Cementy niskoemisyjne w chemii budowlanej – podkłady podłogowe i betony
Low-emission cements in dry mixtures of construction chemicals. Part 5: Types of floor screed and concrete
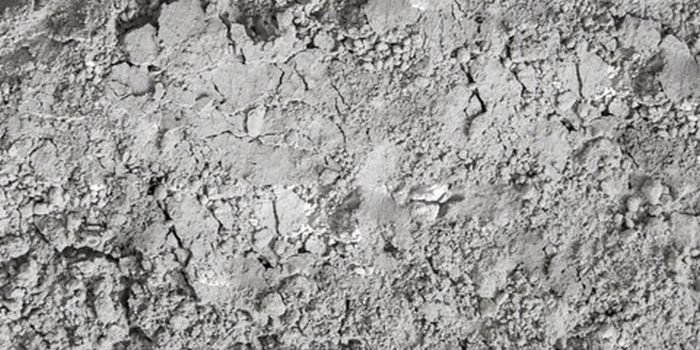
Cementy niskoemisyjne w chemii budowlanej – podkłady podłogowe i betony, fot. J. Sawicki
Droga do neutralności klimatycznej całego sektora budowlanego opiera się na szeregu działań związanych z obniżeniem śladu węglowego wbudowanego i operacyjnego. W całym procesie należy brać pod uwagę wszystkie potencjalne czynniki oraz źródła emisyjności, nawet te z pozoru niewielkie.
Zobacz także
BayWa r.e. Solar Systems novotegra: jakość, prostota i bezpieczeństwo

Z wyniku badań rynkowych, a także analiz i obserwacji prowadzonych nie w biurze, lecz na dachu, powstał bardzo wydajny system montażowy. Stworzony w ten sposób produkt umożliwia szybką i łatwą instalację.
Z wyniku badań rynkowych, a także analiz i obserwacji prowadzonych nie w biurze, lecz na dachu, powstał bardzo wydajny system montażowy. Stworzony w ten sposób produkt umożliwia szybką i łatwą instalację.
Bauder Polska Sp. z o. o. Nowoczesne rozwiązania na dachy płaskie

Szczelny dach płaski to gwarancja bezpieczeństwa dla użytkowników budynku oraz pewność wieloletniej i bezawaryjnej trwałości pokrycia. Obecnie od materiałów do izolacji i renowacji dachów wymaga się coraz...
Szczelny dach płaski to gwarancja bezpieczeństwa dla użytkowników budynku oraz pewność wieloletniej i bezawaryjnej trwałości pokrycia. Obecnie od materiałów do izolacji i renowacji dachów wymaga się coraz więcej – powinny być nie tylko wysokiej jakości, ale także przyjazne dla środowiska.
Czytaj całość »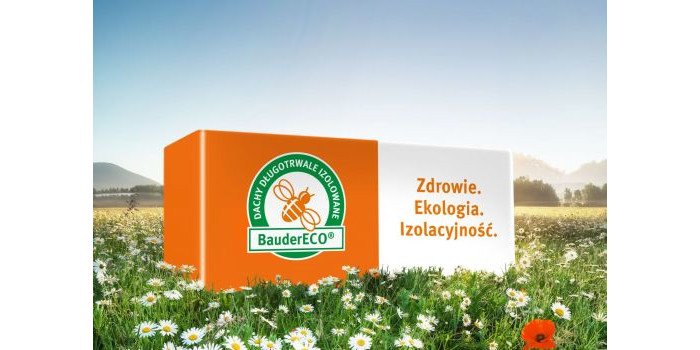
Bauder Polska Sp. z o. o. BauderECO – nowoczesna termoizolacja dachowa
Ekologiczna termoizolacja dachowa, składająca się w dwóch trzecich z biomasy, zapewnia bardzo dobre właściwości izolacyjne oraz zdrowy klimat dla mieszkańców.
Ekologiczna termoizolacja dachowa, składająca się w dwóch trzecich z biomasy, zapewnia bardzo dobre właściwości izolacyjne oraz zdrowy klimat dla mieszkańców.
