Fibrobeton – kompozyt cementowy do zadań specjalnych
Fibre concrete – cement composite for special tasks
![Koncepcja projektowa CUBE autorstwa HENN architects, rys.: [7]](https://www.izolacje.com.pl/media/cache/typical_view/data/202308/koncepcja-projektowa-cube-fibrobeton.jpg)
Koncepcja projektowa CUBE autorstwa HENN architects, rys.: [7]
Beton jest najczęściej używanym materiałem budowlanym na świecie i jest stosowany w prawie każdym typie konstrukcji. Beton jest niezbędnym materiałem budowlanym ze względu na swoją trwałość, wytrzymałość i wyjątkową długowieczność. Może wytrzymać naprężenia ściskające i rozciągające oraz trudne warunki pogodowe bez uszczerbku dla stabilności architektonicznej. Wytrzymałość betonu na ściskanie w połączeniu z wytrzymałością materiału wzmacniającego na rozciąganie poprawia ogólną jego trwałość. Beton zbrojony włóknami jest jednym z rodzajów betonu zbrojonego.
Zobacz także
mgr inż. Julia Blazy, prof. dr hab. inż. Łukasz Drobiec, dr hab. inż. arch. Rafał Blazy prof. PK Zastosowanie fibrobetonu z włóknami polipropylenowymi w przestrzeniach publicznych

Beton to materiał o dużej wytrzymałości na ściskanie, ale około dziesięciokrotnie mniejszej wytrzymałości na rozciąganie. Ponadto charakteryzuje się kruchym pękaniem i nie pozwala na przenoszenie naprężeń...
Beton to materiał o dużej wytrzymałości na ściskanie, ale około dziesięciokrotnie mniejszej wytrzymałości na rozciąganie. Ponadto charakteryzuje się kruchym pękaniem i nie pozwala na przenoszenie naprężeń po zarysowaniu.
prof. dr hab. eur. inż. Tomasz Z. Błaszczyński, mgr inż. Marta Przybylska-Fałek Fibrobeton jako materiał konstrukcyjny
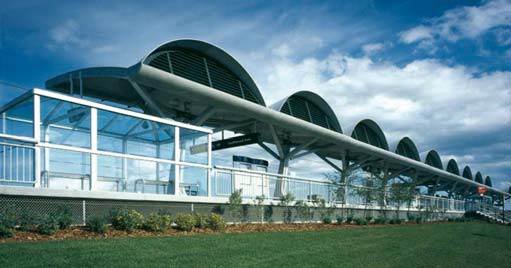
Fibrobeton jest coraz częściej stosowany w budownictwie – m.in. jako element konstrukcyjny. Aby w tym zastosowaniu pełnił swoją funkcję, musi zapewnić trwałość i nośność budowanej konstrukcji. Z tego powodu...
Fibrobeton jest coraz częściej stosowany w budownictwie – m.in. jako element konstrukcyjny. Aby w tym zastosowaniu pełnił swoją funkcję, musi zapewnić trwałość i nośność budowanej konstrukcji. Z tego powodu bardzo ważny jest przebieg procesu jego niszczenia pod obciążeniem ściskającym.
dr inż. Beata Anwajler, mgr inż. Anna Piwowar Bioniczny kompozyt komórkowy o właściwościach izolacyjnych
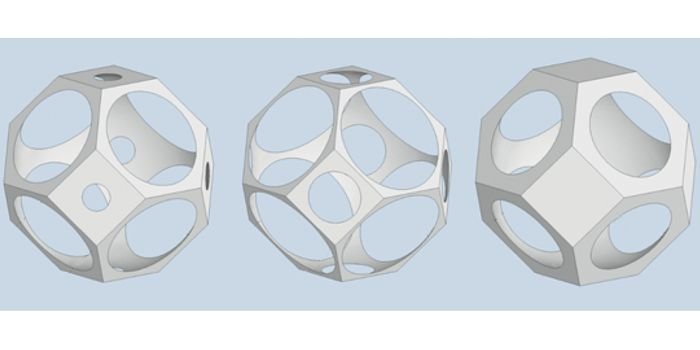
Współcześnie uwaga badaczy oraz polityków z całego świata została zwrócona na globalny problem negatywnego oddziaływania energetyki na środowisko naturalne. Szczególnym zagadnieniem stało się zjawisko...
