Konstrukcje betonowych posadzek przemysłowych
Concrete industrial flooring structures
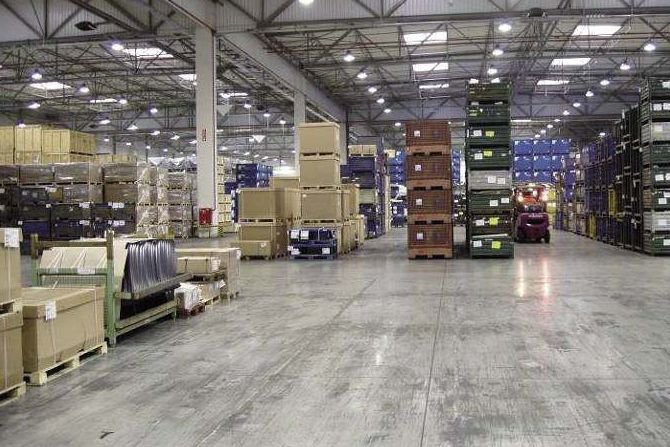
FOT. 1. Posadzka przemysłowa w magazynie
Archiwum autora
Większość wad betonowych posadzek przemysłowych ujawnia się w początkowym okresie użytkowania, a nawet zaraz po zakończeniu robót posadzkowych. Naprawy uszkodzeń są z reguły kłopotliwe, kosztowne i nie pozostają bez wpływu na estetykę oraz przyszłą eksploatację obiektów.
Zobacz także
Tremco CPG Poland Sp. z o.o. Flowcrete – bezspoinowe posadzki żywiczne w przemyśle

Bezspoinowe posadzki żywiczne są często nazywane posadzkami przemysłowymi. Ze względu na ich właściwości, m.in. trwałość, wytrzymałość mechaniczną, w tym odporność na ścieranie, szczelność i nienasiąkliwość...
Bezspoinowe posadzki żywiczne są często nazywane posadzkami przemysłowymi. Ze względu na ich właściwości, m.in. trwałość, wytrzymałość mechaniczną, w tym odporność na ścieranie, szczelność i nienasiąkliwość oraz łatwość utrzymania w czystości, rozwiązania posadzkowe na bazie żywic syntetycznych są powszechnie stosowane w zakładach produkcyjnych z różnych branż.
dr inż. Krzysztof Pogan, WestWood® Kunststofftechnik GmbH Rozwiązania dla parkingów wielopoziomowych i podziemnych

Parkingi wielopoziomowe i podziemne to niewątpliwie budowle, których nie można porównać do powszechnie spotykanych w budownictwie tradycyjnych budowli żelbetowych. Swoimi właściwościami przypominają one...
Parkingi wielopoziomowe i podziemne to niewątpliwie budowle, których nie można porównać do powszechnie spotykanych w budownictwie tradycyjnych budowli żelbetowych. Swoimi właściwościami przypominają one raczej budowle drogowe, jak np. mosty. Zatem muszą spełniać wysokie wymagania w zakresie trwałości – powinny możliwie długo pozostać odporne na oddziaływanie warunków zewnętrznych i służyć przez długi czas.
dr inż. Krzysztof Pogan Rysy w posadzkach nawierzchni garażu podziemnego

Omawiany obiekt, w którym usytuowane są garaże podziemne, został zaprojektowany zgodnie z wytycznymi zawartymi w decyzji o warunkach zabudowy jako zespół trzech budynków zlokalizowanych na działce w sposób...
Omawiany obiekt, w którym usytuowane są garaże podziemne, został zaprojektowany zgodnie z wytycznymi zawartymi w decyzji o warunkach zabudowy jako zespół trzech budynków zlokalizowanych na działce w sposób kontynuujący wnętrza urbanistyczne działek sąsiednich.