Czytaj całość »W artykule przedstawiono i omówiono wyniki badań wybranych podkładów podłogowych i betonów wykonanych z cementów niskoemisyjnych, zawierających w swoim składzie popiół lotny krzemionkowy, granulowany żużel wielkopiecowy oraz wapień. Badania wykazały, że cementy niskoemisyjne mogą być stosowane do produkcji takich wyrobów w miejsce dotychczas stosowanego cementu CEM I bez dodatków.
Low-emission cements in dry mixtures of construction chemicals. Part 5: Types of floor screed and concrete
In the article the results of tests of selected types of floor screed and concrete made of low-carbon cements, containing silica fly ash, granulated blast furnace slag and limestone were presented and discussed. The research has shown that low-carbon cements can be used for the production of such materials in place of the previously used CEM I cement without additives.
***
Przemysł cementowy odpowiada za ok. 2,8% emisji CO2 w kraju [ 1 ], a mimo to jest jednym z liderów proekologicznych działań, mających na celu dążenie do neutralności klimatycznej, w ramach strategii „Fit for 55” [ 2 ]. Jednym z kierunków tych działań jest dążenie do stosowania na szeroką skalę cementów niskoklinkierowych. Cementy takie można z powodzeniem wykorzystać do produkcji suchych mieszanek chemii budowlanej, takich jak np. podkłady podłogowe i betony.
Branża cementowa podejmuje od lat szereg działań w myśl szeroko rozumianego pojęcia zrównoważonego rozwoju, których celem jest znaczące obniżenie emisji CO2 oraz minimalizacja wpływu na środowisko. W ramach głównych działań prowadzone są prace mające na celu m.in. [ 1 ]:
- poprawę efektywności energetycznej procesu,
- wychwytywanie i ponowne wykorzystanie CO2,
- opracowanie innowacyjnych rodzajów cementów,
- większe zastosowanie cementów niskoemisyjnych, czyli cementów z niższą zawartością klinkieru.
Według założeń strategii 5C [ 2 ], czyli strategii redukcji śladu węglowego w łańcuchu wartości obejmującej klinkier, cement, beton, konstrukcję i rekarabonatyzację, tylko z optymalizacji procesu produkcji klinkieru i zastosowania cementów niskoklinkierowych ma pochodzić aż 40% redukcji śladu węglowego.
Możliwości wykorzystania cementów niskoemisyjnych do produkcji suchych mieszanek chemii budowlanej, takich jak podkłady podłogowe i betony, są bardzo duże. Ten potencjał jak dotychczas nie był w pełni wykorzystany, ze względu na wciąż liczne i silne przyzwyczajenia rynkowe do produktów czystoklinkierowych.
Możliwości wykorzystania cementów niskoemisyjnych, zawierających nieklinkierowe składniki główne, takie jak popioły lotne, granulowany żużel wielkopiecowy czy wapień do produkcji suchych mieszanek potwierdzają wieloletnie pozytywne doświadczenia ze stosowania takich cementów workowanych do wykonywania popularnych w kraju podkładów podłogowych (tzw. wylewek) z miksokreta, stanowiących istotny element każdej podłogi.
W budownictwie mieszkaniowym prawidłowo wykonana podłoga powinna wykazywać nie tylko walory estetyczne, lecz przede wszystkim umożliwiać bezpieczną jej eksploatację. Jest to możliwe w przypadku prawidłowego zaprojektowania poszczególnych warstw podłogi, zastosowania odpowiednich materiałów oraz prawidłowego wykonawstwa. Podłoga powinna spełniać odpowiednie wymagania dotyczące izolacyjności termicznej, akustycznej i przeciwwilgociowej, a w przypadku podłóg pracujących na zewnątrz – także odporności na działanie wody i mrozu. Takie właściwości podłogi uzyskuje się wyłącznie przy prawidłowym zaprojektowaniu i wykonaniu wszystkich jej elementów, wśród których podkład podłogowy pełni istotną rolę. Wydawać się może, że podkłady podłogowe są z punktu widzenia całej konstrukcji budynku nie tak istotne jak elementy konstrukcyjne, zapewniające nośność całego budynku oraz stosunkowo łatwe do wykonania. Nic bardziej mylnego, niewłaściwie wykonane lub wykonane z niewłaściwych materiałów mogą powodować szereg problemów eksploatacyjnych, których eliminacja bywa bardzo kosztowna.