Współcześnie uwaga badaczy oraz polityków z całego świata została zwrócona na globalny problem negatywnego oddziaływania energetyki na środowisko naturalne. Szczególnym zagadnieniem stało się zjawisko zwiększania efektu cieplarnianego, które jest wskazywane jako skutek działalności człowieka. Za nadrzędną przyczynę tego zjawiska uznaje się emisję gazów cieplarnianych (głównie dwutlenku węgla) związaną ze spalaniem paliw kopalnych oraz ubóstwem, które powoduje trudności w zaspakajaniu podstawowych...
W artykule omówiono specyfikę fibrobetonu. Przedstawiono różnego rodzaju włókna do zbrojenia betonu. Opisano jego właściwości, a także wpływ zbrojenia betonu na optymalizację kosztów inwestycji.
Fibre concrete – cement composite for special tasks
The article discusses the specificity of fibre concrete. Various types of fibres for concrete reinforcement are presented. Its properties as well as the impact of concrete reinforcement on the optimization of investment costs are described.
*****
Beton zbrojony włóknami Fiber Reinforced Concrete (FRC), inaczej fibrobeton, to beton wykonany głównie z cementów hydraulicznych, kruszyw i włókien wzmacniających. Włókna nadające się do zbrojenia betonu produkuje się ze stali, szkła i polimerów organicznych (włókna syntetyczne). Do wzmocnienia stosuje się również włókna roślinne takie jak sizal i juta. Betonowe podłoża mogą być zaprawami, mieszaninami o normalnych proporcjach lub mieszaninami specjalnie opracowanymi do określonego zastosowania. Jeśli FRC jest właściwie zaprojektowany, jedną z największych korzyści, jakie można uzyskać dzięki zastosowaniu zbrojenia włóknistego, jest poprawa długoterminowej użyteczności konstrukcji lub produktu.
Matryca na bazie cementu
FRC to matryca cementowa, wewnątrz której rozmieszczone są przypadkowe włókna w stosunku do wymiarów elementu. W przeciwieństwie do tradycyjnego zbrojenia prętami stalowymi, dodane krótkie włókna zwykle nie zwiększają wytrzymałości betonu na ściskanie, jednak dzięki ich jednorodnej dyfuzji skuteczniej poprawiają zachowanie się elementu betonowego po spękaniu. Ich celem jest zatem zwiększenie plastyczności i zdolności do pochłaniania energii, poprzez kontrolę propagacji pęknięć.
Główne składniki matrycy w FRC nie różnią się w porównaniu z tradycyjnymi materiałami cementowymi, którymi zazwyczaj są:
- cement portlandzki,
- woda,
- kruszywa różnej wielkości,
- dodatki.
Dobór jakości składników i ich proporcji w mieszance zależy od głównych wymagań co do stopnia wytrzymałości, urabialności w stanie świeżym, porowatości i trwałości.
Zasadniczo matryca składa się na ogół z betonu na bazie cementu portlandzkiego, gdy dodaje się niewielkie ilości włókien. W rzeczywistości głównym wyzwaniem technologicznym jest wprowadzenie dużych ilości rozproszonych włókien w matrycy, bez utraty wysokiej urabialności. Przy wyższych dawkach oraz w zależności od rodzaju i wymiarów włókien należy rozważyć odpowiednie dostosowanie konstrukcji mieszanki. Jest to możliwe dzięki dodaniu lub zwiększeniu dawki superplastyfikatorów oraz uwzględnieniu większej ilości drobnych kruszyw, aby zachować stały stosunek wodno-cementowy. W przypadku dodania dużych ilości włókien projekt mieszanki musi zostać zmodyfikowany, na przykład poprzez zwiększenie ilości drobnych kruszyw i dodatków, co może prowadzić do ścieżki betonu samozagęszczalnego (SCC).
SCC to beton samozagęszczalny bez konieczności wibrowania. Podczas odlewania wyeliminowana jest ewentualna segregacja, jak pokazano w TABELI 1. Ich struktura wewnętrzna jest zbudowana z dużej liczby drobnych kruszyw i stanowi mieszanki odpowiednie do przyjmowania większych dawek włókien.