Abstrakt |
---|
W artykule przedstawiono współczesne wymagania dotyczące wykonania betonowych podkładów posadzek przemysłowych. Omówiono różne rodzaje konstrukcji i szczelin dylatacyjnych. Podano tolerancje wymiarowe. Concrete industrial flooring structuresThe paper presents the contemporary requirements for execution of concrete underlayment of industrial flooring. The discussion covered the various types of structures and expansion joints. Dimension tolerances are given. |
Pod pojęciem posadzki przemysłowej rozumie się nawierzchnie wewnętrzne w obiektach przemysłowych, magazynach i centrach handlowych. Zdecydowaną większość posadzek przemysłowych stanowią posadzki betonowe.
Warstwę wierzchnią posadzek przemysłowych stanową:
- odpowiednio zatarta powierzchnia, najczęściej dodatkowo utwardzona i związana z betonowym podłożem (podkładem),
- nawierzchnia żywiczna,
- nawierzchnia mineralna (np. lastrico),
- płytki ceramiczne,
- kamień.
Betonowe posadzki przemysłowe wykonuje się bezpośrednio na odpowiednio przygotowanym i zagęszczonym nośnym podłożu gruntowym lub na stropach międzykondygnacyjnych.
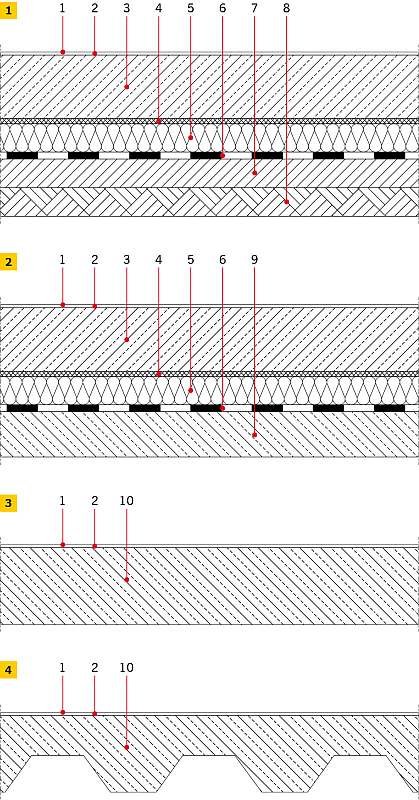
RYS. 1-4. Schematy układu warstw posadzek przemysłowych: posadzka na gruncie (1), posadzka na stropie (2), posadzka stanowiąca jednocześnie element nośny konstrukcji stropu (3); 1 – warstwa wierzchnia (posadzka), 2 – ewentualnie warstwa sczepna: klej, lepik, 3 – betonowy podkład, 4 – ewentualnie warstwa ochronna, 5 – ewentualnie izolacja termiczna lub akustyczna, 6 – izolacja przeciwwilgociowa lub paroszczelna, 7 – ewentualnie warstwa „chudego betonu”, 8 – zagęszczone nośne podłoże gruntowe, 9 – strop, 10 – beton pełniący funkcję nośną stropu; rys. archiwum autora
Niekiedy betonowa posadzka przemysłowa stanowi jednocześnie element nośny konstrukcji stropu – nadbeton w stropach prefabrykowanych lub w stropach betonowanych na blachach fałdowych. Na RYS. 1-4 przedstawiono schematy układu warstw w posadzkach przemysłowych.
Pomimo wieloletnich doświadczeń i stosowania zaawansowanych technologii betonowe posadzki przemysłowe wykazują ciągle nieproporcjonalnie dużą liczbę uszkodzeń i wad [1, 2, 3]. Dla wykonawców stanowi to z reguły poważne problemy przy odbiorze obiektów - częste reklamacje w okresach gwarancyjnych. Przykłady uszkodzeń betonowych posadzek przemysłowych są często przytaczane w literaturze technicznej i w materiałach licznych konferencji naukowo- technicznych.