Nie jest powszechnie dostępna wiedza o właściwościach rozwiązań materiałowych opartych na cementach innych niż cementy z grupy CEM I, a przecież składniki nieklinkierowe zapewniają szereg ważnych cech z punktu widzenia układania i eksploatacji podkładu podłogowego m.in.:
- lepszą urabialność i homogenizację mieszanki,
- lepszą więźliwość wody,
- dłuższy czas urabialności,
- niższy skurcz – minimalizacja ryzyka powstawania rys,
- większą trwałość w środowisku agresji chemicznej.
Niniejszy artykuł stanowi kontynuację cyklu artykułów, rozpoczętych publikacją [ 3 ], w których podjęto dyskusję, opartą na wynikach badań laboratoryjnych i poligonowych (na budowach), dotyczącą możliwości wykorzystania „zielonych” cementów w suchych zaprawach.
Podkłady podłogowe cementowe i suche betony – rodzaje i właściwości normowe
Podłoga, czyli konstrukcja przenosząca różnego rodzaju obciążenia (równomiernie rozłożone i skupione), jest płaska i przystosowana do tego, aby mógł po niej odbywać się ruch pieszy lub kołowy. Podłoga zapewnia ponadto izolację termiczną, akustyczną i przeciwwilgociową podłoża. Z konstrukcyjnego punktu widzenia podłoga może składać się z czterech (lub mniej) warstw:
- warstwa I: posadzka,
- warstwa II: warstwa wyrównująca, warstwa podkładowa,
- warstwa III: izolacja termiczna, izolacja przeciwwilgociowa,
- warstwa IV: strop lub podłoże gruntowe lub betonowe.
Będący przedmiotem artykułu cementowy podkład podłogowy to warstwa (lub warstwy) podłogi układana bezpośrednio pod posadzką. Podkład podłogowy może być wykonany bezpośrednio na podłożu (związany z nim lub niezwiązany siłami przyczepności) lub też ułożony na warstwach pośrednich lub izolujących.
Podkłady podłogowe układane są zazwyczaj w warstwie o grubości co najmniej 20 mm. Ich zadaniem jest przede wszystkim stworzenie odpowiednich warunków do mocowania posadzki oraz przeniesienie różnego rodzaju obciążeń działających na posadzkę. W przypadku balkonów i tarasów podkład podłogowy ma również za zadanie nadanie odpowiedniego spadku podłogi [ 4 ].
Podkłady podłogowe w praktyce wykonywane są albo z gotowych suchych mieszanek (podkładów podłogowych czy betonów), albo bezpośrednio na budowie z uprzednio przygotowanych składników – najczęściej przy pomocy tzw. miksokreta.
Specjalnym rodzajem materiału na podkład podłogowy jest zaprawa wyrównawcza, która oprócz niektórych funkcji podkładu (profilowanie spadków, wykonywanie warstw dociskowych) stosowana jest również do wyrównywania i drobnych napraw podłoży pod wszelkiego rodzaju okładziny ceramiczne.
Zaprawy wyrównujące stosowane są również często do uzupełniania drobnych ubytków i nierówności w konstrukcjach betonowych, żelbetowych, murowych i w tynkach mineralnych. Zaprawa wyrównawcza stosowana jest często do naprawy podłoży betonowych i podkładów cementowych przed wylaniem masy samopoziomującej.
Trudno jest dokonać jednoznacznej systematyki podkładów podłogowych i mas wyrównujących. Na rynku krajowym oferowany jest bowiem bardzo szeroki asortyment tych wyrobów, uwzględniający:
- miejsce użytkowania (wewnątrz, na zewnątrz pomieszczeń),
- funkcję produktu (podkład podłogowy, masa wyrównująca),
- rodzaj spoiwa (cementowe, na bazie siarczanu wapnia (anhydrytowe i gipsowe), z żywic syntetycznych (np. epoksydowe), magnezjowe czy asfaltowe),
- warunki użytkowania: standardowe (wewnątrz i na zewnątrz pomieszczeń mieszkalnych i lokali użytkowych) i specjalne (np. posadzki przemysłowe),
- sposób wiązania i twardnienia (normalnie i szybkotwardniejące),
- grubość układanej warstwy: standardowe (średnio/grubowarstwowe) nanoszone zazwyczaj w warstwie o grubości od 20 mm i cienkowarstwowe nanoszone zazwyczaj w warstwie o grubości do 20 mm,
- sposób układania: ręczne i maszynowe (aplikowane na podłoże maszynowo za pomocą różnego rodzaju agregatów do posadzek i wylewek).
