Rozwój technologii materiałów hydroizolacyjnych
Development of technology of waterproofing materials
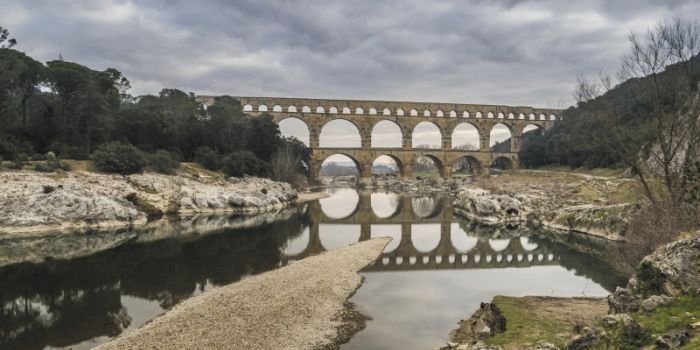
Akwedukt Pont du Gard, fot. Wikimedia Commons
Technologia uszczelniania budowli przy zastosowaniu materiałów uszczelniających produkowanych przemysłowo jest stosunkowo młoda [1]. Jednakże destrukcyjny wpływ wody na budynki i budowle znany jest od najbardziej zamierzchłych czasów – od zarania dziejów ludzkość poszukiwała sposobów zabezpieczania wznoszonych przez siebie obiektów nie tylko przed powodziami czy opadami atmosferycznymi, ale również „niewidzialną niszczycielską siłą generowaną przez wodę gruntową” [2].
Zobacz także
dr inż. Bartłomiej Monczyński Co leży u podstaw niezawodności hydroizolacji budynków?

W przypadku prawidłowo zaprojektowanego i wzniesionego budynku wpływ wody zawartej w gruncie nie powinien być w ogóle uwzględniany przy rozważaniu cieplno-wilgotnościowego stanu przegród budowlanych –...
W przypadku prawidłowo zaprojektowanego i wzniesionego budynku wpływ wody zawartej w gruncie nie powinien być w ogóle uwzględniany przy rozważaniu cieplno-wilgotnościowego stanu przegród budowlanych – przy odpowiednio dobranych i w pełni funkcjonalnych hydroizolacjach strefy przyziemia woda gruntowa nie może zawilgacać konstrukcji, a zatem nie wywiera żadnego negatywnego wpływu na budynek [1].
KOESTER Polska Sp. z o.o. Köster – specjaliści od hydroizolacji

KÖSTER BAUCHEMIE AG specjalizuje się w produkcji i dystrybucji materiałów do hydroizolacji i ochrony budowli oraz systemów uszczelnień, a ich produkty chronią budowle na całym świecie. Zarówno podczas...
KÖSTER BAUCHEMIE AG specjalizuje się w produkcji i dystrybucji materiałów do hydroizolacji i ochrony budowli oraz systemów uszczelnień, a ich produkty chronią budowle na całym świecie. Zarówno podczas renowacji budynków historycznych, jak i w trakcie budowy nowych obiektów – proponuje skuteczne rozwiązanie każdego problemu związanego ze szkodliwym oddziaływaniem wody i wilgoci.
Czytaj całość »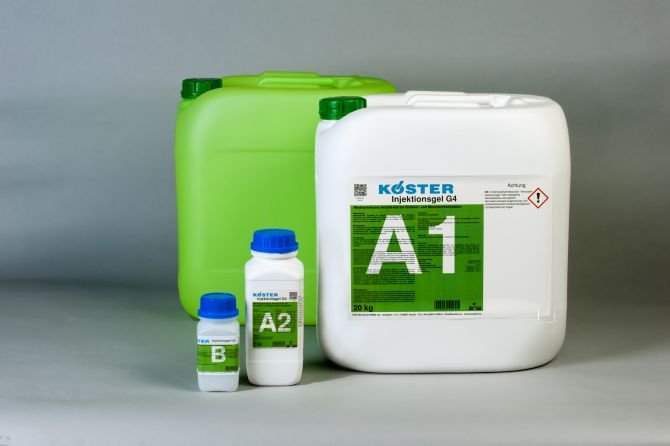
KOESTER Polska Iniekcja uszczelniająca żelem akrylowym KÖSTER Injektion Gel G4 żelbetowej płyty fundamentowej podziemnej hali pieca do wytopu szkła
W ramach prowadzonych prac modernizacyjnych i okresowej wymiany pieca do wytopu szkła podjęto decyzję o usunięciu powstałych podczas dotychczasowej eksploatacji nieszczelności płyty fundamentowej. Płyta...