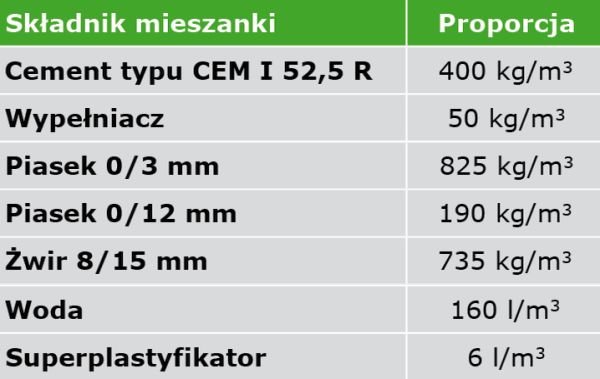
TABELA 2. Przykład projektu mieszanki SCCFRC zaprojektowanej z większą ilością drobnego kruszywa, które należy uznać za wypełniacz [1]
Rozpowszechnienie chemicznych dodatków upłynniających i nadfluidujących wprowadzono na początku lat 70. XX wieku, obecnie są one szeroko stosowane. Poprawiają właściwości w stanie świeżym bez pogarszania właściwości w stanie utwardzonym. W TABELI 2 zilustrowano efekty stosowania betonu SCC bez dodatków.
Najczęściej stosowanymi dodatkami są superplastyfikatory, które są w stanie zmniejszyć zapotrzebowanie na wodę przy równomiernym rozlewaniu i zwiększyć płynność przy takim samym stosunku woda/spoiwo. Niemniej jednak może to mieć wpływ na wczesną wytrzymałość konstrukcji betonowej. Czynnikami nadfluidującymi są rozpuszczalne w wodzie polimery, których głównym efektem jest deflokulacja, poprawiająca dyspersję cząstek stałych. Można rozważyć zastosowanie środków upłynniających w celu uniknięcia dwóch możliwych problemów: wysięku i segregacji betonu. Jeśli dodatek stosuje się w celu zmniejszenia zawartości wody bez zmiany mieszanki, konieczne będzie sprawdzenie, czy lepkość świeżego FRC nie staje się zbyt wysoka, powodując powolny przepływ [1].
Rodzaje włókien
Włókna do betonu są dostępne w różnych rozmiarach i kształtach. Głównymi czynnikami wpływającymi na właściwości betonu zbrojonego włóknami są stosunek wodno-cementowy, procentowa zawartość włókien, średnica i długość włókien.
Poniżej podano różne rodzaje betonu zbrojonego włóknami stosowane w budownictwie.
Beton zbrojony włóknem stalowym (SFRC)
Włókno stalowe jest metalowym wzmocnieniem. Pewna ilość włókien stalowych w betonie może powodować jakościowe zmiany właściwości fizycznych betonu. Może znacznie zwiększyć odporność na pękanie, uderzenia, zmęczenie i zginanie, wytrzymałość na rozciąganie i trwałość. Aby poprawić długoterminowe zachowanie, zwiększyć wytrzymałość, wytrzymałość i odporność na naprężenia, SFRC jest stosowany w konstrukcjach takich jak podłogi, obudowy, prefabrykaty, mosty, tunele, nawierzchnie o dużej wytrzymałości i górnictwo. Średnica włókien stalowych waha się od 0,25 do 0,75 mm. Włókna stalowe ściśle kontrolują szerokość rys i w ten sposób poprawiają trwałość betonu.
Beton zbrojony włóknami polipropylenowymi
Beton zbrojony włóknami polipropylenowymi jest również znany jako polipropylen lub PP. Jest to włókno syntetyczne, przetworzone z propylenu. Włókna te są zwykle stosowane w betonie do kontrolowania pęknięć spowodowanych skurczem plastycznym. Zmniejszają również przepuszczalność betonu, a tym samym ograniczają wyciekanie wody.
Włókno polipropylenowe należy do grupy poliolefin i jest częściowo krystaliczne i niespolaryzowane. Ma podobne właściwości jak polietylen, ale jest twardszy i bardziej odporny na ciepło. Jest to biały wytrzymały materiał o wysokiej odporności chemicznej. Polipropylen jest wytwarzany z gazu propylenowego w obecności katalizatora, takiego jak chlorek tytanu.
Włókno polipropylenowe wykazuje dobre właściwości termoizolacyjne i jest wysoko odporne na działanie kwasów, zasad i rozpuszczalników organicznych.