W kraju od wielu lat bardzo dużą popularnością cieszą się suche mieszanki „betonowe”, których maksymalne uziarnienie waha się w dość szerokich granicach, od 2 mm (są tzw. wylewki betonowe, czyli de facto podkłady podłogowe) aż po 8 mm. Jest to górna granica uziarnienia tzw. suchych betonów, podyktowana względami technologicznymi i ograniczeniami w produkcji takich wyrobów. Produkty te, oprócz zastosowania do wykonywania podkładów podłogowych, przeznaczone są do prostych prac betonowych.
Podkłady podłogowe i masy wyrównawcze ujęte zostały w normie PN-EN 13813 [ 5 ] podającej klasyfikację, wymagania oraz metody badań materiałów na podkłady podłogowe. To najbardziej „popularna” norma stosowana przez producentów, ale ma swoje ograniczenia w stosowaniu. Norma ta nie obejmuje tzw. podkładów podłogowych nośnych, tj. takich, których nośność jest uwzględniana przy wyznaczaniu konstrukcji, ponadto obejmuje wyroby przeznaczone do stosowania wyłącznie wewnątrz obiektów budowlanych.
Ograniczenia te sprawiają, że producenci wyrobów stosowanych na zewnętrz deklarują zgodność swoich wyrobów w następujący sposób:
- powołując się na normę PN-EN 1504-3 [6] dotyczącą wyrobów do napraw betonu,
- powołując się na normę PN-EN 13813 [5] dotyczącą wewnętrznych podkładów podłogowych oraz dodatkowo na normę PN-EN 998-2 [7] dla zapraw murarskich (z uwagi na fakt, że suche podkłady i betony mogą być stosowane do murowania z bloczków betonowych).
Tematykę zapraw murarskich i wymagań normowych opisano we wcześniejszej publikacji [ 8 ]. W niniejszej omówiono wymagania stawiane wyrobom w normach PN-EN 13813 oraz PN-EN 1504-3.
W normie PN-EN 13813 podano wymagania i metody badań dotyczące właściwości:
- mieszanek po zarobieniu wodą, takie jak:
- czas wiązania,
- konsystencja,
- wartość pH,
- stwardniałych materiałów, takie jak:
- wytrzymałość na ściskanie,
- wytrzymałość na zginanie,
- odporność na ścieranie,
- twardość powierzchni,
- twardość podkładów asfaltowych,
- wytrzymałość na nacisk koła,
- skurcz i pęcznienie,
- moduł sprężystości,
- przyczepność,
- odporność na uderzenia,
- reakcja na ogień,
- właściwości akustyczne,
- opór cieplny i odporność chemiczna.
Wykaz właściwości normowych materiałów na podkłady cementowe podano w TABELI 1.
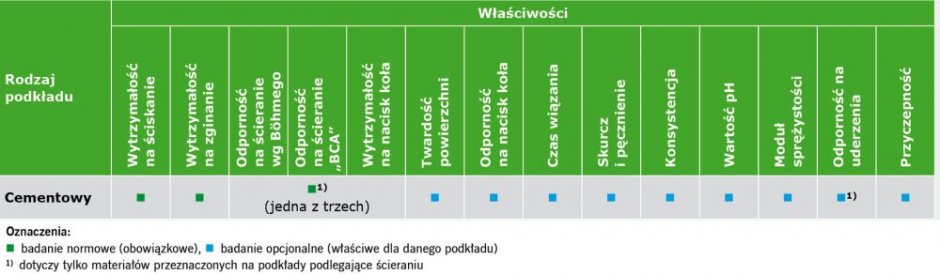
TABELA 1. Wykaz badań materiałów na bazie cementu przeznaczonych do wykonywania podkładów podłogowych
Z TABELI 1 wynika, że parametry wytrzymałościowe stanowią podstawę klasyfikacji większości podkładów. W normie przewidziano następujące klasy wytrzymałości na ściskanie i zginanie ( TABELE 2–3 ).
