Polimerowe środki ochronne do izolacji zbiorników
Polymer-based protective materials for container insulation
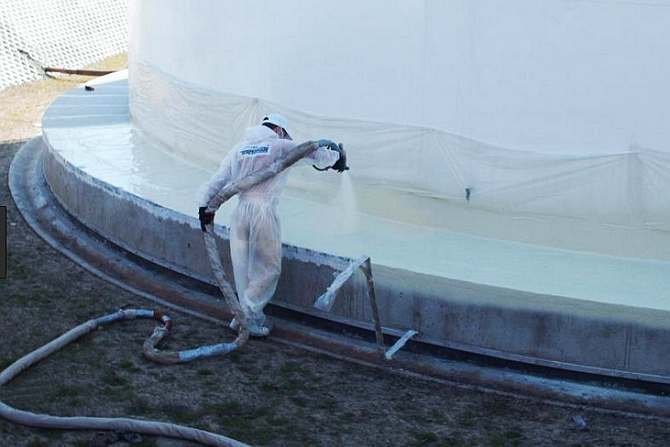
Nieodpowiednio dobrany zbiornik i brak prawidłowego kontrolowania jego szczelności może doprowadzić do katastrofy.
Termopian
Przy rozważaniu zakupu zbiornika do przechowywania substancji żrącej najważniejszym czynnikiem, który powinien być brany pod uwagę, jest materiał pokrywający zbiornik od wewnątrz.
Zobacz także
Sika Poland Nowe Centrum Hydroizolacji Sika na Pomorzu

Z przyjemnością informujemy o otwarciu nowego Centrum Hydroizolacji w firmie Broker – hurtownia materiałów budowlanych w Rokocinie.
Z przyjemnością informujemy o otwarciu nowego Centrum Hydroizolacji w firmie Broker – hurtownia materiałów budowlanych w Rokocinie.
Bostik Bostik AQUASTOPP – szybkie i efektywne rozwiązanie problemu wilgoci napierającej
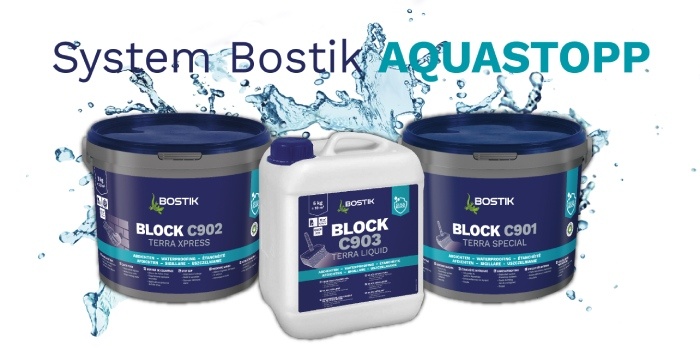
Bostik to firma z wieloletnią tradycją, sięgającą 1889 roku, oferująca szeroką gamę produktów chemii budowlanej dla profesjonalistów i majsterkowiczów. Producent słynie z innowacyjnych rozwiązań i wysokiej...
Bostik to firma z wieloletnią tradycją, sięgającą 1889 roku, oferująca szeroką gamę produktów chemii budowlanej dla profesjonalistów i majsterkowiczów. Producent słynie z innowacyjnych rozwiązań i wysokiej jakości preparatów, które znajdują zastosowanie w budownictwie, przemyśle i renowacji.
Alchimica Polska Sp. z o.o. Skuteczna naprawa betonu z zaprawą Hygrosmart®-Fix&Finish

Hygrosmart Fix&Finish to jednoskładnikowa, szybkowiążąca, zbrojona włóknami zaprawa cementowa typu PCC (beton polimerowo-cementowy nazywany również betonem żywicznym). Służy do napraw strukturalnych betonu...
Hygrosmart Fix&Finish to jednoskładnikowa, szybkowiążąca, zbrojona włóknami zaprawa cementowa typu PCC (beton polimerowo-cementowy nazywany również betonem żywicznym). Służy do napraw strukturalnych betonu i wyrównywania jego powierzchni.