Beton zbrojony włóknem szklanym
Beton zbrojony włóknem szklanym to materiał składający się z wielu bardzo drobnych włókien szklanych. Włókno szklane ma z grubsza porównywalne właściwości mechaniczne z innymi włóknami, takimi jak polimery i włókno węglowe. Chociaż nie jest tak sztywne jak włókno węglowe, jest znacznie tańsze i znacznie mniej kruche, gdy jest stosowane w kompozytach. Włókna szklane są zatem stosowane jako środek wzmacniający w wielu produktach polimerowych; w celu utworzenia bardzo mocnego i stosunkowo lekkiego materiału kompozytowego z polimeru wzmocnionego włóknem (FRP), zwanego tworzywem sztucznym wzmocnionym włóknem szklanym (GRP), popularnie znanego również jako „włókno szklane”. Materiał ten zawiera niewiele powietrza lub gazu lub nie zawiera ich wcale, jest gęstszy i jest znacznie gorszym izolatorem termicznym niż wełna szklana. Włókna szklane mają wytrzymałość na rozciąganie od 1020 do 4080 N/mm2. Długość włókien stosowanych w tego typu włóknach wynosi na ogół 25 mm. Mają wysoką wytrzymałość na zginanie, są plastyczne, a także odporne na wysokie temperatury.
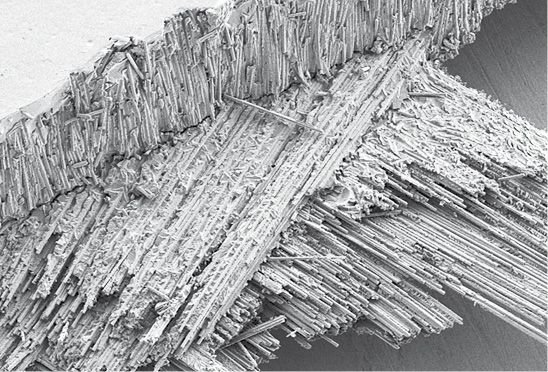
FOT. 4. Mikrografia pokazująca orientację włókien węglowych superkompozytu węglowego; fot.: Boston Materials
Beton zbrojony włóknami poliestrowymi
Włókna poliestrowe są stosowane w betonie przeznaczonym na posadzki przemysłowe i magazynowe, chodniki i nawierzchnie oraz wyroby prefabrykowane. Mikro- i makrowłókna poliestrowe wykorzystuje się w celu zapewnienia lepszej odporności na powstawanie pęknięć skurczowych plastycznych oraz w celu zwiększenia wytrzymałości.
Beton zbrojony włóknami węglowymi
Włókna węglowe mają średnicę ok. 5–10 μm i składają się głównie z atomów węgla. Mają wiele zalet, w tym wysoką sztywność, dużą wytrzymałość na rozciąganie, niską wagę, wysoką odporność chemiczną, tolerancję na wysoką temperaturę i niską rozszerzalność cieplną.
Włókna węglowe są zwykle łączone z innymi materiałami w celu utworzenia kompozytu. Po zaimpregnowaniu żywicą z tworzywa sztucznego i wypaleniu tworzą polimer wzmocniony włóknem węglowym (często nazywany włóknem węglowym), który ma bardzo wysoki stosunek wytrzymałości do masy i jest niezwykle sztywny, choć nieco kruchy.
Włókna węglowe są również łączone z innymi materiałami, takimi jak grafit, tworząc wzmocnione kompozyty węglowe, które mają bardzo wysoką tolerancję na ciepło.
Beton zbrojony włóknami makrosyntetycznymi
Włókna makrosyntetyczne są wykonane z mieszanki polimerów i zostały pierwotnie opracowane jako alternatywa dla włókien stalowych w betonie natryskowym, ale prace badawcze wykazały, że mają zastosowanie w projektowaniu i konstruowaniu płyt na gruncie oraz w wielu innych elementach konstrukcyjnych. Są niezbędne do zapewniania nominalnego zbrojenia w agresywnych środowiskach, takich jak konstrukcje morskie i przybrzeżne, ponieważ są odporne na problemy z plamami i odpryskami, które mogą wynikać z korozji stali. Poza tym, ponieważ nie przewodzą prądu elektrycznego, znalazły zastosowanie w zabudowie trakcyjnej.
Beton zbrojony włóknami mikrosyntetycznymi
W porównaniu ze spawanym drutem zbrojeniowym, włókna mikrosyntetyczne zapewniają lepszą odporność na powstawanie pęknięć skurczowych plastycznych, ale nie są w stanie zapewnić żadnej odporności na dalsze rozwarcia pęknięć spowodowane skurczem, obciążeniem konstrukcyjnym lub innymi formami naprężeń. Jednak produkty te powinny być stosowane w każdym typie betonu, aby poprawić odporność na pękanie, ochronę przed odpryskami, odporność na zamrażanie i rozmrażanie oraz poprawić jednorodność betonu podczas układania.