Ważną cechą niektórych podkładów podłogowych jest odporność na ścieranie. Właściwość ta, określona jedną z trzech metod (na tarczy Böhmego, metodą BCA lub też w postaci wytrzymałości na nacisk koła), jest znakowana odpowiednio: A (A1,5, A3, A6, A9, A12, A15, A22), AR (AR0,5, AR1, AR2, AR4, AR6) lub RWA (RWA1, RWA10, RWA20, RWA100, RWA 300).
Producent może również, lecz nie musi, zadeklarować szereg innych parametrów, np.:
- odporność na nacisk koła – RWFC (RWFC 150, 250, 350, 450, 550),
- moduł sprężystości – E (E1, E2, E5, E10, E15, E20 i wyższe z wielokrotnością [kN/mm2]),
- przyczepność – B (B0,2; B0,5; B1,0; B1,5 i B2,0),
- wartości pH (dla produktów na bazie siarczanu wapnia – pH ≥ 7),
- a także innych parametrów, dla których klas/wartości nie podano czasu wiązania, skurczu i pęcznienia i konsystencji.
Ponadto materiały na podkłady podłogowe mogą wykazywać szereg innych właściwości szczególnych, które producent może deklarować nawet wówczas, gdy przepisy tego nie wymagają. Są to np.:
- reakcja na ogień,
- oporność elektryczna,
- odporność chemiczna,
- przepuszczalność pary wodnej,
- opór cieplny,
- przepuszczalność wody,
- izolacyjność od dźwięków uderzeniowych,
- pochłanianie dźwięków.
Jak wspomniano wcześniej, norma EN 13813 ma swoje ograniczenia w stosowaniu. Ma to znaczenie w przypadku wszystkich podkładów zewnętrznych i suchych mieszanek betonowych o szerokim zastosowaniu, wykraczającym poza ramy wytyczone przez normę na podkłady. Dlatego też producenci częstokroć powołują się na normę dotyczącą napraw betonu PN-EN 1504-3.
W normie tej określono wymagania dotyczące cech identyfikacyjnych, właściwości użytkowych, w tym trwałości (mrozoodporności) wyrobów i systemów przeznaczonych do konstrukcyjnych i niekonstrukcyjnych napraw betonu.
Wymaganiami objęto „zaprawy i betony do napraw, możliwe do stosowania z innymi wyrobami i systemami w celu odbudowy i/lub zastąpienia uszkodzonego betonu oraz ochrony zbrojenia, co jest konieczne w celu przedłużenia czasu użytkowania konstrukcji betonowej wykazującej uszkodzenia”.
Wymienione wyroby mogą być stosowane do: odbudowy elementu betonowego, wzmocnienia konstrukcji lub też do utrzymania bądź przywrócenia stanu pasywnego betonu zbrojonego. Wyjątek stanowią materiały przeznaczone do naprawy nawierzchni betonowych na lotniskach, które powinny uzyskać aprobatę techniczną IBDiM oraz orzeczenie o przydatności do stosowania do nawierzchni lotniskowych, wydane przez Instytut Techniczny Wojsk Lotniczych.
Wymagania normy PN-EN 1504-3 dla wyrobów do napraw zestawiono w TABELI 4.
Analizując wymagania podane w TABELI 4, warto zwrócić uwagę na stosunkowo wysokie wymaganie dotyczące przyczepności zaprawy/betonu naprawczego. Wynika ono z konieczności bardzo dobrej kohezji i współpracy betonu naprawianego i zaprawy/betonu naprawczego. Aby je spełnić, niezbędne może być zastosowanie w recepturze specjalnych dodatków poprawiających przyczepność, jak na przykład proszku redyspergowalnego, stosowanego przykładowo w recepturach klejów do płytek czy do ociepleń. Typowe suche betony nie zawierają zazwyczaj tego dodatku, mogą zatem nie spełniać wymagań tej normy.