Konstrukcje podkładów
Konstrukcje betonowych podkładów zależą od zakładanych obciążeń posadzek siłami rozłożonymi na powierzchni i siłami skupionymi (reakcje z kół urządzeń transportowych, reakcje pod stopami regałów), a także od obciążeń termicznych, warunków gruntowych (niejednorodne podłoże) i technologii wykonania (podkłady dylatowane, posadzki bezspoinowe).
Podkłady posadzek przemysłowych wykonuje się jako:
- płyty betonowe niezbrojone (RYS. 5);
- płyty betonowe zbrojone siatkami zgrzewanymi. Siatki rozmieszczane są:
- w środku grubości płyt (RYS. 6),
- przy dolnej powierzchni (RYS. 7)
- lub w 2 warstwach - przy dolnej i górnej powierzchni (RYS. 8).
Minimalna otulina zbrojenia powinna wynosić 50 mm; - płyty ze zbrojeniem rozproszonym (włókna stalowe, włókna syntetyczne - polipropylenowe, polietylenowe, nylonowe) (RYS. 9);
- płyty ze zbrojeniem siatkami i ze zbrojeniem rozproszonym (RYS. 10);
- płyty sprężone (RYS. 11).
Betonowe podkłady ze względu na odkształcenia skurczowe i termiczne wymagają dylatowania. Wyróżnia się następujące rodzaje szczelin dylatacyjnych podkładów:
- dylatacje konstrukcyjne,
- dylatacje stykowe,
- dylatacje skurczowe.
Dylatacje konstrukcyjne, zwane także termicznymi, lub rozszerzania (movement, isolationjoints) wykonuje się:
- wokół obwodu posadzki przy ścianach zewnętrznych pomieszczenia,
- wokół obwodu niezależnych fundamentów, słupów kanałów itp.
W wypadku dużych powierzchni w halach (niewielkie wahania temperatur otoczenia) maksymalna odległość między dylatacjami termicznymi nie powinna przekraczać 90 m [4].
W wypadku podkładów zewnętrznych (place składowe, drogi dojazdowe) zaleca się, by rozstaw dylatacji termicznych nie przekraczał:
- 50 m w wypadku wykonywania robót betonowych w temp. otoczenia powyżej 20°C
- i 25 m w wypadku wykonywania robót w temp. poniżej 20°C [5].
Dylatacje konstrukcyjne podkładów na stropach międzykondygnacyjnych wykonuje się bezpośrednio:
- nad dylatacjami konstrukcji stropu,
- wzdłuż ścian,
- w liniach otworów drzwiowych (skokowa zmiana szerokości).
Szerokość dylatacji konstrukcyjnych przyjmuje się zazwyczaj równą 20 mm. Dylatacje konstrukcyjne przechodzą przez całą grubość podkładu.
Dylatacje konstrukcyjne między poszczególnymi polami posadzki powinny być dyblowane. Dylatacji konstrukcyjnych występujących wokół ścian zewnętrznych, przy fundamentach, kanałach, studzienkach itp. najczęściej się nie dybluje.
Dylatacje stykowe, zwane także dylatacjami dziennymi, dylatacjami roboczymi, dylatacjami technologicznymi (formedjoints, constructionjoints), determinowane są technologią wykonywania płyty podkładu. Występują one jako dylatacje podłużne i dylatacje poprzeczne na obrzeżach kolejnych "dziennych" pasów betonowania. Szczeliny te powinny być dyblowane.
Dyblowanie szczelin powinno się stosować zawsze przy obciążeniach skupionych Q przekraczających 40 kN. Wzdłuż linii styków dylatacje są zwykle nacinane.
Na obrzeżach szczelin stykowych stosowane są często specjalne profile dylatacyjne. Szerokość nacięć dylatacji stykowych wynosi zazwyczaj 3-6 mm.
Rozstaw dylatacji stykowych zależy od technologii wykonywania:
- metoda wąskich pasów (4-8 m) lub
- metoda szerokich pasów (8-18 m)
- oraz metoda wielkich płaszczyzn i wynosić może maks. 40-50 m.