ABSTRAKT |
---|
Artykuł omawia zagadnienia związane z izolacjami zbiorników o podwyższonych parametrach użytkowych, narażonych na wysoką temperaturę, silnie żrące substancje, transport o dużym ryzyku. Autorzy charakteryzują rynek środków izolacyjnych i przedstawiają różne typy żywic do izolowania wnętrza zbiorników. Omawiają metody pokrywania powierzchni warstwami izolacyjnymi z podaniem przykładów i ze szczególnym uwzględnieniem natryskiwania płomieniowego. |
Polymer-based protective materials for container insulationThe article discusses issues related to the insulation of improved-property containers susceptible to high temperatures, strongly corrosive substances, high-risk transport. The authors describe the market for insulation materials and present various types of resins used for insulating container interiors. They discuss methods of coating of surfaces with insulating layers with the indication of examples and with particular inclusion of flame spraying. |
Materiały konstrukcyjne stosowane do produkcji zbiorników i silosów to najczęściej stal węglowa, stal nierdzewna, aluminium oraz, dla wyjątkowo znacznych objętości, beton (RYS. 1) [1-2].
W przypadku przechowywania płynów istotne są dwie cechy:
- odporność na korozję,
- odporność na czynniki chemiczne.
W literaturze często rozważa się także kwestię bezpieczeństwa, z tego względu, że wiele zbiorników produkowanych jest do zastosowań ogólnych. Nie nadają się one do instalacji specjalnego przeznaczenia, a tym samym tak istotne staje się, aby pokrycie zbiornika było odpowiednie dla konkretnego zastosowania.
Nieodpowiednio dobrany zbiornik i brak prawidłowego kontrolowania jego szczelności może doprowadzić do katastrofy. Za przykład można wskazać awarię instalacji stalowej w Indiach.
W 1984 roku w Bhopalu w fabryce produkującej pestycydy rozszczelnieniu uległ zbiornik zawierający izocyjanian metylu. Toksyczny gaz uwolnił się do atmosfery, na skutek czego zmarły dziesiątki tysięcy osób, a teren fabryki został poważnie skażony. Negatywne skutki zdrowotne pojawiały się nawet w następnych pokoleniach.
Bezpośrednią przyczyną tej katastrofy była nieszczelna izolacja, w wyniku czego woda dostała się do zbiornika, gdzie zachodziła reakcja z magazynowaną substancją toksyczną. Na skutek kontaktu tych substancji nastąpił gwałtowny wzrost temperatury, a następnie duży wzrost ciśnienia, który spowodował rozsadzenie zbiornika.
Wydarzenie to miało miejsce ponad 30 lat temu, jednak dowodzi, jak ważny jest zarówno odpowiedni dobór zbiornika do konkretnego zastosowania, jak i kontrolowanie jego szczelności. W celu zwiększenia bezpieczeństwa i żywotności zbiorników stosuje się warstwy ochronne zabezpieczające warstwę nośną przed kontaktem ze znajdującym się wewnątrz instalacji medium, a także chroniące przed czynnikami zewnętrznymi (np. promieniowaniem UV) [1-3].
Rynek środków izolacyjnych
Współcześnie pokrycia składają się z trzech komponentów:
- pigmentu,
- żywicy polimerowej,
- rozpuszczalnika.
Każde z nich nadaje pokryciu konkretną właściwość i dopiero ich mieszanina zapewnia pożądany efekt izolacji.
Zastosowanie pigmentów nie tylko zabarwia powłokę na określony kolor, ale również zwiększa odporność na korozję i adhezję, a także zmniejsza przepuszczalność wilgoci.
Żywica polimerowa to z kolei najważniejszy składnik całej mieszaniny, spajający powłokę oraz nadający jej odporność chemiczną i trwałość oraz wiążący ją na danej powierzchni.
To przede wszystkim na podstawie zastosowanej żywicy polimerowej wyróżnia się rodzaje pokryć, takie jak:
- czysta żywica epoksydowa,
- żywica fenylowa,
- żywica izocyjaniano-epoksydowa,
- alkaliczny krzemian cynku,
- żywica siloksano-epoksydowa [1-2].
Istotne jest, aby możliwie łatwe było stosowanie pokrycia, czyli rozprowadzanie go po powierzchni. Jest to możliwe dzięki zastosowaniu rozpuszczalnika, który ponadto pomaga w reakcji pomiędzy żywicą a składnikami sieciującymi. Rozpuszczalnik po pewnym czasie odparowuje, nie stanowi więc znaczącej części suchej już powierzchni.
Krzemiany cynku generalnie składają się z dwóch podstawowych składników:
- pudru cynkowego o rozmiarach cząstek mieszczących się w granicach 5-7 mikronów oraz
- nieorganicznego lub organicznego spoiwa.