Badania suchych mieszanek przygotowanych „fabrycznie”
Na potrzeby projektu badawczego opracowano w laboratorium specjalne kompozycje kilku produktów:
- podkładu podłogowego klasy CT-C12-F3,
- podkładu podłogowego klasy CT-C20-F4,
- posadzki wyrównującej klasy CT-C20-F4,
- betonu B20 klasy CT-20-F4,
- betonu B30 „szybkiego” klasy CT-C30-F6.
Zaprawy przygotowano z zastosowaniem zamiennie różnego rodzaju cementów. Produktami referencyjnymi były zaprawy wykonane na cementach portlandzkich dwóch klas wytrzymałości:
- CEM I 52,5R,
- CEM I 42,5R.
Natomiast zaprawami, których właściwości sprawdzono, dodatkowo były zaprawy wykonane przy użyciu niskoemisyjnych cementów niskoklinkierowych:
- portlandzkiego popiołowego: CEM II/A-V 52,5R-NA,
- portlandzkiego wapiennego: CEM II/A-LL 42,5R-NA.
Taki wybór cementów miał na celu zarówno sprawdzenie wpływu nieklinkierowych składników głównych (popiół, kamień wapienny) na uzyskiwane właściwości zapraw, jak i porównanie parametrów uzyskiwanych przy dwóch klasach wytrzymałości cementów. Należy zaznaczyć, że porównywano zaprawy skomponowane z różnych cementów, ale przy zachowaniu tej samej ilości cementu w zaprawie.
Szczegóły dotyczące właściwości i wpływu poszczególnych nieklinkierowych składników głównych na właściwości cementów opisano we wcześniejszej publikacji autorów [ 9 ].
Zaprawy przygotowano na bazie standardowych receptur, z wykorzystaniem dostępnych na rynku składników, z zastosowaniem typowych dodatków modyfikujących właściwości zapraw. Badania zapraw z różnych cementów polegały na ocenie konsystencji i właściwości roboczych zapraw oraz wytrzymałości normowych. Wodożądność zapraw dobrano z uwzględnieniem rozpływu na stoliku potrząsalnym 14 ± 1 cm, pozwalającego na uzyskanie zapraw i betonów o optymalnej konsystencji. Wyniki badań zestawiono w TABELACH 5–6.
Z przeprowadzonych badań wynika, że zaprawy wykonane z cementów niskoklinkierowych CEM II wykazywały generalnie porównywalne parametry wytrzymałościowe w porównaniu do wytrzymałości zapraw z cementów CEM I.
Z uwagi na dodatki popiołu/wapienia, zaprawy z cementów CEM II wykazują natomiast w niektórych przypadkach lepsze właściwości robocze. Zastosowanie w recepturach zapraw cementów niskoklinkierowych może zatem pozwolić na modyfikację polegającą na zmniejszeniu lub wręcz wyeliminowaniu ilości drogich dodatków/domieszek, szczególnie tych mających na celu poprawę właściwości reologicznych.
Polowe testy posadzek wykonywanych z wykorzystaniem agregatu (miksokret)
Drugą część programu badawczego przeprowadzono w postaci testów wykonywania i układania podkładów podłogowych na budowach za pomocą popularnego w kraju urządzenia – agregatu do maszynowego wykonywania posadzek (miksokreta). Maszyna jest wyposażona w sprężarkę i wąż zakończony podajnikiem. Mieszanka wytworzona w agregacie ma konsystencję wilgotną otrzymywaną poprzez dozowanie odpowiedniej ilości wody zarobowej. Następnie, z urządzenia, wężem podawana jest na podłoże. Wykonawcy rozgarniają ją, wyrównują i zagęszczają przez zacieranie, tak żeby powstał równy i gładki podkład podłogowy.
Dla poprawy właściwości świeżej mieszanki i stwardniałego podkładu stosuje się często oprócz typowego piasku, dodatkowo do 30% żwiru o uziarnieniu do 8 mm, dodatki włókien i domieszki chemiczne (głównie plastyfikatory). Badane podkłady wykonywane były z uprzednio przygotowanych pojedynczych składników: kruszywa, cementu workowanego i ewentualnych dodatków.