W podkładach wykonywanych na stropach szczeliny stykowe należy sytuować najlepiej w osiach głównych belek nośnych.
Dylatacje skurczowe zwane są także dylatacjami pozornymi lub dylatacjami nacinanymi (sawnjoints, contractionjoints). Nacięcia wykonuje się na głębokość 1/3 grubości betonowej płyty. Nacięcia wykonuje się pod kątem prostym, a stosunek dłuższego boku do krótszego nie powinien być mniejszy niż 1,5. Szerokość dylatacji wynosi 3-6 mm. Przy obciążeniach skupionych Q > 40 kN szczeliny skurczowe zaleca się dyblować.
Maksymalny rozstaw dylatacji skurczowych zaleca się przyjmować z następujących warunków:
- 25-35 mm grubości podkładu,
- 4-6 m w wypadku standardowych warunków wykonania podkładów,
- 10 m w wypadku specjalnych warunków wykonania (mała ilość wody w mieszance betonowej, niskie ciepło hydratacji, efektywna ochrona przed wiatrem i słońcem, staranna pielęgnacja.
Na RYS. 12-15 przedstawiono przykładowe rozwiązania dylatacji betonowych podkładów.
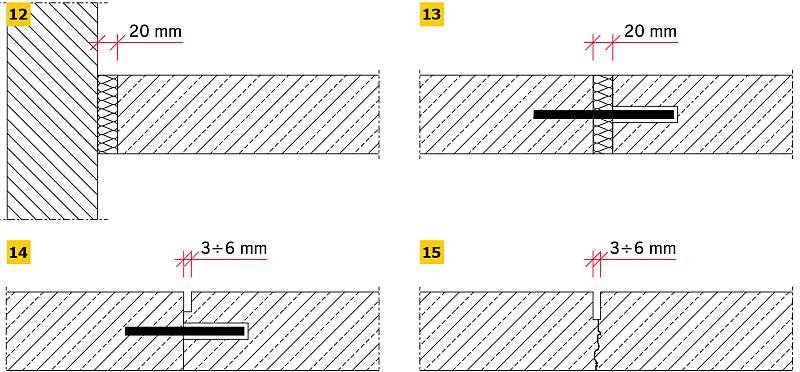
RYS. 12–15. Konstrukcje dylatacji podkładów: dylatacje konstrukcyjne (12, 13), dylatacje stykowe (14), dylatacje skurczowe (15); rys. archiwum autora
Wymagania
Wymagania stawiane betonowym podkładom posadzek przemysłowych zależą od ich przeznaczenia, obciążeń, rodzaju nawierzchni. Są one zróżnicowane w poszczególnych normach (PN‑EN 13813:2003 [7], EN 1504-10:2002 [8]) i wytycznych [9, 10].
Dylatacje w zależności od warunków eksploatacji mogą być otwarte lub zabezpieczone od góry elastycznymi masami. Na RYS. 16-19 przedstawiono przykładowy rozkład dylatacji podkładu betonowego na gruncie oraz szczegóły dylatacji słupów. Dylatacje powinny być projektowane w osiach słupów konstrukcji obiektu. Nie należy sytuować dylatacji podłużnych na projektowanych pasach ruchu urządzeń transportowych.
Wypełnienie szczelin dylatacyjnych masami elastycznymi powinno się wykonywać w następujący sposób:
- sfazowanie naroży szczelin szlifierką na głębokość ok. 2 mm,
- oczyszczenie i przesuszenie oraz wciśnięcie wałka oporowego z tworzywa sztucznego,
- zagruntowanie szczeliny i wypełnienie, do poziomu dolnej krawędzi sfazowania, elastyczną masą uszczelniającą na głębokość równą szerokości szczeliny.