W ramach prowadzonych prac modernizacyjnych i okresowej wymiany pieca do wytopu szkła podjęto decyzję o usunięciu powstałych podczas dotychczasowej eksploatacji nieszczelności płyty fundamentowej. Płyta o wymiarach w świetle ścian 35,50x36,27 m i grubości 1,60 m wykazywała liczne i okresowo intensywne przecieki, które powodowały konieczność tymczasowego odprowadzania przenikających wód gruntowych systemem rowków powierzchniowych wyciętych w płycie do studzienek zbiorczych i odpompowywania. Powierzchnia...
Czytaj całość »*****
Artykuł dotyczy historii rozwoju materiałów hydroizolacyjnych. Autor opisuje ich właściwości i zastosowanie.
Development of technology of waterproofing materials
The article concerns the history of the development of waterproofing materials.The author describes their properties and application.
*****
Pierwsze techniki uszczelniania wykorzystywały głównie produkty naturalne. Oprócz środków zapobiegawczych, takich jak zabezpieczenie przed wilgocią z gruntu poprzez posadowienie budynków na palach lub duże okapy dachów jako zabezpieczenie przed wodą z opadów atmosferycznych, do ochrony budynków stosowano glinę lub różnorakie powłoki ochronne (którym pokrywano ściany), np. gips zmieszany z olejem lnianym, tlenkiem ołowiu i woskiem [ 3 ].
Czytaj też: Odwadnianie budynków za pomocą drenażu opaskowego
Prawdopodobnie najstarszy zapis dotyczący zastosowania hydroizolacji zawarty jest w Biblii. Według Księgi Rodzaju materiały uszczelniające po raz pierwszy użyte zostały przy budowie Arki Noego [ 4 ]:
„Ty zaś zbuduj sobie arkę z drzewa żywicznego, uczyń w arce przegrody i powlecz ją smołą wewnątrz i zewnątrz.” (Rdz. 6, 14).
Natomiast pierwsza wzmianka dotycząca zastosowania smoły jako materiału budowlanego pojawia się przy opisie wieży Babel [4]:
„ I mówili jeden do drugiego: «Chodźcie, wyrabiajmy cegłę i wypalmy ją w ogniu». A gdy już mieli cegłę zamiast kamieni i smołę zamiast zaprawy murarskiej, rzekli: «Chodźcie, zbudujemy sobie miasto i wieżę, której wierzchołek będzie sięgał nieba, i w ten sposób uczynimy sobie znak, abyśmy się nie rozproszyli po całej ziemi»”. (Rdz. 11, 3–4).
Kwestią wymagającą wyjaśnienia jest pochodzenie smoły jako materiału uszczelniającego. Przypuszczalnie w zapisie biblijnym smoła oznacza produkt składający się z asfaltu naturalnego z mniej lub bardziej mocnymi domieszkami substancji mineralnych [ 1 ].
Asfalty naturalne występują zazwyczaj w pobliżu źródeł ropy naftowej i pod względem chemicznym są zbliżone zarówno do ropy naftowej, jak i asfaltów otrzymywanych z ropy naftowej. Na Środkowym Wschodzie, w Syrii, występują złoża asfaltu naturalnego o zawartości czystego asfaltu sięgającej 99% [ 5 ]. Na obszarze tym ropa może – ze względu na budowę geologiczną – wydostawać się na powierzchnię ziemi ( RYS. 1 ), gdzie pod wpływem promieniowania słonecznego odparowują jej lotne składniki, w wyniku czego powstaje asfalt naturalny.
