dziesiątych procenta. W przypadku elastomerów natura tych odkształceń jest jednak odmienna. Odkształcenia wynikają z rozprostowywania zwartych łańcuchów makrocząsteczek. To prostowanie się łańcuchów nie jest związane ze wzajemnym przemieszczaniem się atomów, nie następuje więc wydłużenie wiązań między nimi. Wydłużanie materiału, spowodowane na przykład działaniem siły, prowadzi do zmniejszania się entropii. Towarzyszy temu między innymi efekt wydzielania ciepła. 2) Substancje o konsystencji płynnej, wytworzone na drodze polimeryzacji, polikondensacji lub poliaddycji, będące mieszaninami prepolimerów zawierających reaktywne grupy funkcyjne, które umożliwiają dalsze prowadzenie polireakcji bądź sieciowania skutkującego zmianą stanu skupienia w ciało stałe. 3) Odspajanie się powłoki od podłoża. |