Wypełnienie szczelin powinno być wykonywane po wystąpieniu największych odkształceń skurczowych, czyli nie wcześniej niż ok. 6 miesięcy od zabetonowania podkładu. Czas ten zależy od warunków otoczenia (temperatura, wilgotność). Często przyrost odkształceń skurczowych występuje w okresie pierwszego okresu grzewczego i wówczas dochodzi do odspojeń wcześniej założonych mas wypełniających od krawędzi szczelin.
W celu ograniczenia liczby dylatacji w betonowych posadzkach na podłożu gruntowym wykonywane są także tzw. posadzki bezspoinowe (jointlessslabs on ground). W posadzkach tego typu wykonuje się jedynie dylatacje stykowe i konstrukcyjne.
Posadzki bezspoinowe wymagają większego zbrojenia, najczęściej rozproszonego (włókna stalowe w ilości 40-60 kG/m3) w celu zabezpieczenia przed odkształceniami skurczowymi.
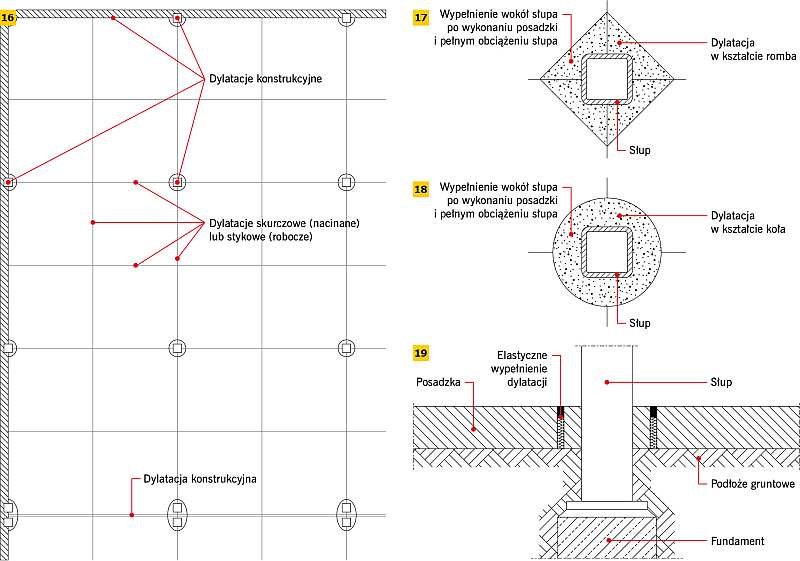
RYS. 16-19. Dylatacje betonowego podkładu: rozmieszczenie szczelin dylatacyjnych i szczegół dylatacji słupa; rys. ACI 302.1 R-04 [6]
Grubość podkładu betonowego
Określa się ją na podstawie obliczeń. Uzależniona jest od wartości obciążeń i sposobu ich przekazania (rozłożone, skupione), podatności podłoża gruntowego, wytrzymałości betonu podkładu. Przy obciążeniach siłami skupionymi (reakcje z kół, stóp regałów) o grubości podkładu decydują obciążenia krawędziowe (przy końcach płyt i przy dylatacjach).
W publikacji "Concrete floors for warehousing and distribution facilities: fit for purpose" [11] podano przykładowo obliczone metodą Westergaarda grubości płyt betonowych o charakterystycznej wytrzymałości fck= 40 MPa, w zależności od współczynnika podatności gruntu K, dla powierzchni magazynowych silnie obciążonych (obciążenie rozłożone 7,25 kN/m2, wózki o udźwigu do 1,5 t.) - TAB. 1.
Minimalna grubość betonowego podkładu według zaleceń amerykańskich [12] powinna wynosić:
- 127 mm (5 cali) przy obciążeniu wózkami na kołach pompowanych,
- 152 mm (6 cali) przy obciążeniu wózkami z kołami z pełnej gumy, stali lub tworzyw sztucznych.