Asfalt syryjski – nazywany również smołą żydowską – jest jednym z najdłużej znanych gatunków asfaltu. Pochodzi on z Morza Martwego i był opisywany przez takich starożytnych pisarzy jak Strabo, Diodorus czy Siculus [ 6 ]:
„…gdy asfalt rozpoczyna się wydostawać z dna morza na jego powierzchnię, to wzdyma się ono w fale i unoszą się z niego dymy i kłęby pary siarkowej, w której złoto, srebro i miedź traci swą barwę…”
Z drugiej strony można sobie wyobrazić, że biblijna „smoła” została wydobyta z naturalnych skał bitumicznych. Wiadomo również, że ropę naftową poddawano obróbce termicznej w tzw. piecach asfaltowych [ 1 ].
Najstarszą znaną budowlą uszczelnioną materiałem bitumicznym jest zbudowana 4,5 tys. lat temu łaźnia publiczna w miejscowości Mohendżo-Daro (jest to współczesna nazwa oznaczająca Kopiec Umarłych) – osadzie protomiejskiej w pobliżu brzegu Indusu na terenie dzisiejszego Pakistanu. Wielka Łaźnia był to położony w obrębie cytadeli miejskiej kompleks wielu komnat oraz ośmiu łazienek usytuowanych wokół basenu o wymiarach 12×7×2,5 m ( FOT. 1 ). Ściany basenu wykonane zostały z dwóch warstw muru rozdzielonych spoiną uszczelnioną bitumem [1, 7].
Technologie hydroizolacyjne stosowane były również przez starożytnych Egipcjan. Grecki historyk Herodot w piątym stuleciu przed naszą erą donosił o zastosowaniu asfaltów, jak również najstarszych tzw. zapraw szczelnych [ 2, 3 ]. Były to zaprawy zawierające popiół, czyli gliniano-popiołowe, a później również wapienno-popiołowe, a ich odporność na działanie wody wynikała z hydrofobowych właściwości niedopalonego popiołu, zawierającego sole alkaliczne oraz cząsteczki węgla drzewnego [ 2 ].
Również starożytni Rzymianie stosowali zaprawę wodoodporną ( opus caementicium ), której używali głównie do obiektów służących do magazynowania lub transportu wody, takich jak łaźnie, zbiorniki na wodę, wodociągi, a także w budownictwie portowym [ 1, 3 ]. Termin opus caementicium składa się ze słów opus (= dzieło, składnik, metoda budowy) oraz caementicium (= kamień ciosany, kamień łupany, kruszywo), które z biegiem czasu przekształciło się w stosowane obecnie słowo cement [ 1 ].
W swoim dziele „O architekturze ksiąg dziesięć” [8] Witruwiusz, architekt armii Cezara, wymienił następujące instrukcje dotyczące receptury produkcji w dużej mierze wodoodpornej zaprawy murarskiej:
„Po zgaszeniu wapna należy w ten sposób sporządzić zaprawę, żeby przy piasku kopalnym zawierała trzy czwarte piasku, a jedną czwartą wapna, jeśli zaś jest piasek rzeczny lub morski, dwie części piasku, a jedną część wapna. Wtedy bowiem słuszna będzie proporcja mieszaniny. Również jeśli dorzucić do rzecznego lub morskiego piasku jedną trzecią część tłuczonej i przesianej cegły, otrzyma się zdatniejszą do użytku zaprawę. (…) Mury zaś, które mamy zakładać w wodzie, należy tak budować. Trzeba sprowadzić piasek z obszarów ciągnących się od Kumę do przylądka Minerwy i wymieszać z wapnem tak, aby otrzymać zaprawę o stosunku dwa do jednego”.
Zastosowanie naturalnej puzzolany (pyłu pochodzenia wulkanicznego, którego najsłynniejsze złoża odkryto w Pozzuoli niedaleko Neapolu – stąd nazwa) pozwalało nie tylko uzyskać odporność na przenikanie wody, ale – jak wykazały ostatnie badania [ 9, 10 ] – zapobiegało rozprzestrzenianiu się uszkodzeń (włączenie klastów wapiennych umożliwiło betonowi samonaprawę pęknięć).