Beton zbrojony włóknami naturalnymi
Włókna naturalne są łatwo dostępne i można je stosunkowo szybko przekształcić we włókniny takie jak filc lub papier, lub po przędzeniu w przędzę lub tkaninę. Włókno naturalne można zdefiniować jako skupisko komórek, w którym średnica jest pomijalnie mała w porównaniu z długością. Naturalne materiały włókniste to głównie materiały celulozowe, takie jak bawełna, drewno, zboża i słoma. Stosowanie włókien naturalnych do produkcji fibrobetonu stało się popularne, ponieważ włókna te są dostępne lokalnie i występują w dużych ilościach. Pomysł wykorzystania takich włókien do poprawy wytrzymałości i trwałości kruchych materiałów nie jest nowy; na przykład słoma i włosie końskie były używane do wyrobu cegieł i gipsu już w starożytności.
Beton zbrojony włóknami celulozowymi
Włókna celulozowe są wytwarzane z eterów lub estrów celulozy, które można uzyskać z kory, drewna lub liści roślin lub innego materiału pochodzenia roślinnego. Oprócz celulozy włókna mogą zawierać również hemicelulozę i ligninę, przy czym różne zawartości procentowe tych składników zmieniają właściwości mechaniczne włókien.
Główne zastosowania włókien celulozowych to przemysł tekstylny – jako filtry chemiczne i kompozyty wzmacniające włókna, ze względu na ich podobne właściwości do włókien konstrukcyjnych, co stanowi kolejną opcję dla biokompozytów i kompozytów polimerowych.
Właściwości betonu zbrojonego włóknami
Zalety betonu zbrojonego włóknami to m.in.:
- redukcja grubości elementów betonowych,
- zwiększona trwałość,
- niskie koszty utrzymania – wydłużona żywotność,
- łatwiejsze pozycjonowanie połączeń (wymagana mniejsza liczba połączeń),
- zwiększona odporność na uderzenia, ścinanie i ścieranie,
- równomierne rozmieszczenie włókien w betonie (można określić wytrzymałość betonu na rozciąganie),
- trwalsza powierzchnia z mniejszą liczbą otworów spadowych (oczekiwana lepsza jakość betonu),
- redukcja kosztów i czasu realizacji projektu,
- zmniejszone wchłanianie wody i innych szkodliwych substancji chemicznych,
- zmniejszona przepuszczalność powierzchni i zwiększenie trwałości betonu,
- zmniejszone pełzanie i eliminacja naprężenia skurczowego,
- wzrost wytrzymałości zmęczeniowej, wytrzymałości na zginanie, udarności, nośności itp.,
- zapobieganie powstawaniu pęknięć w betonie,
- włókna są dystrybutorem zlokalizowanych naprężeń [3].
Do wad betonu zbrojonego włóknami zaliczamy:
- korozję na powierzchni betonu (w przypadku zbrojenia włóknami stalowymi),
- konieczność właściwej kontroli podczas przygotowywania mieszanki,
- konieczność zaprojektowania precyzyjnego składu,
- zwiększenie liczby włókien może zmniejszyć podatność na obróbkę i spowodować problemy z wykańczaniem [4, 5].
Beton zbrojony włóknami węglowymi a optymalizacja kosztów inwestycji
Światowa gospodarka przeżywa największy kryzys energetyczny od lat 70. ubiegłego wieku. Inflacja wzrosła do poziomów nienotowanych od wielu dziesięcioleci i obniża wzrost gospodarczy na całym świecie. Choć wzrost cen był już zauważalny przez pandemię i związane z nią ograniczenia w łańcuchu dostaw, to gwałtowny wzrost inflacji stał się znacznie bardziej odczuwalny na całym świecie po inwazji Rosji na Ukrainę. Kryzys odbija się na wszystkich sektorach gospodarki, w tym bardzo dotkliwie na budownictwie. Szukanie oszczędności staje się zatem priorytetem. Jednak budownictwo jest dziedziną, w której mniejsze nakłady finansowe nie mogą odbijać się na jakości materiałów.