Lepiszcza krzemianowe mogą bazować na wodzie z dodatkiem krzemianu potasu lub roztworu alkoholowego, aby zapewnić reakcję sieciowania.
Zazwyczaj powłoki takie nakładane są jako pojedyncza warstwa, będąca barierą pomiędzy stalą a substancją żrącą. Nie są jednak odporne na silne kwasy i zasady, co oznacza, że pokryte nimi zbiorniki są odpowiednie jedynie dla towarów, których pH waha się w granicach 5,5-10. Najlepszą odporność uzyskuje się w przypadku wysokich zawartości procentowych pyłu cynkowego [3].
Pokrycia bazujące na wodzie to alkaliczne krzemiany cynku, które mogą składać się z rozpuszczonego w wodzie krzemianu sodu, potasu lub litu. Wytwarzanie takich powłok odbywa się poprzez reakcję pomiędzy pudrem cynkowym (pigment) oraz lepiszczem, którym jest żel krzemianowy. Spoiwo powinno ponadto reagować ze stalą, wytwarzając formę cechującą się wybitną adhezją.
Mechanizm sieciowania i otrzymywania powłoki obejmuje trzy główne etapy:
- reakcję inicjacji stanowi zatężenie komponentów poprzez odparowanie wody.
- w drugim etapie reakcja jonów cynku z krzemianem oraz formowanie krzemianu cynku powoduje wytworzenie nierozpuszczalnego filmu powłoki. Chemiczne oraz fizyczne właściwości takiej powłoki są wystarczające, jednakże ma ona porowatą strukturę.
- trzeci etap jest spowodowany występowaniem kwasu węglowego, powstającego w wyniku reakcji dwutlenku węgla z wilgocią na powierzchni powłoki. Kwas węglowy reaguje z wolnymi cząstkami cynku, kończąc formowanie matrycy krzemianu cynku [1-4].
Sieciowanie czy też utwardzanie powłoki następuje w wyniku hydrolizy rozpuszczalnego krzemianu poprzez interakcję z cynkiem skutkującą uformowaniem się nierozpuszczalnego kompleksu krzemianu cynku.
Ogólnie ujmując, proces sieciowania zależy od stosunku ilości krzemianu do zasady, typu metalu alkalicznego oraz stopnia rozdrobnienia cząstek cynku.
Osobnym tematem są pokrycia do zastosowań specjalnych, tj. izolacji wnętrza zbiorników i/lub rur instalacji przepływowych narażonych na działanie gorącego i żrącego medium. Do tego celu stosuje się specjalne rodzaje żywic ftalowych, epoksydowych i estrowych [4-5]:
- żywica ortoftalowa przeznaczona jest do zastosowań w niskich temperaturach pracy i do pokrywania powierzchni narażonych na działanie rozcieńczonych substancji żrących.
- żywica izoftalowa, bazująca na standardowych glikolach, w tym glikolu propylenowym, jest odpowiednia do średnich temperatur pracy i odporna na działanie rozcieńczonych substancji oraz kwaśnych mediów, a także do pracy w niskich temperaturach.
- Niski pik egzotermiczny umożliwia ponadto wytwarzanie grubych laminatów w jednym przebiegu.
Żywicą izoftalową można pokrywać zbiorniki i pojemniki, w których występuje kontakt z żywnością. - żywica IZO-NPG jest odpowiednia do pracy w temperaturach otoczenia oraz z rozcieńczonymi substancjami, w tym kwaśnymi mediami.
Utwardzona żywica nadaje się do kontaktu z żywnością oraz charakteryzuje się bardzo dobrą adhezją do powierzchni pokrytych poli(chlorkiem winylu). - żywica winyloestrowa, oparta na bisfenolu A, może być stosowana do pokrywania zbiorników przeznaczonych do przechowywania wody, kwasów i soli o zmiennej temperaturze pracy, a także alkaliów o temperaturze pokojowej. Zapewnia również odporność na działanie lakierów do stosowania w warunkach korozyjnych w chemicznym przemyśle przetwórczym.
- żywica winyloestrowo-uretanowa łączy cechy żywicy winyloestrowej oraz izoftalowej, czyniąc ją silnie odporną na czynniki chemiczne nawet w wysokich temperaturach pracy.