Najbardziej znanym z przykładów zastosowania opus caementicium są prawdopodobnie rzymskie cysterny i akwedukty (łac. aquae ductus, „ciąg wodny”), które doprowadzały wodę ze źródeł do rzymskich osiedli i były częściowo przenoszone na mostach. RYS. 2 oraz FOT. 2 przedstawiają przekroje rzymskiego akweduktu Eifel, wzniesionego w I i II wieku n.e., a zarazem jednego z najdłuższych akweduktów Cesarstwa Rzymskiego, który prowadził od Eifel – pasma górskiego w południowo-zachodniej części dzisiejszych Niemczech – do Colonia Claudia Ara Agrippinensium (dzisiejszej Kolonii).
Zgodnie z zaleceniem Witruwiusza kanały wodociągowe układano z przeważnie stałym spadkiem od 0,5 do 1%. Jeśli kanały musiały być prowadzone przez doliny, wykonywano je na mostach. Jednym z najbardziej znanych akweduktów jest ukończony w Prowansji przez Marka Agryppę w 19 r. p.n.e. Pont du Gard, prowadzący wodę ze źródeł w Uzès do Nimes w dzisiejszej Francji. Jego długość wynosiła ok. 50 km, a całkowity spadek 17 m. Zachowany do dziś (wpisany na listę światowego dziedzictwa UNESCO) w dolinie rzeki Gard odcinek ( FOT. na górze ) rozciąga się na długości 269 m i ma ok. 50 m wysokości. Trzy łuki ułożone jeden na drugim składają się z kamiennych bloków połączonych bez zaprawy, natomiast ułożony najwyżej akwedukt wykonano z opus caementicium [ 1 ].
Akwedukt Pont du Gard jest też przykładem innego rozwiązania hydroizolacyjnego stosowanego przez starożytnych Rzymian. Rozwiązanie to polegało na zastosowaniu impregnatów termoplastycznych w postaci naturalnych cerezyn i ozokerytu. Woski naftowe aplikowano, nagrzewając kamienne powierzchnie spalanymi polanami drewna, a po uzyskaniu wymaganej temperatury w podłoże wcierano ozokerytowe „buły”. Uzyskiwane w ten sposób zabezpieczenie chroniło materiał przed przenikaniem wody. Dzięki powierzchniowemu nagrzewaniu wosk penetrował w porowate kamienie tylko do głębokości kilkunastu milimetrów, a mimo to zabezpieczenia były niezwykłe trwałe [ 11 ].
Mniej więcej do połowy XIX w. środki hydroizolacyjne były zarezerwowane dla konstrukcji specjalnych, które ze względów funkcjonalnych wymagały ochrony przed wodą. Zwykłe budynki zazwyczaj nie były uszczelniane, ponieważ nie posiadały podpiwniczenia, a ich dachy były w większości spadziste.
Technika hydroizolacji (w sensie ochrony budynku) pojawiła się dopiero w wyniku rozwoju odpowiednich materiałów uszczelniających, które stały się dostępne w dużych ilościach. Jednocześnie wraz ze wzrostem liczby ludności oraz dalszym rozwojem przemysłu, rzemiosła i handlu konieczne stało się zwiększenie liczby budynków mieszkalnych, fabryk i hal, z których część była już podpiwniczona, a ze względów funkcjonalnych musiały być uszczelnione [ 1 – 3 ].
Aby niepożądana wilgoć nie dostawała się do ścian, konstrukcje w obszarze stykającym się z gruntem były początkowo budowane z bardzo gęstych naturalnych materiałów budowlanych z danego regionu, takich jak mur z granitu. Oznaczało to, że pewna nieszkodliwa ilość wilgoci w murze piwnicy była tolerowana, a nawet pożądana, ponieważ stwarzała korzystne warunki do przechowywania żywności.
Znajomość historii i rozwoju hydroizolacji budynków jest szczególnie ważna przy dzisiejszych naprawach i modernizacjach zachowanych starych budynków, aby móc wyprowadzić i podjąć poprawne technicznie działania [ 3 ].