Rozkład kosztów dla budynku mieszkalnego jednorodzinnego:
- konstrukcje i elementy budowlane – ok. 83–91% kosztu budowy, pozostała część to koszt instalacji – z najwyższym udziałem (17%) w przypadku domu energooszczędnego,
- największe pozycje kosztów to stan surowy (35–46%) oraz stan wykończeniowy wewnętrzny (22–28%),
- w strukturze ceny obiektu 47–62% to koszty materiałów (najwyższe przy domu energooszczędnym); 19–26% – koszty robocizny; wynajem sprzętu nie przekraczał 2,2%; koszty pośrednie: 14–19%; szacowany zysk wykonawcy: 3,6–5,2% [6].
Rozkład kosztów dla budynku mieszkalnego wielorodzinnego:
- konstrukcje i elementy budowlane stanowiły ok. 81–86% kosztu budynku, pozostałe to koszty instalacji – z najniższym udziałem (13%) w przypadku apartamentowca,
- największe pozycje kosztów to stan surowy (37–48%) oraz stan wykończeniowy wewnętrzny (12–22%),
- w strukturze ceny obiektu 53–63% to koszty materiałów; 13–22%: robocizna; wynajem sprzętu wynosił 4–7% (większy przy większych budynkach), koszty pośrednie: 14–17%; zysk wykonawcy szacowany na ok. 3,7–4,7% [6].
W obu przypadkach widać, że największe oszczędności są możliwe do uzyskania przy optymalizacji kosztów konstrukcji i elementach budowlanych. Wychodząc z tego założenia, powstał projekt CUBE.
CUBE to pierwszy na świecie budynek wykonany z betonu zbrojonego węglem. W całości reprezentuje skoncentrowaną wiedzę z połączonych częściowych wyników projektu C3 w jednym budynku. Tak więc sam CUBE jest wynikiem siedmioletniego projektu badawczego C3 Carbon Concrete Composite, który został skompilowany z ponad 300 podprojektów z ponad 120 partnerami badawczymi.
W ramach projektu badawczego rozpoczętego w 2017 r. dokonano przeglądu wyników C3 i przygotowano je do wykorzystania w projekcie CUBE m.in. za pomocą drzewa wyników. Na tej podstawie elementy struktury i konstrukcji można było następnie opracować z partnerami z dziedziny planowania i realizacji budynków (AIB GmbH, Assmann Ingenieure AG, Bendl HTS GmbH, Betonwerk Oschatz GmbH). Architekci HENN byli odpowiedzialni za koncepcję projektową i przedstawili projekt, który z jednej strony pokazuje techniczne, a z drugiej strony ekonomiczne możliwości, które są już wykonalne w przypadku betonu zbrojonego węglem.
Można nazwać trzy główne obszary: prefabrykowany sześcian BOX, dwie skręcone betonowe skorupy TWIST oraz szklaną elewację zamykającą obwiednię budynku. Planowanie rozpoczęło się w 2018 r., dzięki czemu można było uzyskać pozwolenie na budowę od miasta Drezno i aprobaty w indywidualnych przypadkach dla elementów z betonu zbrojonego węglem. Oprócz planowania, prace budowlane zostały ogłoszone w drodze przetargu publicznego i przyznane konsorcjum składającemu się z firm Hentschke Bau GmbH i Bendl HTS GmbH w wieloetapowym procesie selekcji. Nagrodę partii elementów prefabrykowanych i półprefabrykowanych otrzymała firma Betonwerk Oschatz GmbH ze względu na duże doświadczenie w produkcji prefabrykowanych i półprefabrykowanych elementów z betonu zbrojonego węglem. Inni partnerzy naukowi z C3 wsparli wdrożenie CUBE, dostarczając innowacyjne materiały i komponenty w obszarach zbrojenia, betonu i izolacji.
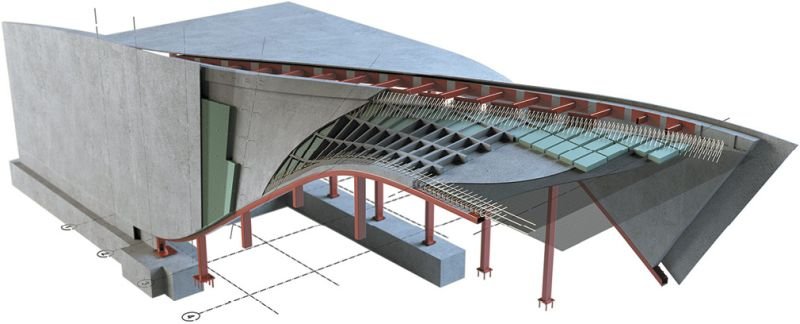
RYS. 6. Ilustracja konstrukcji powłok nośnych i odpornych na warunki atmosferyczne TWIST; rys.: TU Dresden, Vakaliuk [7]
Prace przygotowawcze rozpoczęto w 2020 r. od budowy wykopu. W 2021 r. rozpoczęto realizację samego CUBE wraz z prefabrykacją elementów ścian i stropów, równolegle wykonano fundamenty (fundamenty, płytę podstawy) budynku. Budynek będzie miał powierzchnię użytkową ok. 220 m2, ma 24 m długości i niecałe 7 m wysokości. Znajdą się w nim sale eventowe i laboratoryjne. W tym celu i w celu długoterminowego monitorowania naukowego zostanie on zintegrowany z infrastrukturą uniwersytecką Politechniki Drezdeńskiej [7].