Szczególną cechą żywic winyloestorowo-uretanowych jest ich odporność na chlorowe środki wybielające do zastosowania w warunkach silnie korozyjnych. Korzystne połączenie odporności termicznej i duże wydłużenie czyni tę żywicę idealną do zastosowań przy zmiennych obciążeniach temperaturą. Główną różnicą w stosunku do żywicy winyloestrowej jest jej budowa chemiczna, dzięki której możliwe stało się połączenie łatwości przetwarzania poliestru z odpornością chemiczną winyloestru. Żywica winyloestrowo-uretanowa bardzo słabo pieni się przy zastosowaniu standardowego inicjatora - nadtlenku MEKP (metylo-etylo-ketonu). Dodatkowo warto wspomnieć, iż żywica ta bardzo szybko przesyca włókno szklane. - żywica winyloestrowo-nowolakowa zapewnia doskonałą odporność termiczną i chemiczną na rozpuszczalniki, kwasy i utleniające media, takie jak chlor. Ma dużą wytrzymałość w wysokich temperaturach pracy.
- żywice epoksydowe, zwane czystymi epoksydami, oparte są na reakcji bisfenolu A z epichlorohydryną, poprzez epoksydowe grupy terminalne z utwardzaczami, posiadającymi polifunkcyjne grupy –NH2, nazywane poliaminami. Takie reakcje prowadzą do otrzymania żywicy bez konieczności usuwania produktu ubocznego, np. wody, dzięki czemu można uniknąć skurczu występującego podczas sieciowania w przypadku tworzyw termoutwardzalnych.
Właściwości usieciowanej czystej żywicy epoksydowej zależą od kilku czynników, do których zalicza się: typ epoksydu, typ oraz ilość utwardzacza, stopień usieciowania oraz ilość dodatków.
Wytrzymałość chemiczna oraz właściwości mechaniczne mogą się znacząco różnić w zależności od konkretnej żywicy.
Czynniki, które mają wpływ na te różnice, to masa cząsteczkowa żywicy, rodzaj utwardzacza oraz pigmentacja i mieszanina rozpuszczalnika.
Zastosowanie żywic epoksydowych o niskiej masie cząsteczkowej skutkuje otrzymaniem powłoki o większej gęstości, z mniejszą liczbą grup hydroksylowych, a tym samym charakteryzuje się lepszą odpornością na wodę i czynniki chemiczne od żywic o średniej masie cząsteczkowej. Te z kolei oferują jednak lepszą wytrzymałość mechaniczną i elastyczność. - żywica fenolowo-epoksydowa jest wielofunkcjonalną żywicą powstałą przez epoksydację żywic fenolowych z epichlorohydryną, wyróżniającymi się wysoką odpornością chemiczną. Jednakże większość z takich izolacji wymaga ogrzewania w temperaturze 50-70°C przez kilka dni w celu osiągnięcia pełnej odporności, co niewątpliwie jest główną wadą stosowania tego systemu.
- żywica izocyjaniano-epoksydowa ma większą masę cząsteczkową wynikającą z usieciowania żywic składnikiem izocyjanianowym. Reakcja ta zachodzi w temperaturze pokojowej. Izocyjanian reaguje z grupami hydroksylowymi żywicy epoksydowej, dzięki czemu otrzymuje się gęsto usieciowaną strukturę z wysoką odpornością chemiczną, zbliżoną do odporności żywic fenolowych, jednakże nieodporną na wysokie stężenie zasad.
- żywica siloksano-epoksydowa bazuje na żywicy otrzymywanej w reakcji cyklicznego krzemianu z pięcioma grupami epoksydu fenolowego. Innymi słowy, są to pokrycia dwukomponentowe bazujące na siloxiranie, opatentowanym polimerze z organiczną/nieorganiczną matrycą. Wspomniany wyżej siloxiran składa się z pierścieni SiO, stanowiących szkielet i formujących termoutwardzalne pokrycie żywiczne z wysokimi właściwościami mechanicznymi oraz odpornością chemiczną. Kombinacja bardzo gęsto usieciowanej struktury z silnymi pierwszorzędowymi wiązaniami sprawia, że żywica ta jest nieprzepuszczalna dla najbardziej agresywnych rozpuszczalników i odporna na działanie kwasów oraz zasad [1-5].
W ostatnim czasie na rynku pojawiła się technologia izolacji zbiorników bazujące na łączących się zaletach dopełniających się rozwiązań. Na przykład dwukomponentowa membrana (kompozyt polimocznikowy) o wysokiej odporności chemicznej i zdolności do mostkowania rys przeznaczona zarówno do hydroizolacji, jak i ochrony konstrukcji betonowych. W czasie mieszania na budowie w materiale tworzy się połączona krzyżowo przenikająca się sieć (IPN), polepszając ogólne właściwości produktu, np. odporność chemiczną czy zdolność mostkowania rys.