Przedmiotem testów były podkłady wykonywane z różnych cementów:
- CEM I 42,5R – jako cement referencyjny,
oraz porównawczo cementy niskoklinkierowe:
- portlandzki wapienny: CEM II/A-LL 42,5R-NA – zawierający kamień wapienny,
- portlandzki popiołowy: CEM II/B-V 32,5R – zawierający popiół lotny krzemionkowy,
- portlandzki wieloskładnikowy: CEM II/B-M (S-V) 42,5R – zawierający popiół lotny krzemionkowy i żużel wielkopiecowy,
- portlandzki wieloskładnikowy: CEM II/C-M (W-LL) 32,5R – zawierający kamień wapienny oraz popiół lotny wapienny.
Taki wybór cementów miał na celu sprawdzenie wpływu nieklinkierowych składników głównych (popioły, żużel, kamień wapienny), czyli rodzaju cementu, na wykonywanie podkładów podłogowych w technologii miksokret.
W procesie wykonywania podkładu podłogowego oceniane były przez wykonawcę następujące parametry, kluczowe z punktu widzenia łatwości aplikacji mieszanki i końcowej jakości podkładu w następujących kryteriach oceny ( TABELA 7 ).
Próby polowe mieszanek wykonano przy założeniu stałej ilości stosowanego cementu (1,5 worka na pełny zarób) oraz przy założeniu, że woda jest dozowana do konsystencji jak w zarobie referencyjnym na cemencie CEM I.
Ocenę mieszanek z realizacji polowych w odniesieniu do mieszanki wzorcowej, wykonanej z cementu CEM I 42,5R zaprezentowano w TABELI 8.
Z przeprowadzonych testów polowych oraz doświadczeń własnych autorów można przyjąć, że praktycznie z każdego rodzaju cementu można opracować dobrej jakości mieszankę do wykonania podkładu z miksokreta. Na uwagę w ocenach wykonawców zasługuje punkt dotyczący wyglądu mieszanki, który przy zastosowaniu cementów z nieklinkierowymi składnikami głównymi był inny niż referencyjnej mieszanki, co wzbudzało pewną nieufność co do prawidłowości rozwiązania.
Inna ocena wizualna mieszanki była związana przede wszystkim ze sposobem homogenizacji i spójności składników w mieszankach z cementami niskoklinkierowymi. Co najciekawsze po dodaniu plastyfikatora i związaną z tym dodatkiem redukcją wody zarobowej, wszystkie oceniane parametry mieszanki uzyskiwały najwyższą ocenę Wykonawcy.
W tym miejscu należy także wspomnieć, że wbrew pozorom wykonywanie podkładów podłogowych czy też posadzek w technologii miksokreta, nie jest łatwe i wymaga od wykonawców posiadania niezbędnego doświadczenia i wiedzy.
Wnioski
- Niskoemisyjne cementy CEM II: popiołowe, popiołowo-żużlowe i wapienne mogą, a nawet powinny być stosowane w szerokim zakresie do produkcji suchych mieszanek podkładów podłogowych i betonów.
- Podkłady i betony wykonane z niskoemisyjnych cementów CEM II wykazują porównywalne lub nawet lepsze właściwości robocze i aplikacyjne w porównaniu do zapraw wykonanych z cementu CEM I bez dodatków.
- Wyniki badań wytrzymałościowych podkładów i betonów przygotowanych z zastosowaniem cementów niskoemisyjnych CEM II są podobne do wyników uzyskanych dla zapraw z cementów CEM I tych samych klas wytrzymałościowych.
- Zastosowanie niskoemisyjnych cementów CEM II w recepturach zapraw może, w zależności od rodzaju cementu, wiązać się z pewnymi zmianami receptur tych produktów. Niektóre z takich modyfikacji, biorąc pod uwagę pozytywne oddziaływanie nieklinkierowych składników cementu, mogą być korzystne kosztowo dla producenta.
- Producenci zapraw, którzy chętnie poszukują nowych niskoemisyjnych rozwiązań cementowych do swoich produktów w przeszłości stanowili awangardę, jednak obecnie dostrzegają, oprócz aspektów ekologicznych, pozytywne zmiany związane z właściwościami technologicznymi swoich produktów. W dobie „zielonych” zmian w całym sektorze budownictwa już dziś mogą się pochwalić sukcesami oraz reklamować swoje produkty jako niskoemisyjne.