Podobne zalecenia stosuje się np. na Słowacji [13], przy czym minimalną grubość podkładu uzależnia się od wytrzymałości betonu:
- 120 mm dla podkładów z betonu C30/37,
- 130 mm dla podkładów z betonu C25/30,
- 150 mm dla podkładów z betonu C20/25.
Najczęściej grubości podkładów betonowych w posadzkach przemysłowych wykonywanych na gruncie wynoszą od 150 mm do 300 mm.
Mniejsze grubości podkładów można przyjmować w podkładach wykonywanych na stropach bez warstwy rozdzielającej (związane z podłożem) lub w podkładach pełniących funkcję nośną w stropach zespolonych.
Minimalna grubość podkładów w tych wypadkach powinna wynosić:
- 50 mm w wypadku podkładu zbrojonego
- i 20 mm przy podkładzie niezbrojonym związanym z podłożem.
Wytrzymałość betonu podkładu
Wytrzymałość ta ustalana jest w fazie projektu posadzki w zależności od obciążeń i przeznaczenia. Jako minimalną wartość wytrzymałości na ściskanie przyjmuje się w większości wypadków wytrzymałość odpowiadającą klasie B 25. Niższą klasę B 20 można przyjąć jedynie w wypadku podkładów pod posadzki o małym obciążeniu (obiekty użyteczności publicznej).
W wypadku posadzek silnie obciążonych (intensywny ruch pojazdów na twardym ogumieniu, transport towarowy, bardzo intensywny ruch pieszy) i posadzek o wysokich wymaganiach płaskości powierzchni (magazyny wysokiego składowania, centra dystrybucyjne) beton podkładu powinien odpowiadać klasie min. B 37 [12].
Według doświadczeń niemieckich zawartych w pracy „Posadzki przemysłowe o dużej odporności na ścieranie [14] wymagania w stosunku do betonu posadzkowego uzależniono od przyjętych klas obciążenia posadzki – TAB. 2.
Inne wymagania
Inne wymagania dotyczące betonu mają istotne znaczenie dla przewidywanego sposobu wykończenia powierzchni i warunków eksploatacji.
- W podłożach pod systemy posadzkowe na bazie żywic epoksydowych istotne znaczenie ma wilgotność betonu, temperatura i stan przygotowania powierzchni.
- Wilgotność wagowa betonowego podłoża pod posadzki żywiczne w większości wypadków nie może być większa niż 4%.
- Powierzchnia powinna spełniać wymagania normy europejskiej EN 1504-10:2002 [8] w zakresie czystości, szorstkości, zarysowań, wytrzymałości na odrywanie, zanieczyszczenia chlorkami lub innymi szkodliwymi substancjami i głębokości ich wniknięcia, głębokości karbonatyzacji, zawilgocenia, temperatury, stopnia skorodowania zbrojenia.
- W nawierzchniach zewnętrznych ogranicza się nasiąkliwość, przesiąkliwość, śliskość oraz mrozoodporność betonu.
- W szczególnych wypadkach wymaga się także spełnienia szczególnych warunków odporności ogniowej i chemicznej.
Minimalna ilość zbrojenia rozproszonego
Obecnie w większości wypadków w podłożach betonowych stosuje się zbrojenie rozproszone w postaci włókien tekstylnych i stalowych. Minimalna ilość zbrojenia rozproszonego dodawanego do mieszanki betonowej zależy od wielkości obciążeń i rodzaju stosowanego zbrojenia.
Według zaleceń słowackich [13] włókna polipropylenowe stosuje się w ilości 0,6-1,0 kg/m3. Należy się tu kierować zasadą: im więcej cementu na 1 m3 betonu, tym więcej włókien polipropylenowych. Podobne zalecenia zawierają wytyczne polskie [15].
W wypadku włókien stalowych minimalna ich ilość w 1 m3 zależy od stosunku długości włókna l do jego średnicy d oraz od wielkości obciążeń. W TAB. 3 [16] podano minimalne ilości zbrojenia na 1 m3 betonu w zależności od smukłości włókien.