W przeszłości do wykonywania uszczelnień poziomych stosowano m.in. szkło w postaci tafli lub szkła tłuczonego. Tafle szklane o grubości do 5 mm układano w warstwie zaprawy, a ich spoiny klejono. Natomiast tafle o grubości 3,5 mm układano w warstwie piasku.
Od połowy XX w. dostępne są płyty z włókna szklanego. Jest to materiał, w którym zamiast włókien organicznych zastosowano włókno szklane. Ze względu na swoje nieorganiczne pochodzenie, membrana taka nie gnije oraz wykazuje niską nasiąkliwość. Materiał ten jednak nie sprawdził się w technice uszczelnień [ 3 ].
Stosowano również uszczelnienia metalowe, które w budownictwie mieszkaniowym cieszyły się sporym powodzeniem jeszcze w drugiej połowie XX w. [ 3 ]. Z dużym powodzeniem stosowano produkty ołowiane – najczęściej w postaci ołowiu walcowanego – który spełniał „konieczne warunki dobrej jakości”, za jakie uznawano elastyczność, odporność na wodę i nieprzepuszczalność [ 12 ].
Stosowano również cienkie paski blachy falistej o grubości od 0,1 do 0,2 mm wykonane z miedzi, cynku, aluminium lub stopów aluminium. Hydroizolacja taka była wyjątkowo odporna na naprężenia mechaniczne i statyczne, dlatego też stosowano ją przy bardzo intensywnym obciążeniu wodą. Arkusze blachy były spawane, względnie łączone masą bitumiczną. Bitum pełnił w tym wypadku podwójną rolę – masy klejącej oraz uszczelnienia połączenia arkuszy. Uszczelnienie powierzchniowe zapewniane było przez blachę falistą.
W pewnym okresie do wykonania uszczelnienia z blachy używano odpowiednio przygotowanej gliny. Wysoce plastyczną glinę zamiast z wodą mieszano w takim wypadku z ługiem siarczynowym uzyskiwanym podczas produkcji celulozy. W ten sposób powstawał rodzaj masy klejowej, stanowiącej alternatywę dla bitumu, którego brakowało po II wojnie światowej. Technologia ta jednak się nie sprawdziła, dlatego zabezpieczenia takie można spotkać jedynie w budynkach, które były budowane lub remontowane do około 1955 r. ( RYS. 3 ) [ 3 ].
Wadą uszczelnień blaszanych była wolna przestrzeń występująca między hydroizolacją a podłożem, do której – w przypadku niewielkiego nawet uszkodzenia – dostawała i gromadziła się woda, doprowadzając do zawilgocenia przegrody [ 12 ].
Rosnący rozwój przemysłu na początku XIX w. umożliwił pozyskiwanie smoły w procesie koksowania lub odgazowania węgla kamiennego podczas ogrzewania go w piecach koksowniczych (względnie retortach gazowniczych) do temperatury 800–1300°C bez dostępu powietrza [ 3, 5 ].
Smoła jest produktem płynnym lub półstałym, ciemnoczarnym lub brązowawym, powstającym w wyniku rozkładu termicznego (pirolizy) organicznych substancji naturalnych, takich jak węgiel kamienny, węgiel brunatny i drewno. Smoła składa się głównie z mieszanin węglowodorów. Skład różni się w zależności od pochodzenia. Smoła zawiera m.in. duże ilości wielopierścieniowych węglowodorów aromatycznych (WWA) – np. naftalen, benzo(a)piren – fenoli i krezoli. Lotne WWA i fenole/krezole są odpowiedzialne za typowy zapach smoły. W różnych procesach destylacji wytwarzane są różne odmiany smoły: miękka, średnio-twarda i twarda – do uszczelnienia stosowano jedynie smołę miękką [ 3 ].