W ramach tego rozwiązania, kontrolując gęstość sieciowania, można dobrać właściwości technologii w taki sposób, aby idealnie odpowiadały pożądanej charakterystyce produktu. Ponadto wyróżnia się ono bardzo niską zawartością lotnych związków organicznych (VOC), dzięki czemu nanoszenie materiału jest proste i szybkie – zarówno wałkiem, jak i przez natrysk.
Odporność na wilgoć sprawia, że technologia ta sprawdza się w różnorodnych warunkach aplikacji, co znacznie poszerza jej zakres zastosowań, obniżając jednocześnie ryzyko opoźnień i niepowodzenia. Dzięki właściwościom utwardzania, także w niskich temperaturach, technologia ta umożliwia szybki powrót do użytkowania obiektu. Gwarantuje to wydajną, bezpieczną i ciągłą eksploatację infrastruktury w oczyszczalniach ścieków.
Metody pokrywania powierzchni warstwami izolacyjnymi
Przed przystąpieniem do procesu pokrywania powierzchni warstwami ochronnymi należy odpowiednio przygotować podłoże oraz zapewnić wskazane przez producenta warunki pracy. Powłoka źle nałożona nie zapewnia dobrych właściwości ochronnych.
Podstawową czynnością jest dokładne oczyszczenie powierzchni zbiornika z kurzu, substancji olejnych, wody oraz innych zabrudzeń. Zanieczyszczone podłoże, na które zostanie nałożona powłoka, w krótkim czasie ulegnie zniszczeniu, a nałożona warstwa ochronna nie będzie spełniać swojej funkcji.
Ważnymi czynnikami są temperatura zbiornika i panująca względna wilgotność powietrza w zbiorniku. Temperatura powierzchni zbiornika powinna być co najmniej o 3°C wyższa niż temperatura punktu rosy (punkt rosy to najwyższa temperatura, w której będzie się skraplać wilgoć z atmosfery). Temperaturę materiału, z którego wykonany jest zbiornik, można zmierzyć przy użyciu termometru kontaktowego.
Wygodnym urządzeniem jest także kalkulator punktu rosy pozwalający określić, czy warunki klimatyczne są dopuszczalne do nakładania powłoki. Wilgotność względna mierzona jest za pomocą higrometru. Po spełnieniu warunków temperatury i wilgotności można przygotować mieszaninę roboczą do nakładania.
Bardzo ważne jest, aby składniki powłoki były przechowywane w kontrolowanej temperaturze. Zmieszanie substratów powinno odbyć się w sposób przedstawiony przez producenta, przy czym szczególną uwagę należy zwrócić na zachowane proporcje [6-9].
Sposób nakładania warstwy na powierzchnię zbiornika zależy od jego wielkości:
- w przypadku małych zbiorników przygotowaną mieszaninę wlewa się do środka, zamyka zbiornik i dokładnie obraca, aby żywica dotarła do wszystkich miejsc (tzw. powlekanie rotacyjne),
- w przypadku większych gabarytów powłokę można nakładać pędzlem, wałkiem lub przy użyciu pistoletu natryskowego. Ostatni wariant cechuje się największą efektywnością i dokładnością pokrycia.
Po naniesieniu powłoki zachodzi proces utwardzania wykorzystujący system wentylacji. Nie istnieją szczególne zasady dotyczące wentylacji, jednak pewne kryteria zostały przyjęte z doświadczenia. Dla powierzchni o wymiarach 60 m3 i mniejszych wymiana powietrza powinna zachodzić co minutę, przy powierzchni 60–850 m3 co trzy minuty, przy powierzchni 850-2800 m3 co pięć minut, a powyżej 2800 m3 co 10 minut. Ważne jest także kontrolowanie grubości nakładanej powłoki, na przykład za pomocą miernika grubości.
Najlepsze powłoki to te, których sieciowanie następuje jeszcze w fabryce. Większość producentów skłania się ku takiemu nakładaniu powłok, jednakże proces suszenia następuje już w temperaturze otoczenia, przez co są one narażone na takie czynniki, jak wilgoć czy kurz.