W posadzkach wykonanych bez warstwy ścieralnej występuje często problem obecności włókien na powierzchni posadzki.
Francuskie zalecenia SolsIndustriels a base de ciment [17] rozróżniają dwie klasy wykończenia płyty: dobrą oraz średnią, i w zależności od klasy podają maksymalną liczbę włókien widocznych na powierzchni posadzki - TAB. 4.
Równość powierzchni
Równość ma istotne znaczenie dla bezpiecznej eksploatacji i własności użytkowych.
- Dokładność wykonania podkładu powinna być każdorazowo określona w dokumentacji technicznej.
- Wartości dopuszczalnych odchyłek wymiarowych zależą od wymaganej klasy dokładności i od sposobu wykończenia nawierzchni.
- W wypadku podkładów z integralną, utwardzaną przez zacieranie, warstwą posadzkową tolerancje wykonania podkładu są takie same, jak tolerancje dla samej posadzki.
- W wypadku podkładów pod posadzki żywiczne, mineralne, samopoziomujące, z płytek ceramicznych lub lastrykowych, tolerancje wykonania podkładu mogą być łagodniejsze w stosunku do tolerancji przyjmowanych dla nawierzchniowej warstwy.
- Szczególnie ostre wymagania odnośnie równości powierzchni podkładów i posadzek są przyjmowane w magazynach wysokiego składowania, zwłaszcza przy wąskich przejazdach między regałami.
W krajowych Warunkach technicznych wykonania i odbioru robót budowlano-montażowych [9] wymaga się, by podkład miał powierzchnię równą, stanowiącą płaszczyznę poziomą lub pochyloną, zgodnie z ustalonym spadkiem.
- Powierzchnia podkładu sprawdzana 2-metrową łatą, przykładaną w dowolnym miejscu, nie powinna wykazywać prześwitów większych niż 5 mm.
- Odchylenie powierzchni podkładu od płaszczyzny (poziomej lub pochylonej) nie powinno przekraczać 2 mm/m i 5 mm na całej długości i szerokości obiektu.
W TAB. 5 podano klasyfikacje dokładności powierzchni zawarte w niemieckiej normie DIN 18202 [18].
W TAB. 6 podano klasyfikację dokładności powierzchni posadzek betonowych według normy angielskiej BS 8204 [19].
Wymagane tolerancje wykonania betonowych posadzek przemysłowych w magazynach wysokiego składowania zawarto w ConcreteSociety’s Technical Report TR 34 - 3rd Edition [10], traktowanym w wieku krajach jak norma.
Tolerancje równości powierzchni zależą do sposobu ruchu wózków na powierzchni posadzki - ruch swobodny, przypadkowy (FreeMovementareas FM - FOT. 1) lub ściśle określony (Defined Movementareas - FOT. 2) i od wysokości składowania.
Raport TR 34 nakazuje kontrolę 4 cech (RYS. 20-23):
- cecha I (przy ruchu określonym): nachylenia - różnica wysokości na długości 300 mm,
- cecha II (przy ruchu swobodnym i określonym): równość (płaskość powierzchni - różnice wysokości na 2 przyległych odcinkach o długości 300 mm (2×300 = 600 mm),
- cecha III (przy ruchu określonym) - różnica wysokości na długości rozstawu kół wózków - rozstaw do 1,5 m i powyżej 1,5 m,
- cecha IV: (przy ruchu swobodnym) różnice wysokości w punktach leżących na wytyczonej ortogonalnej siatce pomiarowej 3,0×3,0 m.