Choć wynalezienie papy smołowej przypisuje się żyjącemu w XVIII w. radcy administracji szwedzkiej Faxowi [13], dopiero w latach 40. XIX w. została do tego stopnia udoskonalona, że przyjęła się jako materiał uszczelniający. Za ojca technologii krycia papą uznawany jest Friedrich Wilhelm Buttel, w 1841 r. wydał on monografię [ 14 ], w której po raz pierwszy opisał papę smołową stosowaną do krycia neoklasycystycznych dachów płaskich. Papy smołowe produkowane były w Ameryce już w połowie XIX w., podczas gdy w Europie dopiero dzięki ożywieniu gospodarczemu pod koniec XIX w., związanemu z rozwojem stali, nagłym wzrostem liczby ludności i dalszym rozwojem technicznym, powstały pierwsze wyroby uszczelniające wytwarzane przemysłowo, z których część zachowała się w budynkach z przełomu wieków [ 3 ].
W pierwszych latach XX w. do uszczelniania budynków zaczęto stosować również asfalt – materiał często utożsamiany ze smołą, chociaż są to zasadniczo różne substancje. Doprowadził do tego ścisły związek chemiczny i pewne podobieństwa fizyczne (struktura koloidalna, lepkość, zależność od temperatury). Asfalt to produkt koloidalny, którego środkiem dyspergującym jest olej mineralny i faza rozproszona żywic naftowych, występujący naturalnie lub pozyskiwany w procesie destylacji ropy naftowej.
Impuls do rozwoju przemysłowego produktów asfaltowych i rozprzestrzeniania się tego materiału w hydroizolacji budynków nastąpił około 1920 r., kiedy to na szerszą skalę rozpoczęto destylowanie ropy naftowej w celu uzyskania paliwa dla nowo powstałego przemysłu samochodowego i lotniczego [ 3 ].
Wraz z rozwojem produktów smołowych, a później asfaltowych, po raz pierwszy stało się możliwe wytwarzanie na skalę przemysłową produktów do uszczelniania budynków przy rozsądnym nakładzie technicznym i finansowym, jak również stosowanie materiałów hydroizolacyjnych w sposób celowy przy budowie budynków mieszkalnych i przemysłowych.
Kolejny gwałtowny wzrost produkcji materiałów hydroizolacyjnych nastąpił w latach 30. XX w., kiedy pojawiły się pierwsze folie z tworzyw sztucznych. Po drugiej wojnie światowej opracowano membrany bitumiczne z wkładkami z włókna szklanego i tkaniny szklanej oraz nowe membrany z tworzyw sztucznych. Nowe techniki przetwarzania, np. papy termozgrzewalne oraz modyfikowane tworzywami sztucznymi grubowarstwowe masy bitumiczne do dziś stosowane są do hydroizolacji budynków.
Wraz ze wzrostem wiedzy badawczo-rozwojowej liczba technik uszczelniania i materiałów uszczelniających, które obejmują również beton wodonieprzepuszczalny, tynki uszczelniające i mineralne szlamy uszczelniające, stała się bardziej obszerna i wyspecjalizowana [ 3 ].
Wśród materiałów bitumicznych (do których zalicza się zarówno smoły i asfalty, ale również paki, tj. produkty stanowiące pozostałość po destylacji smół, kwasów tłuszczowych, wosków itp.) stosowanych do uszczelniania elementów przyziemia budynków wymienić należy następujące wyroby [ 15 – 20 ]:
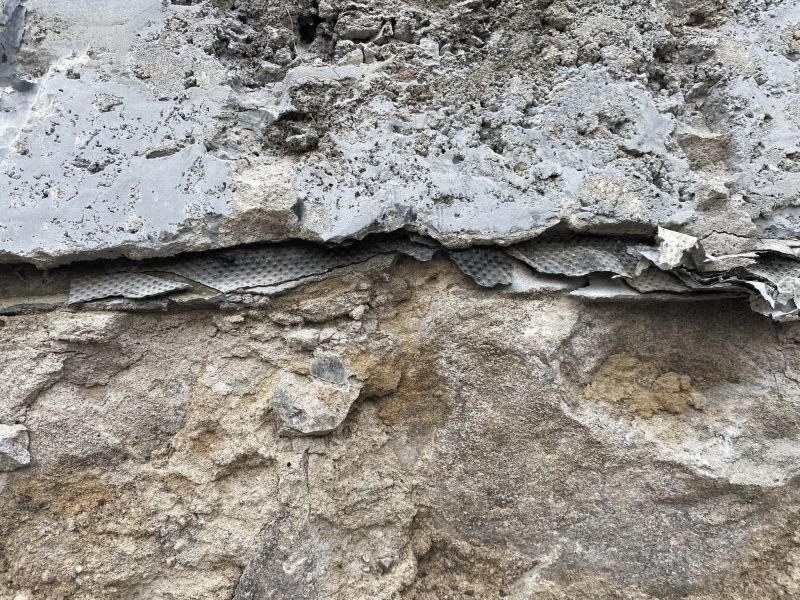
FOT. 3. Hydroizolacja pozioma z papy smołowej z przyklejoną folią metalową w kamienicy z przełomu XIX i XX w.; fot.: B. Monczyński
- Materiały izolacyjne do gruntowania powierzchni – roztwory asfaltowe lub asfalty upłynnione, rozpuszczone w lotnych rozpuszczalnikach, stosowane do gruntowania powierzchni budowli przed nałożeniem właściwej Izolacji asfaltowej oraz do wykonywania samodzielnych izolacji najlżejszego typu. Obok roztworów gruntujących na bazie asfaltu stosowano również roztwory na bazie smołowej. Roztwory takie składały się ze średnio miękkiego paku rozpuszczonego w lotnym rozpuszczalniku.
- Masy izolacyjne powłokowe (na zimno lub na gorąco) – stosowane były do wykonywania izolacji przeciwwilgociowej typu lekkiego lub średniego przez nałożenie powłok bitumicznych na uprzednio zagruntowane powierzchnie. Powłoki te, po ostudzeniu lub odparowaniu składników lotnych, tworzyły szczelne jednolite warstwy.
- Lepiki (na zimno lub na gorąco) – asfalty lub mieszaniny asfaltów z dodatkiem wypełniaczy mineralnych (pyłowych i włóknistych) oraz substancji polepszających właściwości lepiku (jak np. kalafonia, paki tłuszczowe, żywice syntetyczne). Lepiki smołowe otrzymywane były ze smoły surowej z węgla kamiennego lub przez zmieszanie paku z olejami smołowymi ciężkimi. Lepiki stosowane były do przyklejania papy do podłoża oraz do wykonywania samodzielnych powłok izolacyjnych.
- Mastyksy i zaprawy – masy otrzymywane przez zmieszanie na gorąco bitumu z wypełniaczami mineralnymi pyłowymi i włóknistymi, ewentualnie również z dodatkami poprawiającymi właściwości masy, stosowane na gorąco (rzadziej na zimno) do wykonywania samodzielnych powłok ochronnych.
- Emulsje bitumiczne – zawiesiny drobnych cząstek bitumu w wodzie, uzyskiwane dzięki zastosowaniu emulgatorów i stabilizatorów. Emulgatory ułatwiają rozbicie bitumu na drobne cząsteczki oraz uniemożliwiają ich zlewanie się i łączenie ze sobą. Stabilizatory zapobiegają rozkładaniu się emulsji przy zetknięciu np. z materiałem mineralnym, zwiększają trwałość zawiesiny, a także przedłużają czas rozkładu emulsji. W budownictwie stosowano (i nadal się stosuje) głównie emulsje asfaltowe (emulsje smołowe miały mniejsze znaczenie).
- Papy – materiał bitumiczny rolowy, składający się z wkładki (np. z tektury surowej lub filcowej, tkaniny z włókien naturalnych lub sztucznych, folii) nasyconej i ewentualnie dodatkowo powleczonej smołą lub asfaltem, z posypką lub bez posypki bądź przyklejoną folią metalową (FOT. 3).
- Asfalt lany – masa złożona z kruszywa mineralnego (grysiku kamiennego lub żwirku), piasku, mączki mineralnej i asfaltu jako lepiszcza, stosowane jako wodoszczelne i niepylące posadzki w pomieszczeniach zagrożonych wilgocią (w tym w posadzkach na gruncie).
Literatura
1. E. Cziesielski, „Geschichtliche Entwicklung der Abdichtungstechnik”, [w:] E. Cziesielski (red.), „Lufsky Bauwerksabdichtung”, Teubner, Wiesbaden, 2006, pp. 5–10.