Często się zdarza, że zbiorniki pokryte warstwą ochronną mogą być używane tylko w miejscu ich wytwarzania, gdyż przenoszenie wiąże się ze zniszczeniem pokrycia. Warstwy nakładane w warunkach naturalnych ograniczają możliwość transportu zbiornika ze względu na niebezpieczeństwo zniszczenia bądź rozpadu pokrycia, kiedy jego części są przenoszone [1-3, 6-10].
Natryskiwanie płomieniowe
Dość innowacyjną i zapomnianą metodą nanoszenia powłok jest natryskiwanie termiczne/płomieniowe. Nanoszenie poprzez natryskiwanie tworzyw w stanie ciekłym znalazło szczególne zastosowanie w odniesieniu do wodnych układów dyspersyjnych (dyspersji wodnych – hydrozoli).
Proces formowania wstępnego powłoki z wodnych układów dyspersyjnych obejmuje następujące fazy:
- cząstki polimeru o rozmiarach 0,1-5 mm są otoczone błonką koloidu ochronnego lub emulgatora i rozdzielone wodą; w pierwszej fazie tworzenia się powłoki woda odparowuje (B);
- cząstki zbliżają się do siebie, ale w dalszym ciągu pozostają rozdzielone wodą, a odległość między cząstkami zmniejsza się do rozmiarów kapilarnych (C);
- w wyniku działania sił kapilarnych cząstki zbliżają się nadal i dążą do ściślejszego upakowania, wypierając wodę z koloidem ochronnym i emulgatorem, powierzchnie styku cząstek ze sobą i materiałem przedmiotu powiększają się, rośnie adhezja, a falista powierzchnia powłoki ulega wygładzeniu (D).
Opisany proces dla danego wodnego układu dyspersyjnego zależy głównie od temperatury. Za najniższą temperaturę formowania wstępnego powłoki MFT (ang. Minimum Film Temperature) przyjmuje się temperaturę, w której dany wodny układ dyspersyjny ma zdolność do tworzenia powłoki jednolitej.
Wodny układ dyspersyjny nanosi się na przedmiot z odpowiednio przygotowaną powierzchnią, głównie poprzez natryskiwanie za pomocą pistoletów pneumatycznych z dyszą o średnicy 0,4-0,6 mm, stosując ciśnienie powietrza 0,15-0,20 MPa.
Często po przygotowaniu powierzchni najpierw nanoszona jest tzw. międzywarstwa (A), a dopiero później powłoka z tworzywa, jedno- lub wielokrotnie, w zależności od potrzeb.
Jako międzywarstwę stosuje się powłokę metalową o grubości 25-50 mm, wykonaną z materiałów ceramicznych o grubości do 200 mm lub z emalii. Proces natryskiwania termicznego przedstawiono na RYS. 2-5 [11-16].
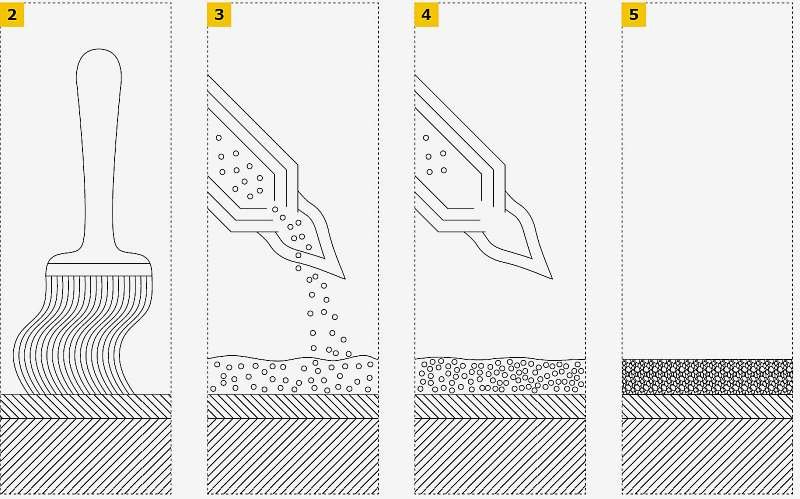
Rys. 2-5. Procedura nakładania powłoki ochronnej metodą natryskiwania płomieniowego; rys.: archiwum autorów
Formowanie ostateczne powłoki polega na jej suszeniu na ogół przy nagrzewaniu promiennikowym, a następnie na nagrzaniu przedmiotu z wysuszoną powłoką do temperatury powodującej topnienie tworzywa, co ostatecznie konstytuuje adhezję do materiału przedmiotu i kohezję powłoki.