Generalna konkluzja autorów po przeprowadzeniu programu badawczego jest następująca: właściwości suchych mieszanek podkładów podłogowych i betonów oraz posadzek wykonywanych na budowie za pomocą tzw. miksokreta można modelować za pomocą zastosowanego cementu. Czas uniwersalnych rozwiązań opartych na cementach portlandzkich CEM I jest czasem przeszłym, a przyszłość i trwałość rozwiązań zależy od właściwie użytych cementów niskoemisyjnych zapewniających elastyczność w doborze do przeznaczenia.
Przeprowadzone testy pozwoliły także na sformułowanie dodatkowych wniosków dotyczących samego procesu i technologii wykonywania tego typu podkładów, które mogą być przydatne do stworzenia w przyszłości ewentualnych wytycznych wykonawczych:
- stosowany w mieszankach z przeznaczeniem do wykonywania podkładów podłogowych piasek powinien być piaskiem czystym, najlepiej bez wtrąceń ilastych lub gliniastych,
- w przypadku stosowania piasków drobnych (pozostałość na sicie 0,250 mm powyżej 25%) należy stosować doziarnienie żwirem 2–8 mm lub użyć domieszki plastyfikującej, mającej za zadanie zredukować zapotrzebowanie na wodę mieszanki,
- rozpoczynając inwestycję na nowych materiałach, warto wykonać próby technologiczne wraz z przeprowadzeniem badań mieszanki w celu określenia dozowania wody do suchej mieszanki w miksokrecie oraz poboru próbek do oceny stwardniałego materiału.
Rozwój i wdrażanie technologii materiałów budowlanych CEMEX jest częścią globalnego networku ds. badań i rozwoju, na czele z Centrum Badań CEMEX z siedzibą w Szwajcarii.
Prawa autorskie dotyczące badań:
© 2022/CEMEX Innovation Holding Ltd. Szwajcaria.
Literatura
1. J. Deja, „Rozwój technologii cementu i betonu w kierunku obniżenia śladu węglowego”, prezentacja na seminarium „Droga do neutralności klimatycznej”, Warszawa, 21.09.2022.
2. Global Status Report for Buildings and Construction, 2020, https://architecture2030.org/newbuildings-embodied
3. P. Górak, S. Chłądzyński, K. Walusiak, „Cementy niskoemisyjne w suchych mieszankach chemii budowlanej – zielony kierunek rozwoju”, „IZOLACJE” 5/2022, s. 104–109.
4. S. Chłądzyński, R. Skrzypczyński, „Podkłady podłogowe. Część 1 – Rodzaje i właściwości”, „IZOLACJE” 11/12/2011, s. 42–47.
5. PN-EN 13813:2003, „Podkłady podłogowe oraz materiały do ich wykonania. Materiały. Właściwości i wymagania”.
6. PN-EN 1504-3:2006, „Wyroby i systemy do ochrony i napraw konstrukcji betonowych. Definicje, wymagania, sterowanie jakością i ocena zgodności. Część 3: Naprawy konstrukcyjne i niekonstrukcyjne”.
7. PN-EN 998-2:2016-12, „Wymagania dotyczące zaprawy do murów. Część 2: Zaprawa do murowania”.
8. P. Górak, S. Chłądzyński, J. Gaudy, „Cementy niskoemisyjne w suchych mieszankach chemii budowlanej. Część 4. Zaprawy murarskie i tynkarskie”, „IZOLACJE” 10/2022, s. 36–41.
9. P. Górak, S. Chłądzyński, K. Walusiak, „Cementy niskoemisyjne w suchych mieszankach chemii budowlanej. Część 2. Zaprawy klejowe do dociepleń”, „IZOLACJE” 7/8/2022, s. 74–79.
10. PN-EN 1015-3:2000, „Metody badań zapraw do murów. Określenie konsystencji świeżej zaprawy (za pomocą stolika rozpływu)”.
11. PN-EN 13892-2:2004, „Metody badania materiałów na podkłady podłogowe. Część 2: Oznaczenie wytrzymałości na zginanie i ściskanie.”