2. J. Szewczyk, „Hydroizolacja elementów budowli w wybranych okresach historii architektury, czyli o uszczelnieniach z nietypowych materiałów, o dawnych impregnatach, drenażach i pokrewnych rozwiązaniach budowlanych”, Oficyna Wydawnicza Politechniki Białostockiej, Białystok 2019.
3. J. Weber, „Entwicklung der Bauwerksabdichtung”, [w:] J. Weber, V. Hafkesbrink (red.), „Bauwerksabdichtung in der Altbausanierung. Verfahren und juristische Betrachtungsweise”, Springer Vieweg, Wiesbaden 2018, pp. 1–24.
4. Biblia Tysiąclecia, Pismo Święte Starego i Nowego Testamentu, Wydawnictwo Pallottinum, Poznań 2000.
5. B. Stefańczyk, P. Mieczkowski, „Lepiszcza bitumiczne i wyroby z nic”, [w:] B. Stefańczyk (red.), „Budownictwo ogólne. Tom 1. Materiały i wyroby budowlane”, Arkady, Warszawa 2005, s. 743–821.
6. R.Z. Ciesielski, „Asfalt naturalny w budownictwie”, nakładem Księgarni Ludwika Fiszera w Łodzi, Łódź 1922.
7. Praca zbiorowa, „Wielka historia świata – tom V”, Oxford Educational, Warszawa 2005.
8. M. Vitruvius Pollio, „O architekturze ksiąg dziesięć”, Pruszyński i S-ka, Warszawa 1999.
9. L.M. Seymour, J. Maragh, P. Sabatini, M. Di Tommaso, J.C. Weaver, A. Masic, „Hot mixing: Mechanistic insights into the durability of ancient Roman concreto”, „Science advances” vol. 9, no. 1, 2023.
10. M.D. Jackson, S.R. Mulcahy, H. Chen, Y. Li, Q. Li, P. Cappelletti, H. Wenk, „Phillipsite and Altobermorite mineral cements produced through lowtemperature water-rock reactions in Roman marine concreto”, „American Mineralogist”, vol. 102, no. 7, 2017, pp. 1435–1450.
11. R. Wójcik, „Odtwarzanie izolacji poziomych”, „Builder” 1/2008, s. 90–93.
12. H. Stankiewicz, „Ochrona budowli od wody”, Politechnika Warszawska, Warszawa 1938.
13. R.Z. Ciesielski, „Papa (dachowa izolacyjna cement drzewny)”, nakładem Księgarni Ludwika Fiszera w Łodzi, Łódź 1922.
14. F.W. Buttel, „Practische Erfahrungen Über Dornsche Dächer Nebst Ausführlicher Beschreibung, Kostenberechnung Und Zeichnung Solcher Constructionen, Welche Denselben Größere Dauer Und Dichtigkeit Geben, Und Einem Anhange: Über Die Anwendung Der Flachen Dächer Bei Ökonomi”, Neubrandenburg 1841.
15. H. Stankiewicz, „Zabezpieczenie budowli przed wilgocią, wodą gruntową i korozją”, Arkady, Warszawa 1959.
16. W. Danilecki, M. Mączyński, „Izolacje przeciwwilgociowe. Materiały, projektowanie, wykonawstwo”, Arkady, Warszawa 1957.
17. E. Janczewski, I. Płoński, „Spoiwa, lepiszcza i zaprawy budowlane”, [w:] W. Żenczykowski (red.), „Budownictwo ogólne – tom 1”, Arkady, Warszawa 1976, s. 105–202.
18. Z. Rojek, A. Gudaj, „Wykonywanie izolacji przeciwwodnych”, Arkady, Warszawa 1980.
19. W. Danilecki, „Izolacje przeciwwilgociowe i przeciwwodne”, [w:] W. Żenczykowski (red.), „Budownictwo ogólne – tom 3/1”, Arkady, Warszawa 1987, s. 250–313.
20. T. Dzięgielewski (red.), „Mały ilustrowany słownik budowlany”, Arkady, Warszawa 1971.