Nanoszenie natryskowe stosuje się przede wszystkim do wodnych układów dyspersyjnych PTFE i kopolimeru PVC/VA.
Typowe zastosowania warstw natryskiwanych to tworzenie powłok odpornych na ścieranie, erozję gazową i korozję albo odznaczających się podwyższonymi właściwościami ślizgowymi, izolacyjnością cieplną lub podwyższoną przewodnością cieplną i elektryczną.
Dodatkowe efekty można uzyskać, stosując specjalne procedury technologiczne. Porowate warstwy można uszczelniać, przesycając je tworzywami sztucznymi.
Źródłem ciepła stosowanym w tej technice jest płomień gazowy, najczęściej ze spalania acetylenu w tlenie, o temperaturze ok. 3000°C, a natryskiwane cząstki osiągają prędkość 100-350 m/s. W zależności od postaci materiału powłokowego (proszek) wyróżnia się odpowiednie konstrukcje palników.
Natryskiwanie na gorąco stosuje się do elementów, od których wymaga się wysokiej odporności na ścieranie, żaroodporności, odporności na korozję i erozję, udarności. Pokrywane elementy podgrzewa się do temperatury osiągającej 150-500°C, nakładając warstwę wstępną o grubości 0,2-0,5 mm w celu ochrony powierzchni podłoża przed utlenieniem [14, 17-20].
Przykłady zastosowania metod nanoszenia powłok
Zbiorniki transportowane drogą morską wymagają dodatkowej ochrony przed wodą słoną. W przypadku rozszczelnienia takiego zbiornika magazynującego chemikalia wielkość skażenia wód słonych byłaby ogromnym problemem dla środowiska. Często stosuje się na takie zbiorniki powłoki na bazie żywic siloksano-epoksydowych, które charakteryzują się wysoką odpornością na agresywne rozpuszczalniki.
- Powłoki epoksydowe, dzięki wysokiej odporności na kwasy nieorganiczne, alkalia, wodę, benzynę i oleje, znajdują zastosowanie w takich obiektach, jak zbiorniki na wodę, oleje, ścieki, konstrukcje mające kontakt z atmosferą morską, konstrukcje narażone na zachlapania i opary substancji chemicznych [1-5].
- Powłoki krzemianowe nie są zalecane jako warstwy ochronne przed agresją chemiczną, natomiast rekomendowane są w obiektach, których powierzchnie narażone są na wysokie temperatury.
- Powłoki na bazie żywic izocyjaniano-epoksydowych wskazane są dla ochrony powierzchni przed rozcieńczonymi substancjami.
W przypadku, gdy podczas nanoszenia warstwy powierzchniowej podłoże nie ulega roztopieniu, proces jest natryskiwaniem cieplnym, a połączenie jest wyłącznie mechanicznym, z częściowym udziałem dyfuzyjnego.
Natryskiwanie cieplne jest grupą metod, w których stopiony lub ciastowaty materiał powłoki jest nanoszony na powierzchnię przygotowanego wcześniej podłoża.
Na powłoki stosuje się epoksydy, poliamid 6, poliamid 66, poli(tetrafluotoetylen), poli(fluoroetylenopropylen), poli(fluorek winylidenu). Powłoki z tych materiałów nakłada się na metale, ceramikę, szkło, niektóre maty plastyczne, drewno i papier.
Proszek materiału pokrycia jest umieszczany w płomieniu gazowym, w łuku elektrycznym lub plazmowym, gdzie następuje jego stopienie i rozdrobnienie przez strumień gazu, takiego jak argon, azot lub sprężone powietrze albo w płomieniu gazowym.
Strumień gazu, porywając ciekłe cząstki o średnicy 0,01-0,05 mm, kieruje je na powierzchnię pokrywanego elementu, o którą uderzają, chłodzą się na niej i łączą się z nią. Na podłoże przekazywane jest niewiele ciepła, w wyniku czego jego temperatura podnosi się jedynie do 100-250°C.
Natryskiwanie cieplne nie powoduje zatem zmian strukturalnych lub odkształcenia plastycznego podłoża, a tego typu pokrycia mogą być m.in. stosowane do cienkich i precyzyjnych elementów oraz do materiałów podatnych na oddziaływanie ciepła, np. do materiałów polimerowych. Natryskiwana powłoka ma strukturę warstwową o różnej koncentracji porów, która może dochodzić nawet do 20%.