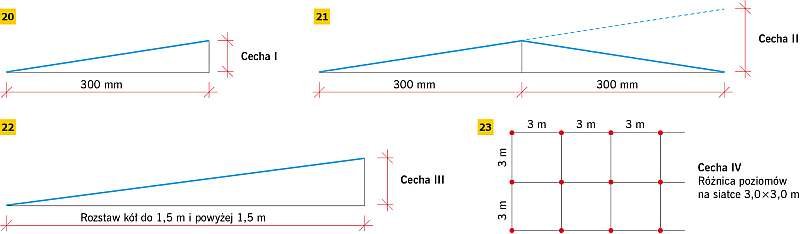
RYS. 20-23. Sposób określania parametrów równości powierzchni według TR 34 [10]; rys. archiwum autora
Według raportu TR34 [10] określa się odchyłki gwarantowane z 95% i 100% prawdopodobieństwem nieprzekroczenia wartości dopuszczalnych (TAB. 7 i TAB. 8).
Według normy amerykańskiej ASTM E1155 [20] dokładność wykonania powierzchni określa się w sposób statystyczny, dokonując pomiarów różnic wysokości w licznych punktach na powierzchni posadzki.
Oblicza się następnie dwie wartości F:
- FF charakteryzującą płaskość (flatness) powierzchni (RYS. 24) oraz
- FL charakteryzującą spoziomowanie (levelness) powierzchni (RYS. 25).
Zalecane wartości F dla różnych kategorii posadzek według „Concrete Slab Finishes and Use of F-number System” [21] podano w TAB. 9.
W TAB. 10 podano natomiast przybliżone wartości dopuszczalnych odchyłek mierzonych pod łatą o długości 3,0 m (10’) odpowiadające wartościom F z TAB. 9.
Literatura
- State of the Art Report of RILEM, Technical Committee TC 184-IFE: Industrial Floors (Rilem Raport nr 33), 2006.
- A. Garbacz, "Raport dotyczący stanu wiedzy i techniki w dziedzinie posadzek przemysłowych", "Materiały Budowlane", nr 5/2007, s. 2-5.
- L. Czarnecki, "Badania i rozwój posadzek przemysłowych", "Materiały Budowlane", nr 5/2007, s. 6-8.
- F.R. Neal, "Concrete industrial ground floors", "ICE. Thomas Telford", London 2002.
- PN-75/S-96015, "Drogowe i lotniskowe nawierzchnie z betonu cementowego".
- ACI 302.1 R-04: Guide for Concrete Floor and Slab Construction, "ACI Committee 302", 2004.
- PN-EN 13813:2003, "Podkłady podłogowe oraz materiały do ich wykonywania. Materiały. Właściwości i wymagania".
- EN 1504-10:2002, "Products and systems for the protection and repair concrete structures. Definitions, requirements quality control and evaluation of conformity".
- "Warunki techniczne wykonania i odbioru robót budowlano‑montażowych. Budownictwo Ogólne", "Arkady" Warszawa 1990.
- Technical Report 34, Third edition: "Concrete industrial ground floors - a quide to their design and construction", "The Concrete Society", Camberley 2003.
- N.I.H. Williamson, "Concrete floors for warehousing and distribution facilities: fit for purpose", "Proc. ICE Structures and Building", May 1996, s. 235–243.
- ACI 360 R-92: Design of Slabs on Grade "American Concrete Institute".
- P. Svoboda, J. Doležal, "Průmyslové podlahy a podlahy v objektech pozemnich staveb", "JAGA", Bratislava 2007.
- G. Zając, „Posadzki przemysłowe o dużej odporności na ścieranie", "Materiały Budowlane", nr 5/2007, s. 28-30.
- Materiały reklamowe firmy BAUTECH.
- Materiały reklamowe firmy BEKAERET.
- "Sols industriels a base de ciment", NIT 204 1997/06, CSTC.
- DIN 18202 04.97, "Toleranzen im Hochbau Bauwerke; Bauwerke".
- BS 8204-1:2003, "Screeds, bases and in situ floorings".
- ASTM 1155M-96 (2001), "Standard test method for determining FF floor flatness and FL floor levelness numbers".
- M. Stuard, "Concrete Slab Finishes and Use of F-number System".