TWIST to wielowarstwowa betonowa konstrukcja skorupowa, która reprezentuje ścianę, dach i wszystko pomiędzy. Jest on podzielony na dwie główne części, część skorupy nośnej i część powłoki pogodowej. Ponieważ konstrukcja oprócz konstrukcji nośnej powinna również spełniać wszystkie wymagania fizyki budowli. Powłoka nośna składa się z dolnej i górnej warstwy betonu o grubości 3 cm, każda z jedną warstwą zbrojenia węglowego, z pionowymi żebrami pomiędzy dwiema warstwami betonu. Niezbrojone żebra o szerokości 6 cm tworzą ortogonalną siatkę betonu o osiowym wymiarze 44 cm, powstałe wnęki są wypełnione materiałem izolacyjnym w celu ochrony termicznej.
Po bitumicznej warstwie uszczelniającej i całopowierzchniowej izolacji, na wierzchu układana jest powłoka chroniąca przed czynnikami atmosferycznymi. Składa się z cienkiej warstwy betonu o grubości 4 cm z dwiema warstwami zbrojenia węglowego. Powłoki nośne i odporne na warunki atmosferyczne są połączone ze sobą za pomocą prętów zbrojeniowych z włókna szklanego, które są regularnie rozmieszczone na przecięciach prostopadłej siatki środnika. Konstrukcja ma wysokość 44 cm, z czego 25 cm to konstrukcja nośna skorupy wraz z izolacją i hydroizolacją oraz 19 cm powłoka chroniąca przed czynnikami atmosferycznymi wraz z izolacją i hydroizolacją.
Dach TWIST składa się z dwóch przeciwległych powłok, które stykają się ze sobą w dwóch punktach, tworząc otwór w obszarze dachu zaprojektowany jako szklany pas światła dziennego w budynku. Dzięki weryfikacji inżynierów budownictwa i instytutów badawczych możliwe było uzyskanie aprobaty w indywidualnych przypadkach dla tej konstrukcji nośnej [7].
BOX ma ok. 7 m wysokości, dwukondygnacyjny fragment budynku CUBE o pow. 4,9×10,7 m z prefabrykowanych elementów ściennych i stropowych. BOX pełni rolę funkcjonalnego budynku komercyjnego, spełniającego wszelkie wymagania techniczne i budowlane. Dwie z czterech ścian są określone jako ściany zewnętrzne, a pozostałe dwie jako ściany wewnętrzne, przy czym konstrukcja, grubość ścian oraz metody produkcji i montażu są identyczne. Do elementów ściennych wykorzystano półfabrykaty betonowe, które można było wytwarzać półautomatycznie w wytwórni prefabrykatów betonowych z systemem cyrkulacyjnym.
W przeciwieństwie do TWIST, BOX ma betonową powłokę zewnętrzną w kolorze antracytu (5% pigmentu). Ustawowo wymagana izolacja termiczna oparta na rozporządzeniu w sprawie oszczędzania energii została wykonana przy użyciu wysokowydajnej izolacji z niepalnego aerożelu. Grubość ściany wynosi 27 cm przy grubości izolacji 7 cm. Skorupa zewnętrzna i wewnętrzna mają po 4 cm każda, a rdzeń betonowy in situ ma 12 cm, skorupy są połączone prętem zbrojeniowym z włókna szklanego.
Elementy stropowe to prefabrykowane elementy pełne, których konstrukcja jest bardzo zbliżona do powłoki nośnej TWIST. Dopuszczenie w indywidualnych przypadkach można było uzyskać również dla tych elementów BOX.