Grubość powłok jest na ogół większa niż grubość otrzymywana innymi technikami powlekania powierzchni i zwykle mieści się w przedziale 0,05-2,5 mm, chociaż może sięgać do 12 mm. Uzyskiwane powłoki mogą być również cieńsze niż w przypadku pozostałych metod [1, 4-5, 8-12].
Podsumowanie
Omówione wyżej rodzaje pokryć mają szerokie zastosowanie. Pozwalają na ochronę zbiorników przed transportowanym medium, a także zabezpieczają przed wpływem czynników atmosferycznych.
Powłoki wewnętrzne są niezwykle istotne podczas transportu oraz przechowywania substancji żrących, stężonych kwasów oraz wody o wysokiej temperaturze. Zbiorniki, w których umieszcza się tego typu substancje, muszą być tak przygotowane, aby zapewnić bezpieczeństwo personelu zajmującego się transportem oraz środowiska, np. wody morskiej podczas transportu statkami.
Literatura
- N. Ackermann, "Choosing the correct coatings for cargo tanks, Anticorrosion Service", Trieste, Italy, 1998.
- P. Vodak, "Coatings Protection against Tank Corrosion Translates into Longer Lifespan", Industrial WaterWorld.
- T.N.Rhys-Jones, "Application of thermally sprayed coatings systems in aero engines". Materiały Konferencyjne ITSC’89, Londyn 1989, Abington Publishing, Vol. 1 s. 87-100.
- John E. McAlvin, AOC, LLC, Technical Paper, "Heat Resistant Vinyl Ester Resins for Composite Applications".
- William R. Slama, "Polyester and Vinyl Ester Coating", „Journal of Protective Coatings & Linings", Technology Publishing Company, May 1996/89.
- G.R. Heath, P.A. Kammer, "The high temperature erosion behavior of arc-sprayed coatings", Materiały Konferencyjne ITSC’96, Essen 1996, DVS Berichte, s. 76-79.
- S.J. Yankee, B.J. Pletka, H.A. Luckey, W.A. Johnson, "Process for fabricating hydroxylapatite coatings for biomedical applications. Thermal Spray and Application", Materiały Konferencyjne NTSC’3, Long Beach, CA, USA 1990, s. 433-438.
- Prospekt reklamowy firmy AMIL, 2004 rok.
- S. Kostrzewa, B. Nowak, "Podstawy regeneracji części pojazdów samochodowych", WKŁ, Warszawa 1979.
- E. Chlebus, "Innowacyjne technologie Rapid Prototyping w rozwoju produktu", Oficyna Wydawnicza Politechniki Wrocławskiej, Wrocław 2003.
- W. Milewski, "Elektrometalizacja", WNT Warszawa 1968.
- E. Chlebus, "Techniki komputerowe CAX w inżynierii produkcji". WNT, Warszawa 2000.
- J. Dziubiński, W. Mazur, "Zastosowanie natryskiwania łukowego do regeneracji elementów hydrauliki siłowej", "Eksploatacja Maszyn" 2-3/1987, s. 26-28.
- B. Aumueler, D.W. Schneider, K. Eisnegg, H. Krauss, W. Kroemmer, "Herstellung von Kleinserienwerkzeugen fuer die Blechumformung durch gespritzte Schichten in Schalen-Bauweise", Materiały Konferencyjne ITSC’02, Essen 2002, s. 149-152.
- P. Białucki, R. Kaczmarek, S. Kozerski, "Analiza wytrzymałości zmęczeniowej elementów natryskiwanych cieplnie", "Eksploatacja Maszyn" 2-3/1987, s. 19-20.
- A. Seils, "Korrosionsschutz von Stahlbauwerken durch Metallspritzen. Thermische Spritzverfahren", DVS‑Sondertagung, Saarbrucken 1963, s. 78-88.
- E. Kretzschmar, "Metall-, Keramik- und Plastspritzen", VEB Verlag Technik, Berlin 1969.
- A. Drygas, "Flammgespritzte Verschleissschutzbeschichtung in Kaplanturbinen", Materiały Konferencyjne ITSC’90, Essen 1990, DVS Berichte, s. 78-81.
- A. Sikorski, P. Białucki, S. Kozerski, "Properties of ferrochromium thermal sprayed layers with different carbon contents", Materiały Konferencyjne ITSC’96, Essen 1996, DVS Berichte, s. 65-67.
- J. Wilden, T. Schick, A. Wank, "Thermal spray moulding - production of microcomponents", Materiały Konferencyjne ITSC’02, Essen 2002, s. 144-148.