Potencjały oszczędności potwierdzone na podstawie prefabrykowanych części CUBE dla aktualnego stanu projektu i wykonalnego następnego etapu zostaną teraz odniesione do powiązanego segmentu rynku. Według Reference 30 żelbet, stosowany jako element prefabrykowany, okazał się dominującym materiałem do budowy ścian na elewacje w 2019 r., z 51 mln m2 budowanymi rocznie w Niemczech. Gdyby ten obszar został przekształcony w beton zbrojony węglem, można by zaoszczędzić 0,45 mln ton cementu (w oparciu o ścianę sześcienną); dzięki wyżej wymienionym optymalizacjom mającym na celu zmniejszenie zawartości cementu i grubości płyt, można było zaoszczędzić nawet 1,14 mln ton cementu [7].
Beton zbrojony włóknem węglowym jest przedmiotem badań na poziomie akademickim, ponieważ wydaje się być bardzo obiecującym materiałem budowlanym. Jest tani i trwały, dzięki czemu doskonale nadaje się do wzmacniania każdej konstrukcji betonowej. Ponieważ może również wzmocnić istniejące obiekty, jego wykorzystanie jest bardziej opłacalne niż wyburzanie całej konstrukcji. Nośność mostów i innych konstrukcji można zwiększyć, stosując włókna węglowe. Włókno węglowe ma również wysoką odporność na ciepło. Beton zbrojony włóknem węglowym może pracować pod ciśnieniem, ale jest również bardzo lekki; jego materiały kompozytowe składają się z drobnoziarnistego i superwytrzymałego betonu, a także innych włókien węglowych. Można by pomyśleć, że włókno stalowe ma większą wytrzymałość, ale włókno węglowe ma wyższą odporność niż włókna stalowe przy zaledwie 25% wagi. Włókna węglowe rozwiązują problem słabej elastyczności betonu, ponieważ wytrzymałość betonu na zginanie podwaja się po dodaniu włókna węglowego.
Badania laboratoryjne betonów zbrojonych włóknami wykazały, że całkowita energia pochłonięta przez włókno, mierzona polem powierzchni pod krzywą obciążenie-ugięcie, jest od 10 do 40 razy większa w przypadku betonu zbrojonego włóknami niż zwykłego betonu. Dodatek włókien do konwencjonalnie wzmacnianych belek zwiększał trwałość zmęczeniową i zmniejszał szerokość pęknięć pod obciążeniem zmęczeniowym. W podwyższonej temperaturze fibrobeton ma większą wytrzymałość zarówno na rozciąganie, jak i ściskanie. Oszczędność kosztów to ok. 10–30% w porównaniu z konwencjonalnym systemem betonowym.
Literatura
1. P. Samui, D. Kim, N. Iyer, S. Chaudhary, „New Materials in Civil Engineering”, Butterworth–Heinemann 2020.
2. M. Glinicki, „Beton ze zbrojeniem strukturalnym”, XXV Ogólnopolskie Warsztaty Pracy Projektanta Konstrukcji, Szczyrk 10–13 marca 2010.
3. M. Rodriguez, „What are the Advantages of using Steel Fibre Reinforced Concrete instead of traditional Rebar?”, „Structures Insider”, 9 marca 2022.
4. J. Śliwiński, „Beton zwykły – projektowanie i podstawowe właściwości”, „Polski Cement”, Kraków 1999.
5. Z. Jamroży, „Betony ze zbrojeniem rozproszonym (co projektant konstrukcji wiedzieć powinien)”, Materiały XVII Ogólnopolskiej Konferencji „Warsztaty Pracy Projektanta Konstrukcji” t. I, Ustroń 2002.
6. Raport PKO BP „Rynek Mieszkaniowy 3q22/Analizy Nieruchomości”.
7. M. Tietze, Z. Kirmse, A. Kahnta, F. Schladitza, M. Curbacha, „The ecological and economic advantages of carbon reinforced concrete. Using the C3 result house CUBE especially the BOX value chain as an example”, Civil Engineering Design, tom 4 , wyd. 1–3, czerwiec 2022.
8. PN-EN 14889-1:2007, „Włókna do betonu. Część 1: Włókna stalowe. Definicje, wymagania i zgodność”.
9. PN-EN 14889-2:2007, „Włókna do betonu. Część 2: Włókna polimerowe. Definicje, wymagania i zgodność”.
10. Z. Jamroży, „Beton i jego technologie”, Wydawnictwo Naukowe PWN, Warszawa–Kraków 2000.